|
This topic comprises 2 pages: 1 2
|
Author
|
Topic: Technical help needed!
|
Bruce McGee
Phenomenal Film Handler
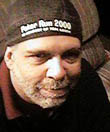
Posts: 1776
From: Asheville, NC USA... Nowhere in Particular.
Registered: Aug 1999
|
posted 05-24-2001 06:25 PM
I got a break in my financial woes today.  I am going to do maintenance on a pizza parlor projection equipment. And Get Paid For It! They want me to do some maintenance on their Century SA with an R4 soundhead, ORC platter (model yet unknown,) a Kneisley Xenex II lamphouse (size yet unknown,) and general cleaning of the heat sinks on their Smart sound system with JBL power amps. Today, I watched the operator thread-up, noticing that his leader was on the floor, and he was stepping all over it while we talked... He has heard of FilmGuard and wants me to get a bottle. My question here is: Help! I know how to clean a Holmes, but it is not a real projector like the SA/R4. I think that the theatre does not have anything to use for cleaning, and I am sure that the projector has not been oiled or maintained. I bet he has no oil for the intermittent there either. Since I have WebTV, I cant download any of the manuals here on Film-Tech, so can you guys enlighten me on the SA? I am told that it's a good machine. I turned it over by hand, and other than a tic in the intermittent (low on oil) it is smooth. There is another SA sitting here. Dont know if it has been cannabalized or not. They want a couple of hours of work on this. Got any suggestions what I should charge? Please be realistic. This is a small town, an old abandoned theatre, with a leaky roof-patch job under-way. I sure dont want to price myself out of a hopefully good situation here. I have all the basic tools. I dont know if they have any sprockets or anything like that. This machine was installed around 1971. Someone has worked on it. There is a fairly new motor on it. When this theatre was open years ago, it was the Merrimon Twin. I knew all the people that worked there. But this is the first time that I have actually touched the set-up. The owner seemed relieved that I came in and offered to help. I have a feeling that this theatre is the place that the 2nd run houses send all their junky prints. The owner said that he rarely gets a decent print of anything, and just has to run what he gets. After watching the threading, I think they need help. Not a projectionist, but help. I appreciate any information that I might get here. Thanks in Advance!! Bruce, Newbie-Tech.
| IP: Logged
|
|
|
|
Jon Bartow
Master Film Handler
Posts: 287
From: Massachusetts
Registered: Nov 1999
|
posted 05-25-2001 07:31 AM
Bruce, In case you don't get John's CD-ROM in time here are a few things to start with: -Change the oil in the intermittent (a small screw at the bottom of the intermittent on the film side is the drain plug). Please, please, please only put projector oil back in. Also put a drop or two on the upper and lower feed sprocket shafts (under the little covers) -Remove any old, dry grease from the gears and replace with new grease. But before regreasing, check all of the gears for brocken teeth. -check the belt(s) for wear, replace if worn or cracked -once greased and oiled turn the flywheel over by hand. It should turn very easily, with little resistance. If there is resistance then you could have bad bearings or a misaligned shaft/intermittent -If you are going to clean the inside/outside of the projector do it before putting new grease/oil in and use alcohol, just keep it away from the bearings, it will dry them out (= death to bearings)-That Kniesly lamphouse has a GLASS reflector in it. Be very carefull with this thing, it is fragile. Don't open the lamhouse for several minutes after the lamp has been on. The sudden inrush of cold air can crack the reflector. However that glass reflector puts out a very nice light. -Double check the lamphouse working distance (I think that it is 34" for that particular setup, but I could be wrong) and alignment These are only a few things to start with. Have fun! Jonathan
| IP: Logged
|
|
Trevor Bailey
Expert Film Handler
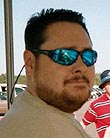
Posts: 113
From: Woonsocket, RI
Registered: Jun 99
|
posted 05-25-2001 04:29 PM
Bruce,Since Jon B. talked about the visual side of things, I'll mention the audio side. I don't know your skill level, so if this is old-hat...maybe someone else will benefit. Not knowing the exact models of the sound equipment, it seems you have at least a center-surround system. A good a-chain can made a tremendous difference in the sound you hear in the auditorium. You'll need a two channel oscilloscope (20MHz minimum if I remember correctly) and preferably a real time analyzer (RTA). You'll also need some test film loops (at a minimum): Dolby tone, Buzz track, Cross talk, and pink noise. Most good sound system installation manuals contain a step by step a-chain procedure (for the general procedure use a Dolby manual, they are great with lots of illustrations). On a new account I like to check the b-chain as well. This will require the RTA, a calibrated microphone (there are also multi-mic systems available) and a pink noise generator. Before you present a price to your prospective client, make sure you have had a chance to read the a-chain and b-chain procedures. They are not five minute jobs if done properly. And if you are new to this, you can expect to spend a fair amount of time "playing" to get a feel for how things need to be. Good luck!
