|
This topic comprises 7 pages: 1 2 3 4 5 6 7
|
Author
|
Topic: Proper/Improper use of FilmGuard
|
|
Brad Miller
Administrator
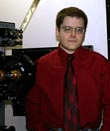
Posts: 17775
From: Plano, TX (36.2 miles NW of Rockwall)
Registered: May 99
|
posted 05-28-2006 04:19 PM
Some people are confusing "saturate" with the word "submerge". The author of that note above is correct that there is no reason to literally DUNK the media pads into a container of FilmGuard. The pictures in the instruction sheets show pressing the tip of the sprayer nozzle up against the pads, which is the proper way to apply the product. The pads do need to be "saturated" (not submerged) so that the application is even however. Otherwise there will be lubricated and non-lubricated sections of the print. (This means part of the print will still suffer from static issues as well as will not benefit from the scratch protection, cleaning and image improvement benefits that FilmGuard offers.) However if the product is literally dripping off of the cleaning machine, then there is definitely too much being applied. (Most certainly due to "dunking" the pads immediately prior to running the show.)
As far as the streaking issue goes, that's just a fact of life for the first application run. Placing the film cleaner on the platter, rather than the top of the projector (which is how I am assuming this example was being handled) does help reduce the streaks. However for some reason there are lots of techs who don't like that idea for reasons of which have never been told to me (and that I can't even come up with on my own).
I am assuming the theater example mentioned above was applying FilmGuard to a public show on a new print, rather than pre-screening the film the night before and applying the product then. Putting aside the obvious issue of there potentially being a lab problem with one of the reels that would never get noticed without a pre-screening (but would be presented to the paying customers), there is a trick to drastically reducing the "liquid lines" on that first application performance for theaters that do not prescreen their films the night before for whatever reason. That trick is simply to load up the cleaner the day before and "saturate" (not submerge or dunk) the media, then let it sit until the next day. This will result in streaks that are not as visible on screen, yet the media will still provide an even application. I plan on putting this into the next batch of instruction sheets.
On picture jumping, there are two projectors out there that can be overly sensitive to FilmGuard. The #1 offender is some Christie projectors, and is what the instructions were based off of...however it does not affect ALL Christie projectors. For example, I used to work at the UA Galaxy in Dallas, and their gates were extremely sensitive to the product, such that the modification needed to be done. However go across town to the UA MacArthur and nothing needed to be done. These two theaters were only built a few years apart as well.
The second troublesome model is some later model Simplex projectors. I witnessed this problem first hand close to the opening of the AMC Mesquite 30, yet go to another AMC in town built a couple of years before or after and the problem is nonexistant. I have yet to find another projector that has had any issue with FilmGuard. The reason the tip went into the instructions was because the Christie projector apparently has more people with the issue than those who don't. (The Christie gate tension spring will also tend to break or remain permanently bent if left at 4 or 5 for any length of time, especially with large xenons behind it.) As such, the modification works magnificently on those troublesome models and is a permanent fix. It has been a number of years now, so it is quite possible that Christie has taken care of the pinhole placement problem of their bands by now too. (If your Christie projector cannot run a "dry" print at a setting of 1 steadily, then your machines definitely have that problem.)
Remember a little bit goes a very long way. Only one quart of FilmGuard if used per the instructions will clean an 8 plex for one month. Hope that helps.
| IP: Logged
|
|
|
|
|
|
|
|
|
|
Brad Miller
Administrator
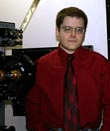
Posts: 17775
From: Plano, TX (36.2 miles NW of Rockwall)
Registered: May 99
|
posted 05-28-2006 11:45 PM
Monte, that's yet another trick that I do believe is mentioned in the instructions...
If using Film-Tech brand media, the rolls are plenty long to cut into halves for long movies (Harry Potter types) and thirds for shorter movies (100 minute comedy types). Not only does this give the theater more rolls per box, but it uses less FilmGuard because you are only loading up as much media as you need to get through the show. Any excess media on the rolls simply soaks up the FilmGuard and gets wasted (media AND FilmGuard, that is). Kelmar also puts a good amount of media on their rolls, but you don't get the coupling cores, nor are they recyclable for more media stock.
Sure it takes a little bit of effort from a booth guy to cut and roll them up, but seriously, surely these guys can devote a few minutes once a week to the task.
(Chris - I thought AMC got that weirdness fixed with that particular set of Simplexes at Mesquite??? The other AMCs in town, as well as other Simplex houses don't have that problem.)
| IP: Logged
|
|
Monte L Fullmer
Film God
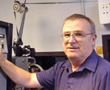
Posts: 8367
From: Nampa, Idaho, USA
Registered: Nov 2004
|
posted 05-29-2006 12:52 AM
Brad, I do agree with you totally since I did read the instructions..AFTER I was told about this Film-Tech site, in 2002.
Yet, Film-Guard was introduced to me the year before, in early 2001 by my good tekkie friend, Mark Gulbrandsen. He told me all about the substance on how well it preserves the film and makes the filmpath run so much smoother. I ordered a bottle from GTS (where he was working with at the time) and tried the substance out with his instruction of soaking the media rolls to the core so that the substance can last throughout a few passes.
It was shortly after the introduction, that I figured out on my own that I could do the limitation of saturation on the media..and cut down the media to fit the feature length to save on the media itself.
When, I was introduced to the Film-Tech site in the summer of 2002 by Mark, is when I noticed the compound being advertised and being sold with the instuctions as you mentioned. This is where I noticed in the instructions of the same tricks of saving the rolls that I was already using and been practicing the year before..
..just a fascinating coinsidence that occured.
thx-Monte
| IP: Logged
|
|
|
|
|
|
All times are Central (GMT -6:00)
|
This topic comprises 7 pages: 1 2 3 4 5 6 7
|
Powered by Infopop Corporation
UBB.classicTM
6.3.1.2
The Film-Tech Forums are designed for various members related to the cinema industry to express their opinions, viewpoints and testimonials on various products, services and events based upon speculation, personal knowledge and factual information through use, therefore all views represented here allow no liability upon the publishers of this web site and the owners of said views assume no liability for any ill will resulting from these postings. The posts made here are for educational as well as entertainment purposes and as such anyone viewing this portion of the website must accept these views as statements of the author of that opinion
and agrees to release the authors from any and all liability.
|