|
This topic comprises 3 pages: 1 2 3
|
Author
|
Topic: Film cement joins
|
|
|
|
|
|
|
|
Leo Enticknap
Film God
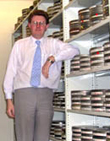
Posts: 7474
From: Loma Linda, CA
Registered: Jul 2000
|
posted 03-13-2002 02:38 AM
I'd like to jump on the 'Stan is correct' bandwagon, and furthermore add that on acetate, properly made cement joins are better than tape joins in every possible way. Nothing is visible on the screen, digital sound is not affected (only two Dolby data blocks are affected, and I believe the system can survive four corrupted ones without dropping to analogue) and the join will last longer than any splicing tape before drying out. Furthermore, when it has dried out, if you remake the join with care, gently removing the dried cement and cleaning the area of film from which the emulsion has been scraped off, the join can be remade without any loss of frames. OK some sorts of tape are better than others when it comes to leaving deposits, but they all will if they're left on the film long enough.
| IP: Logged
|
|
|
|
|
|
|
Gerard S. Cohen
Jedi Master Film Handler
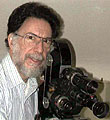
Posts: 975
From: Forest Hills, NY, USA
Registered: Sep 2001
|
posted 03-13-2002 09:29 PM
The Neumade/Griswold wet splicers were sold for negative or positive splicing, the difference being in the width of the anvil bar which determined the amount of overlap. The wider bar and overlap was used in projection booths and the narrow one for negative cutting. When the bar became worn, two setscrews could be loosened, and the bar inverted, bringing a new, square and sharp-edged surface into play. A small cast iron holder contained a scraper, the surfaces of which could also be rotated when worn, and a stiff wire brush. This handy tool was easily lost unless attached to the splicer with a beaded chain or length of monofilament fishing line. Usually this tool was replaced by single edged razor blades, conveniently tucked under the manufacturer's brass label on the front of the splicer. I have a 35mm model containing two "D" cell batteries that illuminated a 3V bulb under a convex lens, providing light for examining film and splice in dimly lit projection booths. Splicing cement [solvent] contained film stock disolved in acetone*, available in thin or thick consistencies according to the user's preference. Neumade made a black, round cast iron bottle holder, with a wood, aluminum and brass pen-like applicator. A fancy gift set on a white ceramic base was available that held bottles of water, cement and blooping ink, with a grooved tray to hold scrapers and applicators. (Photo in the 1934 Neumade catalog.) Neumade/Griswold splicers were originally made in New York City and upstate, and are very common today, sold as nostalgic collectables for about $8 to $10. I've heard of them being made into lamps and bookends. The 16mm model is still used by students and film collectors, and is similar to the 35mm model, but half its size and weight.* See John Pytlak's link to Kodak Professional Film Cement (above) for a complete list of ingredients, formulae and caveats.
| IP: Logged
|
|
|
|
All times are Central (GMT -6:00)
|
This topic comprises 3 pages: 1 2 3
|
Powered by Infopop Corporation
UBB.classicTM
6.3.1.2
The Film-Tech Forums are designed for various members related to the cinema industry to express their opinions, viewpoints and testimonials on various products, services and events based upon speculation, personal knowledge and factual information through use, therefore all views represented here allow no liability upon the publishers of this web site and the owners of said views assume no liability for any ill will resulting from these postings. The posts made here are for educational as well as entertainment purposes and as such anyone viewing this portion of the website must accept these views as statements of the author of that opinion
and agrees to release the authors from any and all liability.
|