| IP: Logged
|
|
|
Bruce McGee
Phenomenal Film Handler
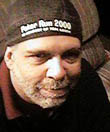
Posts: 1776
From: Asheville, NC USA... Nowhere in Particular.
Registered: Aug 1999
|
posted 05-25-2001 07:37 PM
Thanks everyone for your responses!John: If I got the CD ROM, what could I run it on? As for the scope. I have a nice B&K Dual-trace scope here The theatre has nothing in house in the form of oil, or spare parts, except for a junked SA, and it is missing its intermittent. I dont have any test-loops, etc. either.
This job is going to be interesting if I end up doing it.
| IP: Logged
|
|
|
|
|
|
John Eickhof
Jedi Master Film Handler
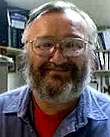
Posts: 588
From: Wendell, ID USA
Registered: Jan 2000
|
posted 05-29-2001 10:52 PM
You won't be able to do a proper call without test films!I also advise a GOOD analog DB meter, such as the Simpson 260 series multi-meter. (The standard of the sound business) It is most likely a mono house,regardless if it is or not, clean all sound optics (in place) remove and REPLACE the exciter lamp! then adjust it for maximum light on the cell or PEC. (Place a white card in between the cell and the optic lens tube, then adjust the lamp by loosening the two screws that hold the exciter lamp bracket, then move it up or down for maximum brilliance of the slit image) the R-4 reproducer was originally chain driven (both motor & projector) Make sure the chains are slightly slack, not tight like timing belts. Lube the idler roller on the projector drive chain, as well as put a couple drops of oil in the cup behind the large drive sprocket from rear (non film) side. (This lubricates the sound sprocket shaft, bronze bushings) If film sprockets are worn, reverse them on the shafts, also if it is a platter or large reel set-up, be sure to remove the upper sprocket shaft and lightly clean the galding off the shaft with crocus cloth (800 grit) then clen, lube with oil and put back together. Be sure to lube the main drive gear with lots of grease! I advise a couple drops of oil on all gear surfaces too. Check film trap for wear on parts, and that the lateral guide roller is free moving and the inner portion slides aesily on the shaft. Check lenses for burns, stars, or other damage, Drain & re-fill the intermittent, clean all lamp fans and the reflector. Clean any cooling fans on the rectifier. (power supply) Look for damage to the bulb, ie: darkening, pitting, etc..) Clean out any vents in the sound equipment, amps, etc. Pull, clean contacts, and install all sound cards in the processor. Run Buzz loop to check lateral film alignment, then run 9 Kc Loop to check HF output, followed by 1 Kc. loop and reading the output of the amp with the meter, you should have no more than 5 db difference between the 9 Kc and 1 Kc loops. (For mono only, if there is a difference of more than 5 db, you will have to re-focus the optics using the 9 KC loop) If stereo, run Buzz then CAT-69 Tone loop, align pre-amp levels, also, run 9 Kc loop and check HF output. Check Surround level and delay with CAT-151 loop and adjust surround level as necessary. (Listen in auditorium for equal level between surrounds & screen) If you think it needs a B chain alignment, plan on a couple more hours work! A typical GOOD service call on a single machine set up takes about 3-4 hours. Don't rush it! Good luck!!------------------ John Eickhof President, Chief Slave Northwest Theatre Equipment Co., Inc. P.O.Box 258 Wendell, ID. 83355-0258 208-536-5489 email: jeickhof@nteequip.com
| IP: Logged
|
|
Mark Gulbrandsen
Resident Trollmaster
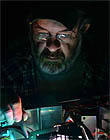
Posts: 16657
From: Music City
Registered: Jun 99
|
posted 05-30-2001 02:33 PM
Bruce, If you are seriously thinking about doing service you need to be properly equipped beforehand. The fact that you are tinkering with anothers livelyhood shouldn't be taken lightly. You should also be able to offer the finest service available,period! This does mean having the proper test equipment, test films, and tools. It costs allot of money to equip your self but you HAVE to do so in order to provide the best service. Your knowledge is also your ticket to doing the best service possible so hone it to the equipment you will be working on. Minor repairs are one thing but normal booth maintainance requires that you know what to do, how to do it, and that you are ready to attack whatever you find wrong in a short time. If the problem can't be corrected easily then you need to now how to make it fly with bubble gum and paper clips at least temporarily. If you find a major problem you may need to know how to completely strip this machine down in order to replace say, the verticle shaft. You will need other parts to be able to correctly replace the shaft....bearings, spring washers, spacers, etc. Don't read this as a discouragement as I would never discourage anyone from enterint this field, I would only encourage them. I only wanted to present the more serious side of this buisness which many don't stop to think about. Mark @ GTS (Third slave in line) Thankfully not the first in line!
