|
This topic comprises 2 pages: 1 2
|
Author
|
Topic: Trailers
|
|
|
|
|
|
|
|
|
John Pytlak
Film God
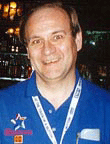
Posts: 9987
From: Rochester, NY 14650-1922
Registered: Jan 2000
|
posted 09-16-1999 01:25 PM
A good way to determine the cause of any unsteadiness is to pull the aperture from the projector, and project the actual print film perforations on the screen. With most projectors, pulling the aperture will show at least the edges of the perfs on one side or the other of the print. Do this with the non-anamorphic "flat" lens (greatest magnification) and the screen masking pulled back so you can see the perfs imaged on the screen.If the print perfs are "rock steady" but the picture still has jump and weave, the print stock and projector are likely NOT the source of the unsteadiness. If the print perfs are unsteady, do the same test with a roll of SMPTE 35-PA (RP40) test film to see if the unsteadiness was the print film (if RP40 is steady) or the projector (if RP40 is also unsteady). If the print perfs are steady, notice whether the framelines and edges of the image are moving relative to the print perfs. If the whole image tends to be "dancing", then the unsteadiness was probably introduced during printing. Sometimes you can actually see the image of the round edges of the BH-perf of the printing negative move relative to the more rectangular KS-perf of the print film. Camera unsteadiness is usually seen as a movement of one frame relative to an adjacent frame, across the frameline. Frame the projector so the print frameline is across the center of the screen. You can then see how the camera positioned one frame relative to the next frame. Any side-to-side movement or "bounce" across the frameline during a scene was likely introduced in the camera. If everything EXCEPT the image itself is steady, it may just be that the camera was handheld or not mounted rigidly. Trailers are likely to be less steady than the feature film because there are usually more "generations" of printing between the camera negative and the final prints. Another factor that has affected steadiness is that most labs no longer edge-wax prints, because of increased environmental restrictions on the solvents used. Kodak process specifications and SMPTE Recommended Practice RP151 specify edge-waxing of 35mm prints to reduce friction in the projector gate. Properly lubricated prints are steadier, quieter, and much less prone to projector abrasion, gate deposits, and dusting/shedding.
| IP: Logged
|
|
|
|
|
John Pytlak
Film God
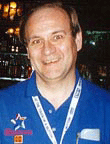
Posts: 9987
From: Rochester, NY 14650-1922
Registered: Jan 2000
|
posted 09-17-1999 08:00 AM
Although Kodak had made polyester (ESTAR) film base since the 1950's, most of it was used for "special venue" films like IMAX films and films used at theme parks. Polyester prints were also preferred for specialized applications like the 16mm and Super-8 prints used on airplanes.Kodak did NOT lead the conversion to polyester. The distributors and theatre owners felt there would be advantages, and requested the conversion. The January 1991 NATO News reported: "The board also resolved, at the (Technical Advancement) committee's request, to approve and recommend the use of polyester film, which is thinner (allowing more film per reel) and less likely to break". Other film manufacturers encouraged the conversion to polyester, with pictures such as "The Fugitive", "Free Willy", "Secret Garden" and "The American President" being released on their new stocks. During this time period, Kodak publically expressed concerns about an excessively rapid conversion of the industry to polyester base. In October 1993, the Intersociety Committee for the Enchancement of Theatrical Presentation sponsored a project to study the performance of polyester prints in theatres. Kodak provided polyester film for the Warner Bros. picture "Mr. Wonderful", and followed up on the performance of the prints with visits to the lab, exchanges, and theatres. A comprehensive written survey questionnaire was sent to 250 theatres playing the polyester prints. I presented the results of the study at ShoWest in March 1994. Although most theatres reported no problems, and even preferred the performance of the polyester prints, a few theatres DID have problems, including static, dusting, and slippery rolls. Many projectionists also expressed concern about the strength of polyester and the risk of equipment damage. Despite these concerns, the conversion continued because the advantages polyester offered (thinner film, resistance to perforation damage, more "friendly to the environment") seemed to outweigh the disadvantages. Kodak had to invest hundreds of millions of dollars to make the conversion to 100% polyester for release prints, building a completely new base manufacturing plant. Kodak continued to address the known concerns of polyester (e.g., increased static charging, projector abrasion), which led to the recent introduction of Kodak Vision Color Print film. At its own expense, Kodak is also supplying all its laboratory customers a special antistatic process additive that enhances the antistatic performance of all films. Kodak continues to encourage laboratories to properly lubricate prints, per Kodak processing specifications and SMPTE Recommended Practice RP151. And Kodak continues efforts to further improve film performance, with millions of feet of the latest improvement being tested now.
| IP: Logged
|
|
Bruce McGee
Phenomenal Film Handler
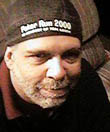
Posts: 1776
From: Asheville, NC USA... Nowhere in Particular.
Registered: Aug 1999
|
posted 09-17-1999 08:44 AM
This is an intresting thread. I have several Estar prints in 16mm. Some are in color. I have run them over and over in the last 25 years. They continue to run smoothly. I have never seen any shedding from them either. Yes, I am aware of the difference in film movement speed.The only gripe I had with Estar is its unwillingness to break if something happens. Once I had a new print arrive on Estar. It was apparently slit improperly and was just a bit wider than 16mm in a small area. Anyway, the film stopped in the gate, and broke the teeth off the claw. I was impressed with the durability of the base stock, and I have never had the problems with easily-scratched emulsion on Estar either. My new 35mm trailers on Polyester stock jump and bounce like crazy on my Holmes. I am looking forward to trying Film-Guard. I ran a loop of polyester 35 through my projector for about an hour last night. There was a small snowstorm under the intermittant, and the only damage to the film I noticed was light abrasions on the edges of the film where the springs in the gate actually touch the perforations. The picture area is black with no noticable new scratches. I think that if Film-Guard does what it is ment to do, this shedding thig will soon be history.
| IP: Logged
|
|
|
|
All times are Central (GMT -6:00)
|
This topic comprises 2 pages: 1 2
|
Powered by Infopop Corporation
UBB.classicTM
6.3.1.2
The Film-Tech Forums are designed for various members related to the cinema industry to express their opinions, viewpoints and testimonials on various products, services and events based upon speculation, personal knowledge and factual information through use, therefore all views represented here allow no liability upon the publishers of this web site and the owners of said views assume no liability for any ill will resulting from these postings. The posts made here are for educational as well as entertainment purposes and as such anyone viewing this portion of the website must accept these views as statements of the author of that opinion
and agrees to release the authors from any and all liability.
|