|
This topic comprises 2 pages: 1 2
|
Author
|
Topic: Interlock setup
|
|
John Pytlak
Film God
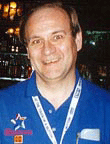
Posts: 9987
From: Rochester, NY 14650-1922
Registered: Jan 2000
|
posted 02-11-2001 06:20 PM
I don't favor the practice of interlocking, except as a last resort, but the rollers on poles idea seems very prone to misalignment. Do the poles have heavily weighted bottoms, so they don't move or tip over?------------------ John P. Pytlak, Senior Technical Specialist Worldwide Technical Services, Entertainment Imaging Eastman Kodak Company Research Labs, Building 69, Room 7419 Rochester, New York, 14650-1922 USA Tel: 716-477-5325 Cell: 716-781-4036 Fax: 716-722-7243 E-Mail: john.pytlak@kodak.com Web site: http://www.kodak.com/go/motion
|
|
|
|
|
|
John Eickhof
Jedi Master Film Handler
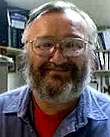
Posts: 588
From: Wendell, ID USA
Registered: Jan 2000
|
posted 02-11-2001 11:18 PM
Come on Brad, you know that in the normal 'booth' environment of today, the result of no snafus when interlocking would be rare! I agree with John P, that multi print screenings are more productive especially as far as the film companies are concerned, and the 'have it when you want it' attitude of the theatre going public! I must commend you on the rather interesting interlock you guys pulled off! However, I want to know two things...First, how long was your thread-up leader and how long did it take to fully lace the system? And second, how long was the feature you ran, and obviously, all projectors were equipped with sych motors on the same phase?------------------ John Eickhof President, Chief Slave Northwest Theatre Equipment Co., Inc. P.O.Box 258 Wendell, ID. 83355-0258 208-536-5489 email: jeickhof@nteequip.com
|
|
|
|
|
|
Bill Purdy
Expert Film Handler
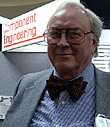
Posts: 139
From: Seattle, WA
Registered: Oct 1999
|
posted 02-12-2001 10:15 AM
I agree with Brad's "Awwwwww, come on John. Interlocking is fun and "done right" will not damage the film in any way whatsoever."I smile every time I remember a set-up in the old "Crest" theatre in north Seattle. Let's say that we are starting in house #1. From an old Potts platter (the ones that used Chrysler auto distributor points), through the first AA II, across the ceiling, through a hole in the wall, across the manager's office, a left turn and down a hall way, a right turn, through another hole in a wall, across a small booth, through the second AA II to take-up on a Drive-In platter. The two automations were totally different and special interface boxes had to be made. The building was undergoing alterations with all the attendant dust so we put a pair of opposed anti-static brushes in the middle of the run which really worked well. There was enough film in the air that it took 51 seconds from screen to screen which means a length of about 96 feet because this was in 70mm! Yup, it is fun! ------------------ Bill Purdy Component Engineering
|
|
John Pytlak
Film God
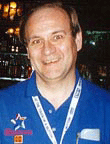
Posts: 9987
From: Rochester, NY 14650-1922
Registered: Jan 2000
|
posted 02-12-2001 11:31 AM
Bill Again, "Done Right" is the big question mark. One badly aligned guide roller, or poor tensioning that drags the film across the floor, will forever leave its mark on the print. At least KODAK VISION Color Print film will not attract dirt on all that free-hanging film (2200 feet for the 16 screen world record, 96 feet for yours) with a static charge, because of it's transparent conductive backing layer. Older film was a shocking "dust magnet". I can understand the need to interlock when a picture like "Hannibal" is selling out, and you haven't sold any tickets for the "dog" playing next door. But the scheduling flexibility and lower risk of having multiple prints for a hit movie is hard to argue with. ------------------ John P. Pytlak, Senior Technical Specialist Worldwide Technical Services, Entertainment Imaging Eastman Kodak Company Research Labs, Building 69, Room 7419 Rochester, New York, 14650-1922 USA Tel: 716-477-5325 Cell: 716-781-4036 Fax: 716-722-7243 E-Mail: john.pytlak@kodak.com Web site: http://www.kodak.com/go/motion
|
|
|
John Pytlak
Film God
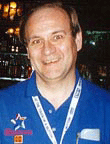
Posts: 9987
From: Rochester, NY 14650-1922
Registered: Jan 2000
|
posted 02-12-2001 12:31 PM
The problem of static attraction of dirt with older films was not the airborne dirt, but dirt attracted to the print when is got close to a dirty surface like the floor or an unkempt rewind bench. You could literally watch dust and dirt "jump up" to the highly charged film. Fortunately, the new conductive VISION print stocks quickly dissipate any dirt-attracting static buildup. I totally agree that in addition to keeping the booth clean, on-line film cleaning is the best way to keep prints looking good, and avoid winding in abrasive particles that eventually will cause cinch marks. An on-line film cleaner for each projector is a good investment in "doing film right". ------------------ John P. Pytlak, Senior Technical Specialist Worldwide Technical Services, Entertainment Imaging Eastman Kodak Company Research Labs, Building 69, Room 7419 Rochester, New York, 14650-1922 USA Tel: 716-477-5325 Cell: 716-781-4036 Fax: 716-722-7243 E-Mail: john.pytlak@kodak.com Web site: http://www.kodak.com/go/motion
|
|
|
All times are Central (GMT -6:00)
|
This topic comprises 2 pages: 1 2
|
Powered by Infopop Corporation
UBB.classicTM
6.3.1.2
The Film-Tech Forums are designed for various members related to the cinema industry to express their opinions, viewpoints and testimonials on various products, services and events based upon speculation, personal knowledge and factual information through use, therefore all views represented here allow no liability upon the publishers of this web site and the owners of said views assume no liability for any ill will resulting from these postings. The posts made here are for educational as well as entertainment purposes and as such anyone viewing this portion of the website must accept these views as statements of the author of that opinion
and agrees to release the authors from any and all liability.
|