|
This topic comprises 3 pages: 1 2 3
|
Author
|
Topic: How are star gears machined?
|
|
|
Will Kutler
Phenomenal Film Handler
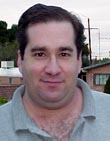
Posts: 1506
From: Tucson, AZ, USA
Registered: Feb 2001
|
posted 09-18-2001 11:24 PM
1st, ther are books that give all kinds of tech data about metals and heat treatment so that a designer/engineer can select the approperiate materials for a given application.the basic shaft od (outside diameter) profile is turned on a lathe between centers. The shaft is then taken to a mill where it can be inserted into a made fixture for mass production--or a rotary table. and the star to cam and star to cam pin profiles are milled with approperiate dia end mills . Rough milled parts are left about .010 oversized to allow for grinding. The part is then heat treated. After heat treatment, the shaft will be ground between centers on an od grinder. Then the star to cam and star to cam pin bearing surfaces are located back into a made fixture or rotary table and ground on a jig grinder. Finished part needs to be precision inspected. Tolorances for these parts is about + or - 0.0002 or so -- a quarter inch is 0.250 --so this shows you just how precise these parts are! Yes, I can make these parts--I just dont have my own shop! Fun projects. About 3 days work to make one star and cam (including heat treatment) So making one is expensive! Shops like LaVezzi have special set-ups and tools for mass production. This explanation is very basic, I have not discussed all of the tools and fixturing needed. These would have made excellent projects for my machine tool classes--we just did not have a jig grinder! As for sprockets, LaVezzi has designed their own special tools and processes for making sprockets--these are their own patented secrets that they will not discuss--they do not give tours of their shop.
| IP: Logged
|
|
|
|
|
John Anastasio
Master Film Handler
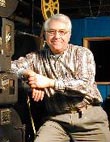
Posts: 325
From: Trenton, NJ, USA
Registered: Sep 2000
|
posted 09-19-2001 09:13 PM
The Sarnoff Research Center is practically in my back yard and I've been in it many times, including the old "General"s office...actually had the chance to peruse his personal picture books one day, courtesy of an old friend. RCA did make some nice equipment, but they also had some spectacular bombs. You're probably too young to remember the CED videodisc that actually used a stylus sitting in a groove. You should have seen the video games they were working on with that dog! Fortunately, they never made it to the public. And yet, their unique "video engine" computer has enable other companies to produce some amazing new technology. They also made a few radios that were amazing for their really crazy circuitry, especially in the 1930's. They did a lot of really nutty things to get around other people's patents. What they couldn't get around, they stole and then ran people into the ground in court....like Edwin Armstrong. Those Brenkerts might have an RCA logo on them, but they weren't designed by RCA. It was an interesting company. Watch a tape called "Empire of the Air" and you'll get a good feel for how Sarnoff made the company in his own somewhat seedy corporate image. They had a very large presence in New Jersey, both here in the Princeton area and also down in Camden.
| IP: Logged
|
|
Paul G. Thompson
The Weenie Man

Posts: 4718
From: Mount Vernon WA USA
Registered: Nov 2000
|
posted 09-19-2001 09:41 PM
John, David Sarnoff was quite the person. He and Frank Sinatra were very good friends, too. I have heard that Frank Sinatra composed a song for Mr. Sarnoff, and sang it at a party that included Mr. Sarnoff. Name of the song (I think) was "That's Why You're A Champ".Josh, have you seen the video tape PBS had about these old radio guys? The title was, "Empire of the Air". I have that, and if you would like to borrow it, I'll send it to you. I think it is out of print, and can't buy it anymore. It includes the history of all these guys from Marconi, Armstrong, Deforest, Sarnoff, and a few others. One weird funky circuit RCA had was known as the "Syncro-Guide" Oscillator. It was used as the horizontal sweep circuit in the old RCA TV sets, and it was nothing more than a mdoified Series Hartley Oscillator. I never ever did figure out how his horizontal drive circuit worked. And, I have heard many TV techs say, "Oh, those ***** syncro-guides - grrrrrrrrrrrrrr" And, I have said the same countless times. Paul
| IP: Logged
|
|
Mark Gulbrandsen
Resident Trollmaster
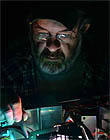
Posts: 16657
From: Music City
Registered: Jun 99
|
posted 09-20-2001 04:53 AM
