|
|
Author
|
Topic: change platter from micro switch to phase control?
|
|
|
Monte L Fullmer
Film God
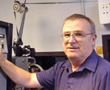
Posts: 8367
From: Nampa, Idaho, USA
Registered: Nov 2004
|
posted 04-04-2005 02:25 AM
There's arguments both ways: One can say that phase controlled brains are the way to go, and one can say that microswith brains are the way to go. I've seen both.
Main reason of users using microswitch is that with the vacuum motors that these platters uses are very sensitive to variations in voltage in the AC line. One volt difference in the 120VAC line, either way, can cause the platters to go faster, or go slower.
Phase controlled brains, in as much as they pay out film in a continous fashion, will be sensitive to this voltage variations in where the one volt drop will cause film windage to wrap around the roller ring a good two times while the film is being paid out, due to the slight slower rotation of the platter. One volt more will cause the platter to "stop and go" due to the faster rotation of the platter.
Microswitch brains are not sensitive to this. It's a simple "On and Off" situation-no matter what the voltage variations are.
If you're using microswitch and happy with it, stay with microswitch. Yet, if not and you want to try phase control, plan on spending $170.00 per module from Strong.
Installation of Phase control modules is quite easy. Two things that must be done for the conversion: take out the microswich hardware, and move the inner guidance roller to the outer hole on the control plate. The wires from the control plate plug must be attached a certain way (in phase) with the module. Wires crossed and the module will not work. When installing the module, one screw is a regular pan head and the other is a phillips taper head. This allows alignment of the module to the arm. the payout arm where the film feeds through must be at least a half inch from the stop roller for the module to activate. Any later, and wraps will be prominent. Earlier and one can have payout problems.
I've seen both in operation. One "indie" house that I service had phase controls and they work like a charm-no wrapping, no early payout problems. Film feed dead center to the brain. Microswitches can be problem free as well, if they are aligned correctly as well as above, but in time, the switches do wear out and short across where brain wraps are common, (which is a good time to install the Strong Wrap Detectors that is available for the A-3/AP-3 and the AP-5 units) then it's time for a microswitch changeout.
I get my microswitches not from Strong, but from Grainger (the 6X-284 switches) which are 10 bucks cheaper than the ones from Strong.
Hope this help you out. Good luck-Monte
| IP: Logged
|
|
|
Monte L Fullmer
Film God
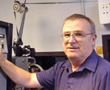
Posts: 8367
From: Nampa, Idaho, USA
Registered: Nov 2004
|
posted 04-04-2005 05:13 AM
quote: Tracy Bellar I was hoping the phase would be steadier feeding out film and not speed up and slow down so much like the warped platters.
Now, you have a BIG, BIG problem there! ... Warped Platters!
Unfortunately, neither microswitch, nor phase control will solve this problem.
What's happening is that when the control arm opens up, the motor takes off on full speed, bringing up the "W" film accumulator to the top which brings the motor to a FULL STOP. Then when the platter has stopped, yet the film is still being delivered to the "W" film accumulator, the "W" film accumulator will begin to drop causing the motor takes off again at full speed, causing this oscillation of stopping and starting and eventually print damage due to the sinching of the film across the "W" film accumulator, and pulled lower guidance rollers from the projector.
One theatre that I know of was playing "LOTR-III" and as big as that print on the deck was, the deck was slightly warped, cause tremendous oscillation, and pulled lower guidance rollers on the projector. When the film was finished, I did my best to flatten out the warpage on that platter by taking the platter off, turn it upside down, and literally pressed on the warped part to flatten it out some.
Best thing is to do is either: straighten out the decks as flat as possible, or replace the decks.
What causes decks to be warped is a most common, and a very sinful and taboo practice, and that is: placing the splicer on the deck and splicing on the decks due to a bad splice or break. (if Brad Miller EVER sees you splice on a platter deck, he'll cut your hands off..lol)
One "HAMMERS" down on the splicer handle thus pushing down on the deck, causing the deck, which isn't the sturdiest made due to the "spider" assemblies below the deck and thin aluminum, to bend down at the end. And this area is where the drive tires of the platter motor are located at below. The motors, then to move up and down due to the warpage and lose grip on the underneath surface of the deck causing this variation of platter speed and eventual oscillation due to the oscillation control of the "W" film accumulator.
Please heed these words of advice of repairing your decks first before doing anything with the brains.
-thx and good luck-Monte
| IP: Logged
|
|
|
|
|
|
|
|
|
|
|
|
All times are Central (GMT -6:00)
|
|
Powered by Infopop Corporation
UBB.classicTM
6.3.1.2
The Film-Tech Forums are designed for various members related to the cinema industry to express their opinions, viewpoints and testimonials on various products, services and events based upon speculation, personal knowledge and factual information through use, therefore all views represented here allow no liability upon the publishers of this web site and the owners of said views assume no liability for any ill will resulting from these postings. The posts made here are for educational as well as entertainment purposes and as such anyone viewing this portion of the website must accept these views as statements of the author of that opinion
and agrees to release the authors from any and all liability.
|