|
|
Author
|
Topic: Goldberg customer service...wait, WHAT CUSTOMER SERVICE???
|
Brad Miller
Administrator
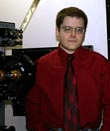
Posts: 17775
From: Plano, TX (36.2 miles NW of Rockwall)
Registered: May 99
|
posted 10-23-2001 11:24 PM
Allright everyone, the boys at Goldberg have been virtually begging me to post this based upon their complete lack of interest in backing their products, so I am posting this in all of it's glory as a warning to anyone considering purchasing a Goldberg product.We all already know what a joke Goldberg projection ports are. Joe has a review of this in the "reviews" section of this website and I couldn't agree more. However, up until now I've always considered their reels the benchmark for which all others are compared to. Well, not anymore. I think I would rather have a Technicolor depot reel with cardboard masking taped onto the flanges to extend them to 24 inches. At least that reel might work. 7 weeks ago I posted a thread titled "Goldberg large split reels". It explained the basic problem I was having with two Godlberg 24 inch split reels I had purchased. Here is the outcome. I contacted Ben Kehe of Motion Picture Projection Services, Inc. whom I had originally purchased the reels through. For those who do not know Ben, he is one of the most wonderful people in this industry to work with. I've yet to find another dealer that cares as much as Ben does and is as particular and efficient. I could go on and on praising Ben, but this Goldberg treatment needs to be heard around the world. Ben had purchased the reels through Wolk and Tony Klingman was very helpful in setting up the return authorization with Goldberg. I shipped the reels back, for they were nothing more than scrap metal to me the way they were. Goldberg received the reels and noted that the packaging was solid and in-tact with no damage. Now here comes the pathetic part...Goldberg would do NOTHING to remedy the problem. NOTHING!!! What kind of company will not stand behind their product? The reels are useless and anyone can easily see that they are defective. Take a look below. Please note that taking pictures of this was VERY difficult, as this really needs to be seen in person to really see just how warped these flanges are. This is reel #1. Notice how the back side of the reel is horribly bent? This is reel #2. This one is even worse. Going back to reel #1, notice how warped the flanges of the reels are. Just sitting a core in the open area of a flange shows the spacing problem. Reel #2 shot from above, showing the warpage, particularly at the core. And here's a shot of reel #1 (the better one of the two) with a core on the shaft. Note that this picture was taken with the flanges screwed together as tight as possible, and yet look at all of the clearance from the edge of the core to the inside of the flange at the shaft! This sort of defect did not happen in shipping, for the front flange of the reels are flat. There is nothing to make me believe that the boxes (which arrived undamaged in their original packaging, with the "cardboard film" strips in between the flanges) suffered any shipping mishandling whatsoever. These reels plain and simple left the Goldberg factory this way and even upon receiving them back from a dissatisfied customer, they have outright refused to do anything to make good on them. Basically what is happening is when the reels are screwed together, they are stopping on the core itself and NOT on the reel's shaft and O-ring. A split reel should close completely and still be able to shift the core back and forth ever so slightly for it to be useful. These reels will severely damage the sprockets on the first part of any film that is ran onto them...and again I stress that Goldberg is NOT willing to make good on this. They are a sheet metal company with more than enough equipment to have even banged these inner flanges flat...but no, they got their money and to hell with their customer. It seems the only thing that Goldberg can make with any degree of quality is their platter reel (also reviewed here on this site). There is no need for this kind of "customer service" in the industry. So, what other company makes 24 inch split reels with a 5/16 inch shaft? (Bob, how about Neumade?) I am taking my business elsewhere and I urge everyone else to as well, for Goldberg does not care about you, the customer.
| IP: Logged
|
|
Mike Heenan
Phenomenal Film Handler
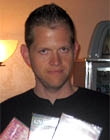
Posts: 1896
From: Scottsdale, AZ, USA
Registered: Mar 2000
|
posted 10-23-2001 11:44 PM
I second Brad's statement. While I have not dealt with the customer service, I must say the reels are pretty crappy. Im on my second 6000' split reel (which is actually a 26", so thats 8,000'). My problems with these reels seem to be with the flange (the gold part where the shaft goes through). I never excessively tighten the reels, but after use, I noticed the screws holding the flange in are torn off. This creates a problem where when you tighten the reel, the flange digs into the reel and creates a twisted mess. I wish they were better enforced in this part, since Im on my second one, which is also missing the screws, but luckily the flange is still on there.
| IP: Logged
|
|
Steve Guttag
We forgot the crackers Gromit!!!