Will and others, I have been very fortunate to have been on a tour of LaVezzi with Al LaVezzi a number of times. At both the old plant in Elmhurst and the new one in Glendale Heights. He's a very gracious host when time allows him to conduct what is usually at least an hour plus long tour of the plant in Glendale Heights, IL. No 10 minuite tours there! The following is a generalized write up about how stars and cans are made....Sprockets are a whole other thing that involves many. many operations, some that are similar to the description below. The only thing proprietry as far as sprockets go is the VKF and posi-trol teeh thata re ground into various sprockets, other wise sprocket making is a pretty straight foreword process. Its the making of Stars and cams that LaVezzi has many secrets about, however they never hesitated to show me, or any other people I brought with for a tour. Quite frankly, one could not set up easily to produce the parts, they are the only one in the country making them to the precise dimensions thata re requires....so why would they worry about someone steeling any secrets........ Century cams are turned down to a rough dimension in one or two passes from 3" diameter alloy steel bar stock on Swiss made CNC lathes. Huge, deep cuts are done on these automated CNC machining centers that have automated bar stock feeders. I remember Al saying that the CNC lathes have burst into flames a couple of times in the past as the cuts they take are so large and generates so much heat. Century cams were being roughed out on my last tour and smoke was pouring from the machine due to the 1" deep cut that was being taken off! From what I remember he told us, if they had to take too many extra passes to turn the bar stock to the proper diameters it would not be economically feasible for them to even make the parts. The next step is to mill out the slot for the star wheel to turn over in,and any other holes and set screw flats, and oil spirals needed. After the rough cut operations, the roughed out cams are sent out for heat treatment and black oxide coating and then the shaft, and then the raduis for the star ground to proper diameter. Next the hole for the pin is located, this is after heat treating due to slight dimensional changes in the part as a result of the heat treat, and a finished cam pin is pressed into place.Starwheels are another matter as they involve more operations, but are roughed out in a similar way as the cams are. After rough cut the star end is round rather than like a star. Next operation if memory serves me is to rough out the star radiuses first on CNC milling machines and to turn any oil spirals, etc into the shaft end, and then the stars go out for hardening and Black oxide for corrosion prevention. The black oxide also aids in visual checking during machining operations. They come back from heat treatment and are sent through a number of different grinding operations such as shaft diameter, star slot rough grind, etc. of which the final operation is a final grind on the slot. This is done in a soundproof booth(talk about working in a padded cell!) with an air bearing Studer grinder which is manually operated. On my last trip there were two of these rooms set up for this. On my last trip through there Al LaVezzi said that there were only two people that worked there that could do this final grind operation properly. The final slot grind operation is something that has to be heard and cannot be felt as in other grinnding operations and thats why the sound proof room. Even the grinder barely makes any noise of its own when its running. After any part at LaVezzi is manufactured it goes into a temperature controled room for QC and each and every parts critical dimensions are checked to meet specification. Reject ratio is low due to the many long time employees experience in this type of manufacturing. Employee turn over is not something he worrys anout much. They also make parts there for other companies such as Imax, Cinemeccannicca, Strong, and also movement parts for many motion picture camera manufacturers. They do have a web site at http://www.lavezzi.com/ There is an on line slide show of the plant and some of the parts that they produce, however, one has to actually go there and see the operation to appreciate the craftsmanship that goes on there. Also, keep in mind that Motion Picture parts are only a small amount of what is produced there anymore. LaVezzi also makes many other parts such as medical items(many from from Titanium!), aerospace parts and anything else of a precision nature. All in all an amazing place to tour. Mark @ GTS
| IP: Logged
|
|
|
|
Will Kutler
Phenomenal Film Handler
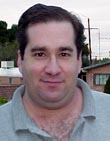
Posts: 1506
From: Tucson, AZ, USA
Registered: Feb 2001
|
posted 09-20-2001 05:00 PM
Hi Mark and all!Just to give you a little background info about myself. I have been a licensed FAA Aircraft Mechanic since 1988 including both civilian and military service. I am currently completing my AAS in Machine Tool Technology CNC Option from Pima Community College (need to finish English 102 to graduate) and am working on a BS in Manufacturing Engineering Technology from AZ State University. Yes, I have job shop machining experience--not to mention my experience as a Projectionist. So I found your post about LaVezzi interesting. I guess Mr. LaVezzi wants to ruin his expensive CNC machines--1" cuts!? And machines bursting into flames? I'm speechless! And needing to hear the gringing operation because feel does not cut it? This is what precision inspection equipment is used for during and after the machining and grinding processes!