| IP: Logged
|
|
Bruce McGee
Phenomenal Film Handler
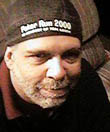
Posts: 1776
From: Asheville, NC USA... Nowhere in Particular.
Registered: Aug 1999
|
posted 05-30-2001 11:02 PM
Thank you all for your comments. Have no fear that I will go in and "tinker" away... I never do things if I dont thoroughly understand, or, have the precise equipment, to do the job correctly. All I planned to do for now is go in and clean the daylights out of the SA, and the associated equipment. I have no intentions of attempting any adjustments of the sound lens, or the xenon lamp. Since I have no test films, I wouldn't do that anyway. The projector in question is filthy. It needs a thorough cleaning and oiling. It has not been oiled in almost a year, according to the owner. They play 2 shows a day when they have 35mm--which is about one-fourth of the schedule. I know that the intermittent sprocket is hooked. I plan to reverse the other sprockets as well. The sound is fairly decent in the theatre. There is not much for me to do here. As I said before, there is very little money available for this work. There is not even any Century Oil in the place! I think that the cleaning and the oiling should make things run better. I PROMISE to never adjust anything that I do not thoroughly understand. I found this out the hard way in 1981 when I loosened the sound lens on my old Eiki 16. Cost me $$$ to fix, and is to this day the most expensive repair I ever had to make on my 16mm anything! (Oh yeah, I tightened the lens sooo tight that I cracked it!) I remembered all of this when I rebuilt the two Holmes 8's, and the Holmes Educator. I didn't break/crack anything. They are decent machines, but not Century's! Thanks!
| IP: Logged
|
|
John Eickhof
Jedi Master Film Handler
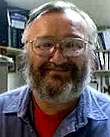
Posts: 588
From: Wendell, ID USA
Registered: Jan 2000
|
posted 06-01-2001 01:24 AM
Bruce, when you reverse the intermittent sprocket remember that it has slack in-and-out so snug the bolt then place a piece of fil in the gate and see how the sprocket holes line up on the intermittent sprocket. If necessary, slide it in or out a little to center the teeth in the sprocket holes, then tighten the bolt. Run a loop of about 10 feet of film, with the intermittent framed down all the way (with max. distance away from bottom of trap) and observe how the film is between the bottom of the trap and the intermittent sprocket, if it is running with bothe edges of the film falt or straight down, you have the sprocket in the correct place, if one side is loose or 'curves' then that side is loose and the sprocket needs to be moved a little towards that side. Have fun!
------------------ John Eickhof President, Chief Slave Northwest Theatre Equipment Co., Inc. P.O.Box 258 Wendell, ID. 83355-0258 208-536-5489 email: jeickhof@nteequip.com
| IP: Logged
|
|
|
All times are Central (GMT -6:00)
|
This topic comprises 2 pages: 1 2
|
Powered by Infopop Corporation
UBB.classicTM
6.3.1.2
The Film-Tech Forums are designed for various members related to the cinema industry to express their opinions, viewpoints and testimonials on various products, services and events based upon speculation, personal knowledge and factual information through use, therefore all views represented here allow no liability upon the publishers of this web site and the owners of said views assume no liability for any ill will resulting from these postings. The posts made here are for educational as well as entertainment purposes and as such anyone viewing this portion of the website must accept these views as statements of the author of that opinion
and agrees to release the authors from any and all liability.
|