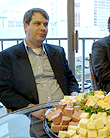
Posts: 12814
From: Annapolis, MD
Registered: Dec 1999
|
posted 10-23-2001 11:55 PM
I can honestly say that as a Goldberg dealer with selling many 16, 35 and 70mm split reels...I have never had the kind of problem you are describing. Again, we sell a lot of reels and split reels and none of the split reels have had problems. I don't recall selling any 6000' split reels except maybe a 70mm one to an IMAX house.I can honestly state that we have not had problems with the Goldberg ports either, still use them, and not a single dissatisfied customer. I can't speak to your experience but it does seem like a lot of "dealers" were involved on old stock items. Steve ------------------ "Old projectionists never die, they just changeover!"
| IP: Logged
|
|
Brad Miller
Administrator
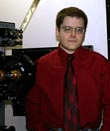
Posts: 17775
From: Plano, TX (36.2 miles NW of Rockwall)
Registered: May 99
|
posted 10-23-2001 11:59 PM
Steve, I urge you to take a trip down to the Dallas area and take a look-see for yourself on these joke ports and these two reels. The projector can be heard during a quiet scene from the front row! As to the reels, I am not aware of a "best if used by XXX date" like milk. The bottom line is these reels were NEW. It doesn't matter how long they sat in someone's stock room. Reels do not go bad from sitting on a shelf in their original packaging.Would you feel the same way if this reel issue had happened through Cardinal? Somehow I don't think you would be backing them if they had told you to take a hike.
| IP: Logged
|
|
John Eickhof
Jedi Master Film Handler
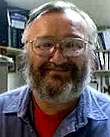
Posts: 588
From: Wendell, ID USA
Registered: Jan 2000
|
posted 10-24-2001 12:13 AM
Hi Brad & Mike, I generally try to avoid this kind of thing, but I need to add acouple of details, first, the use of 'split reels' or 'flanges' is generally regarded to be used in editing and preparation of fil for use on conventional reels. They are not designed to be used on a projector with the exception of 1000 & 2000 foot models used on dual fim projectors and editing / printing machines. They are not designed to be manhandled like conventional reels. By virtue of design, the split reel is not designed to be used at high speeds of rotation, no matter if it's a GB, Neumade, or JR Film, the same troubles will exist! Thus I think some of the fit & wear problems addressed are fault of mis-application of the reel as for use. However, I also do not think that Goldberg should even offer a "split reel' or flange with a capacity over 2000 feet as the shear weight and inertia of use would most likely tear them apart! (as in Mike's case) Brad, did you actually place film with a core on the split reel? I noticed that you used a white core in your pictures, I have found some of these to actually measure around 28-37 mm wide! The quality control of the cores is poor too! The old yellow ones seemed to be the best! The damage to the center that you show is absolutely in-excusable if they came out of the box that way! (They appear to be used ones?) My suggestion as a dealer for Goldberg (for over 20 years now) is to directly contact Randy Urlick, at GB in Denver, (303-321-1099) kindly explain the trouble and see if you can work things out, I have known Ben for many years too, and please don't think this is to circumvent his efforts, but I think anytime there is a dispute, the best information comes straight from the 'horses mouth' not through middle men! Personally, my business relationship with GB and Randy spans many years and he has always been very quick and straightforward to correct any problems. In closing, I wish you and Mike luck, and I would still recommend no split reel larger than 13" diameter!!! John
| IP: Logged
|
|
Brad Miller
Administrator
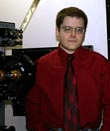
Posts: 17775
From: Plano, TX (36.2 miles NW of Rockwall)
Registered: May 99
|
posted 10-24-2001 12:24 AM
John,I've got a 24 inch split reel that a friend of mine literally "made" in his garage with only a hammer and a pair of pliers. Basically he butchered a 1000' Goldberg reel and he butchered a 6000' Goldberg solid hub reel and concocted the thing. It is very wobbly and I was first very concerned about using it, but the darned thing works and it works very well. I have wound 6000+ feet of film onto cores before and never had a problem. I can also tell you that there are a LOT of other people who do the same for various reasons, of which is not the issue here. To answer your other question, yes I did more than just place a core with film on it. I placed an empty core onto the reel, stuck it on the takeup arm and trashed some film in the process! (Yes, it was junk/test film because I was concerned about there not being enough clearance.) I too have seen the slight differences in cores, but again this is not the issue. I should be able to use a core that is 30mm wide and the flanges should still not screw together so much that the film can not have just a mm or two of side room. As to contacting Goldberg directly, Randy was the person whom I sent the reel to and he was the one who faxed back the refusal to make good on the product. ...and yes, the reels came straight out of the Goldberg box this way and yes, the reels were brand new. Bear in mind that they were used by me for a day, then returned to Goldberg, then sent to Wolk to see if they could do anything with them, then returned to me. Other than the fingerprints and some added scratches from going back to Goldberg, the reels are sitting here now in the same physical condition that I shipped them out originally.
