|
This topic comprises 3 pages: 1 2 3
|
Author
|
Topic: Polishing the sound drum
|
Harry Robinson
Expert Film Handler
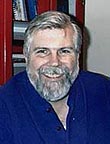
Posts: 155
From: Franklin Tennessee
Registered: Dec 1999
|
posted 07-25-2001 03:11 PM
At the risk of beating a dead horse, I am once again trying to completely eliminate base side scratching in my old RCA 1040. The problem is apparently coming from the sound drum, which I have polished to a level of medium smoothness. I am thinking that the residual marking (which can only be seen by reflecting light off of the film and using a magnifying glass) can be eliminated by polishing to a mirror finish.There seem to be two schools of thought on this, and I'd like to get a cross section of opinion from the experts on what to do. I plan to mount the sound drum shaft in a drill press Thursday evening, then apply 3M Finess-it II finishing material with 3M Imperial microfinishing film until I see a high mirror finish. This technique was recommended by Jim Duncan in Decatur AL. However, I mentioned this to another tech, and he said I would ruin the sound drumm using this method. He suggested taking the shaft to a machine shop, having it indicated, then reground. Which is better? Do I risk ruining the sound drum with the finishing compound? Wolk wants 289 bucks to replace this part. I think we all know that is more than this sound head is worth.
| IP: Logged
|
|
Will Kutler
Phenomenal Film Handler
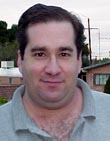
Posts: 1506
From: Tucson, AZ, USA
Registered: Feb 2001
|
posted 07-25-2001 04:23 PM
Hi Harry!First of all, drill presses are not very accurate when it comes to precision work. And if you do insist on using a drill press, then use the best chuck that you can...like a precision Albrecht!! And double check that the drill press is running true and that there are no burrs in the chuck! How do you know that a chuck will not damage the bearing surfaces on the shaft! If you insist on this method, then put the shaft and drum in a lathe with a collet--which should not damage the shaft. Also, when hand polishing, how do you know that you are not going to screw up the coeccentricity of the drum and shaft which will result in a definate unwanted wobble!! Also, Even though it may look like a good polished surface, how can you be sure that you have not created a taper or "wave" on the drum surface! If you do insist on this method, then you will probably need to inspect your work with proper inspection dyes and oils--such as if you were scraping bed ways--which is an art of its own--or a surface plate with v-blocks and dial indicator. If you look at the ends of the shaft, then you can see the center drill counter sinks that were used when the part was origonally turned, heat treated then o.d. ground. If the shaft and drum is put back on an o.d. grinder, then a mag base and dial indicator can be used to get everything perfectly "clocked in" and coencetric--not to mention a perfect finish! My only concern is the possibility of maybe having to regrind the bearing surface also to match the drum. You would then either have to find new bearings with the correct dimensions, and grind to those dimesnsions, or press on sleeve bearings to make up the difference.
| IP: Logged
|
|
|
Will Kutler
Phenomenal Film Handler
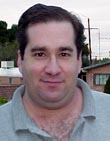
Posts: 1506
From: Tucson, AZ, USA
Registered: Feb 2001
|
posted 07-25-2001 05:07 PM
As far as what Richard Fowler said about chrome plating. He is talking about hard chrome plating such as what is used in engine cylinders, piston rings, etc. This can also be used to build up worn surfaces so that they can be reground/finished. Of course, this process is limited to the type and suitability of the material to be plated. Also, a surface and or o.d. ground surface can be resistant to corrosion--this has to deal with metalurgy.As far as ruining the heat treated surface. This is dependant on the type of material used to make the drum, and the heat treat process. There are heat treating processes used to just treat the surface of the material (case hardening), as well as proceses used to treat the entire thickness of the part. There are also secondary heat treat processes used to do things like tempering. If anyone knows what type of material these shafts were made of, then I can look up the correct heat treat process. My only regret is that I am already finished with my machine tool classes for now. Making a sound drum and shaft would have been a suitable class project! Harry--see if any of your local community colleges have machine tool programs. Enroll--you'll learn something and may be able to make some parts? Also, check out if there are any machinists hobby clubs in your local community--they may be able to help you out!
