|
|
Author
|
Topic: The making of starwheel, cam and pin
|
|
|
|
|
Mark Gulbrandsen
Resident Trollmaster
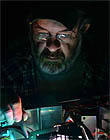
Posts: 16657
From: Music City
Registered: Jun 99
|
posted 12-07-2003 07:32 PM
"I've visited some projector factories, and seen that the "concave cam guide surfaces" of the starwheel are evened manually with a razor-sharp hand tool during checking and assembling of intermittent mechanism." _________________________________________________________________
There is an answer to why it is done this way..... Although it is the "old fashioned way" to fit things, hand scraping of the parts for proper fit is by far the best way to assemble a precision mechanism, and it is in itself considered an art. For instance, all "high end" machine tools have hand scraped ways. This is done for two reasons. 1. To provide the finest possible flat surface that can be produced...(even better than by surface grinder!). and 2., To provide scratches in the machined ways to hold oil for better lubrication. Hand scraped ways always outlast ground ways by a factor of about 10 assuming the machines are equally maintained. Two prime examples of this would be the ways on a Bridgeport Milling machine and the ways on a Hardinge HLV lathe. One has to see the ways on either of these machines to appreciate what it is all about. There was one projector that had a hand scraped main casting and that was the Kalee 21. Really a beautifully made machine with fit and finish that no American manufacturer has come close to yet.
As for the cam radius being hand scraped that you saw, you would find that the parts were not case hardened but you would have a much better fit of the parts in that movement and with the scratches left behind from hand scraping in the surface of the metal some lubricant would be retained and the movement may actually last longer. Nothing wrong with doing things that way at all as long as the person performing the scraping has learned the art. By the way the Brenkert movemetns were not hardened steel but soft, they last longer than the equivelent hardened and ground parts by at least a factor of 10. I'd bet the Turkish movenents are also then run in and lapped with a bit of lapping compound in the oil, guaranteeing a perfect movement.
While John may feel the art of making parts is getting better with technoology, I would flatly disagree. In this sort of case we are relying too much on the technology and too little on peoples actual ability to manufacture tight tolerance parts. Unfortunately the world is quickly loosing all the true artesians that could make super high quality stars, cams, and sprockets to retirement and or death. This is one of the reasons that Kinoton has shifted over to also making electronic intermittent machines. CNC doesnt guarantee you anything in the tolerance department with respect to these parts. Typical tolerance held to at LaVezzi is one ten thousandth of an inch on star wheels and cams. The final grind on the slot in a star wheel is actually done manually in a sound proof booth on special fixtures and the grinder operator has to be able to hear the wheel pass through the slot... Sometimes he can barely hear it at all aas the amount taken off is typically half a ten thousandth of an inch or less! The grinders used by LaVezzi for this are Studer air bearing grinders.
Mark @ CLACO
| IP: Logged
|
|
|
|
|
|
All times are Central (GMT -6:00)
|
|
Powered by Infopop Corporation
UBB.classicTM
6.3.1.2
The Film-Tech Forums are designed for various members related to the cinema industry to express their opinions, viewpoints and testimonials on various products, services and events based upon speculation, personal knowledge and factual information through use, therefore all views represented here allow no liability upon the publishers of this web site and the owners of said views assume no liability for any ill will resulting from these postings. The posts made here are for educational as well as entertainment purposes and as such anyone viewing this portion of the website must accept these views as statements of the author of that opinion
and agrees to release the authors from any and all liability.
|