| IP: Logged
|
|
John Eickhof
Jedi Master Film Handler
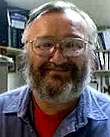
Posts: 588
From: Wendell, ID USA
Registered: Jan 2000
|
posted 10-24-2001 12:36 AM
Brad, I'm sorry to hear that Randy responded that way, I believe his motives might be based on the fact that these were as you said 'in a Dealer's hands fo a few years' and the fact that Ben did not directly purchase them from GB, that in fact he bought them through a middleman. (Wolk) So I would think the final resolution is in the hands of the person you paid, and he in turn should be the one that carries matters further. Thus, Ben should get a refund from Wolk, then Wolk can go after GB! In this order, Wolk has much more clout than you or Ben, they will get results for their own edification! As for fit, It would be very simple to assemble the split reel then measure the distance between flanges with a dial caliper and see exactly the inside dimension, also, it was only about 15 years ago that manufaturers placed the O rings in split reels, before this, they were subject to binding of the brass halves and reels became almost impossible to unscrew! You have to consider the amount of leeway that an O ring can allow as for machining! A lot less tolorance than before! Anyway, I still advocate split reels of less than 13" and like Gordon can say out of several hundred of them, (Neumade, GB & JR) I have never seen this problem! Good luck! (You may want to have your friend fabricate a few more of the home made ones! He might get a decent business started!)------------------ John Eickhof President, Chief Slave Northwest Theatre Equipment Co., Inc. P.O.Box 258 Wendell, ID. 83355-0258 208-536-5489 email: jeickhof@nteequip.com
| IP: Logged
|
|
|
|
|
Jerry Chase
Phenomenal Film Handler
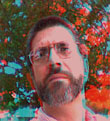
Posts: 1068
From: Margate, FL, USA
Registered: Nov 2000
|
posted 10-24-2001 10:34 AM
Brad, you need to distinguish between your feelings about the product and the financial responsibility involved.From what I understand, Ben sold you the product. Unless he sold you the product "as is," he is responsible for selling the product to you in poor condition, end of story. If it WAS sold "as is," it is your problem. Any refund will have to come from Ben, and he will have to deal up the chain. That is part of doing business. You shouldn't be dealing direct with Goldberg in this situation. I am puzzled about the flange damage to the product. I can't understand how such damage would occur during the manufacturing process. If it didn't occur there, and there is a end of production line inspection, I can understand the reluctance by Randy at Goldberg to "make good" on the product. Stuff does "go bad" on the shelf. A pallet can drop on a stack of boxes and items be "fixed" and then reboxed. Sometimes the owner of the business might not even be aware of the accident and subsequent "repair." The clearance from the edge of the core to the inside of the flange would appear to be OK if the flange was straight, which indicates to me the original manufacturing may have been fine. I understand you are frustrated with a product that wasn't delivered in working order. I understand it isn't technically your responsibility to fix it. Even given that, if I had received a reel like the one shown I would have either returned it to the supplier for a replacement, or used a few blocks of wood and a small sledge hammer to pound out the worst of the problem and gone on with life. I'm sure I must be missing something though, since you are so upset.
| IP: Logged
|
|
|
|
|
Pete Lawrence
Expert Film Handler
Posts: 192
From: Middleburg, PA
Registered: Aug 1999
|
posted 10-24-2001 08:52 PM
If I have this right the trail is manufacturer, dealer, dealer, end user. I can see Goldberg grousing about making good on something that was really out of their hands. Did Goldberg send them out that way originally? You will never know. Returning them to whom you purchased them from was the right way to go. Having said that, this is no way for Goldberg to treat a customer if they want to stay in business. Word gets around. Their reputation is now at least one notch lower in my opinion, and it was low to start with. Customer service after a sale is as much of doing business today as is selling a product in the first place. Richard suggests E.E.P. splits and I agree. I have some of their 2000' split reels and like them better than the Goldbergs. Do they make 24" versions? This doesn't really apply to the discussion but I offer it as an example. I work, doing both circuit and software design, for a company that makes RF test equipment. If a customer decides to return a unit he can, for ANY reason. I should add, these are custom made-to-order in the range of $20K to $150K pieces of equipment. NO questions asked! That's the company policy. If only other well known companies had similar policies. And yes, I do look like that before my first cup of coffee in the morning!
| IP: Logged
|
|
|
All times are Central (GMT -6:00)
|
|
Powered by Infopop Corporation
UBB.classicTM
6.3.1.2
The Film-Tech Forums are designed for various members related to the cinema industry to express their opinions, viewpoints and testimonials on various products, services and events based upon speculation, personal knowledge and factual information through use, therefore all views represented here allow no liability upon the publishers of this web site and the owners of said views assume no liability for any ill will resulting from these postings. The posts made here are for educational as well as entertainment purposes and as such anyone viewing this portion of the website must accept these views as statements of the author of that opinion
and agrees to release the authors from any and all liability.
|