| IP: Logged
|
|
|
Will Kutler
Phenomenal Film Handler
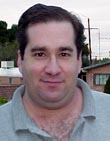
Posts: 1506
From: Tucson, AZ, USA
Registered: Feb 2001
|
posted 07-25-2001 05:34 PM
I CANNOT STAND WD-40!!! Yes, the stuff can INITALLY be a good lubricant, but after it dries IT WILL PROMOTE CORROSION!Here is an example: When I went away for basic training, one of the things that I did was prep my tools for storage. I thourghly cleaned them, coated them with WD-40 and put them back into my roll-a-way. Mind you that my roll-a-way was indoors and not subject to a corrosive atmosphere: ie water etc. Well, when I came home on leave between leaving basic training and going to my first duty assignment I of course checked my tools. ARRRRRRGH!!!!!!!!MAJOR RUST!!!!!!!!!!!!! I had to spend a lot of time cleaning them, and was lucky that some very expensive tools were not ruined!!!!!!!!!!!! Anyhow, after cleaning them up, I had to reprep them for storage. I used Marvel Mystery Oil, and did not have the same problem--in fact, it did an excellent job of protecting my tools, which were stored under the same conditions that they were when I origonally stored them with WD-40. I WILL NOT recommend WD-40 to anyone!!!!!!!!!!!!!!!!!!! Another MAJOR contributing factor leading to rust/corrosion is fingerprints and the oils emitted from your skin!!!!!!!!!!!!!! There have been articles in machinists hobby magazines like Home Shop Machinist about hot blueing metal...
| IP: Logged
|
|
|
|
Will Kutler
Phenomenal Film Handler
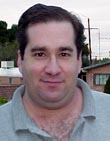
Posts: 1506
From: Tucson, AZ, USA
Registered: Feb 2001
|
posted 07-25-2001 06:51 PM
Thanks for the reply, Gordon!I downloaded the RCA books from Film-Tech. Quote the RCA 1040 book page 6 item(10) second edition Sept 23, 1936 or 8 ('tis hard to tell): "The A.C. Motor is of the split phase starting, induction type and runs at a constant speed of 1765 R.P.M. It is rated at 1/4 h.p. The motor incorporates an automatic starting winding from the motor circuit when normal running speed has been reached." I wonder if the 1765 r.p.m. is a typo? Unfortunately, I could not find a reference to motor r.p.m. in any of the other RCA 1040-9030 or Simplex SH1000 books. Furthermore, much of the info was not stamped onto the motor's data tag at the factory--I wonder why not, since there are blocks in which to stamp this info. Gordon, what about the start resistors having been removed on the 1050 and later soundheads as per the books? According to the RCA 1050 book, downloaded from Film-Tech, the origonal open bearings were replaced with metal shielded bearings. One thing that I have learned is that metal shielded are much-much better than rubber shielded, which tend to be stiff!! But, the metal shielded will not hold lubricants/grease as well as rubber shielded bearings. The only thing that I like about shielded vs open bearings is less chance of notorious oil leaks, which can ruin slit lenses! Gordon, surface grinding and o.d. grinding should be done after heat treatment, otherwise you are defeating your purpose. Thanks for the info about the origonal heat treat process. My guess is that case hardening was picked as a means of shortening the production time!
| IP: Logged
|
|
|
|
|
|
|
|
|
All times are Central (GMT -6:00)
|
This topic comprises 3 pages: 1 2 3
|
Powered by Infopop Corporation
UBB.classicTM
6.3.1.2
The Film-Tech Forums are designed for various members related to the cinema industry to express their opinions, viewpoints and testimonials on various products, services and events based upon speculation, personal knowledge and factual information through use, therefore all views represented here allow no liability upon the publishers of this web site and the owners of said views assume no liability for any ill will resulting from these postings. The posts made here are for educational as well as entertainment purposes and as such anyone viewing this portion of the website must accept these views as statements of the author of that opinion
and agrees to release the authors from any and all liability.
|