| IP: Logged
|
|
Mark Gulbrandsen
Resident Trollmaster
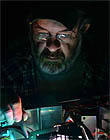
Posts: 16657
From: Music City
Registered: Jun 99
|
posted 09-21-2001 10:17 AM
Will, There are no after machining touch ups at LaVezzi that I was privy to seeing done in the inspection room. The inspection room is a clean, temperature controled room and would not be doing this sort of thing. Any final stuff is done in the shop, which in itself is so clean it could pass a use for food service inspection easily. The final grind on the star wheels slots are indeed done this way and perhaps this is LaVezzi's method of final inspection for this part, but this is out in the shop in an enclosed room for each grinder. Personally, you could never learn what these guys know in any school, anyplace, ever, or even around the normal type of precision CNC machine shop. You have to remember that they have been doing this stuff since the mid 30's, perhaps earlier. You'd have to work there to learn how to make the sort of things that they do. Also keep in mind that they are just about the only place in the country that has this sort of experience, the facility, and knowledge to make these high perecision parts to such tight tolerances, and to keep reject rates as low as they do. I have been to other precision shops to have parts manufactured that claim they can do similar work but the overall quality of the finished product is normally no comparison to what LaVezzi cranks out. When you are shown the parts sample collection that resides in the clean room you are literally blown away. There are parts for Panavision and Arriflex camera movements, Imax camera and projector parts, and the normal lot of high precision projector parts, plus other interesting complicated aerospace parts. These guys are definately in a class all by them selves. When the star slots are getting their final grind sometimes it can be heard and sometimes not, although the final few hundred thousandths or so that is removed definately comes off. The old fashioned way to do this is to lap the slots out to final size. Final inspection of critical dimensions are then performed in the clean room. Anything bad is rejected there and destroyed, although that is rare. As far as these guys taking such heavy cuts are concerned I'm quite sure that they know what they are doing with the lathes that perform this task. I can't remember the depth of cut exactly but it is very large. My last visit there was about 6 years ago and I'm sure those lathes are still humming along quite well today. These lathes also do alot of Titanium machining rough out for medical instruments so one could assume that they're made for this sort of work day in and day out. As I'm sure you kow, it all has to do with spindle speed and cutting tool feed plus proper lubrication of the cutting tool to clear away debris and keep the cutter cool. Any high quality lathe of sufficient size can do this if properly set up, day in and day out. Will, Probably after you have about another 20 years experience in making ONLY presision parts you can then start to think about making parts like those that come out of LaVezzi. If you have the facility to do it in. Keep studying! Mark @ GTS
| IP: Logged
|
|
Will Kutler
Phenomenal Film Handler
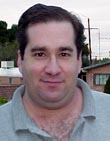
Posts: 1506
From: Tucson, AZ, USA
Registered: Feb 2001
|
posted 09-21-2001 06:16 PM
Hey Mark!If you are offering me a challenge about making these parts, then give me a copy of the prints! I'll take you up on it! There may be a few operations that I may not be able to do because I dont have the tools. I can present the challenge to my instructors and maybe I can use the shop! Most of my classmates are/where people with a lot of experience behind them! They went back to school to get a little piece of paper so that they can get promoted at work! About some of my instructors: They are just not "schoolroom" instructors--all work in industry and teach as a side. If I spent the time here to tell you all their credentials, it would blow you away! Keep in mind that Tucson is very high in the aerospace industry. Several of my instructors were in charge of the tool room at Hughes Aircraft. One of these people was also a tool maker at Los Alamos! Several of these guys are injection mold makers. Several are also precision instrument makers at the University of AZ involved with NASA related projects! We have one injection mold shop in town that is known for taking on the difficult jobs in the country that no one else will touch! As for me, ya, I am used to working with tolorances of 0.0000! And ya, I am good! Another piece of info for you--if one decides to become a machinist, one will never stop learning! The worst machinists are those with egos who are know it alls!
| IP: Logged
|
|
|
|
All times are Central (GMT -6:00)
|
This topic comprises 3 pages: 1 2 3
|
Powered by Infopop Corporation
UBB.classicTM
6.3.1.2
The Film-Tech Forums are designed for various members related to the cinema industry to express their opinions, viewpoints and testimonials on various products, services and events based upon speculation, personal knowledge and factual information through use, therefore all views represented here allow no liability upon the publishers of this web site and the owners of said views assume no liability for any ill will resulting from these postings. The posts made here are for educational as well as entertainment purposes and as such anyone viewing this portion of the website must accept these views as statements of the author of that opinion
and agrees to release the authors from any and all liability.
|