|
|
Author
|
Topic: CDS Digital Sound
|
|
Ian Price
Phenomenal Film Handler
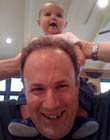
Posts: 1714
From: Denver, CO
Registered: Jun 99
|
posted 01-26-2000 02:04 PM
CDS was encoded on the film in the area that was the analogue soundtrack. CDS sounded great. The only problem was that when the digital failed there was no backup analogue track. They used to send each theatre a 2nd analogue print for emergencies. I ran The Doors on 35 mm at the Coronet in Los Angeles for a week. It was great. Then we ran T2 in 70 mm at the Continental in Denver. The soundtrack failed after a couple of weeks and I never heared about CDS Digital again. They had to have two kinds of prints, CDS and analogue. The industry hates duel inventory. Afew years later I was opening Downtown Plaza in Sacramento. We had 7 old movies we were running for the public for free. One of them was T2. I built them up in a hurry because we had no time. I hit the screen and the sound was Shuuu..... The first reel was CDS. Bobby Pinkston was the fellow who ran the CDS program at ORC. He is now with Dolby. I do have one CDS poster in my office as a reminder.
| IP: Logged
|
|
John Pytlak
Film God
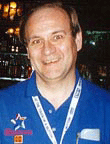
Posts: 9987
From: Rochester, NY 14650-1922
Registered: Jan 2000
|
posted 01-26-2000 02:29 PM
In the mid-1980's, John F. Allen demonstrated digital sound in a theatre environment by interlocking a projector with a video recorder playing PCM digital sound. Showings of "Fantasia" with digital sound were very successful, but this "double system" was not considered commercially viable for large releases.Cinema Digital Sound (CDS) was the first commercial system to print a multi-channel digital soundtrack (bits) directly on the film. It was a joint project between Kodak and Optical Radiation Corporation (ORC). To a large extent, it led the way in convincing film makers, distributors and exhibitors that digital sound was viable in theatres. CDS was used for both 35mm and 70mm prints. The first major release was "Dick Tracy" in June 1990. For 35mm prints, the CDS track was printed in the "protected" area used for analog sound, to wisely avoid projector abrasion and wear of the digital data. But by eliminating the analog soundtrack, "dual inventories" of prints were required, and there was no analog backup if the digital sound system failed. Some early (fixable) hardware problems gave CDS a "black eye" when the system failed without having analog backup. By 1992, Dolby and DTS came out with their systems, and CDS became history. It's "failure" was really a success story for film, as CDS paved the way for today's digital sound systems.  Perry Sun's "Movie Sound Page" has a good description of CDS written by Bobby Henderson. Here is the link: http://www/moviesoundpage.com/msp_cds.htm Another private web page has the original CDS brochure, specifications, and photos: http://members.aol.com/cds3570/ ------------------ John P. Pytlak, Senior Technical Specialist Worldwide Technical Services, Professional Motion Imaging Eastman Kodak Company Research Labs, Building 69, Room 7419 Rochester, New York, 14650-1922 USA Tel: 716-477-5325 Fax: 716-722-7243 E-Mail: john.pytlak@kodak.com
| IP: Logged
|
|
|
|
|
John Pytlak
Film God
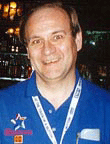
Posts: 9987
From: Rochester, NY 14650-1922
Registered: Jan 2000
|
posted 01-27-2000 02:46 PM
It is well known that the edges and perforation area of the print are abraded by certain projector components. Most good equipment designs take great care to minimize any abrasive contact with the picture or analog soundtrack area of the film. Cinema Digital Sound took the "good engineering" approach of printing the digital data where it was least likely to be abraded or damaged, which was in the already "protected" analog soundtrack area. Projector wear and abrasion can be a problem with digital tracks printed along the edges or between the perforations of the film. Sooner or later, enough damage will occur to cause data error rates to increase. A proven way of reducing projector abrasion is proper print lubrication, per Kodak's processing specifications (H-24.02, H-24.09) and SMPTE Recommended Practice RP-151. Unfortunately, edge-waxing is rarely done anymore because of environmental restrictions on the solvents used to apply the wax. The design, materials, and finish of the projector gate and sprocket shoe greatly affect projector wear. Proper cleaning and maintenance (alignment, tensions) of the film path is also very important to reducing projector abrasion, and the dusting/flaking of prints. ------------------ John P. Pytlak, Senior Technical Specialist Worldwide Technical Services, Professional Motion Imaging Eastman Kodak Company Research Labs, Building 69, Room 7419 Rochester, New York, 14650-1922 USA Tel: 716-477-5325 Fax: 716-722-7243 E-Mail: john.pytlak@kodak.com
| IP: Logged
|
|
|
|
|
|
|
|
All times are Central (GMT -6:00)
|
|
Powered by Infopop Corporation
UBB.classicTM
6.3.1.2
The Film-Tech Forums are designed for various members related to the cinema industry to express their opinions, viewpoints and testimonials on various products, services and events based upon speculation, personal knowledge and factual information through use, therefore all views represented here allow no liability upon the publishers of this web site and the owners of said views assume no liability for any ill will resulting from these postings. The posts made here are for educational as well as entertainment purposes and as such anyone viewing this portion of the website must accept these views as statements of the author of that opinion
and agrees to release the authors from any and all liability.
|