|
This topic comprises 6 pages: 1 2 3 4 5 6
|
Author
|
Topic: How do you thread --- and why?
|
Joe Redifer
You need a beating today
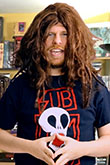
Posts: 12859
From: Denver, Colorado
Registered: May 99
|
posted 11-07-2008 08:03 PM
There are lots of different methods that people use to accomplish the seemingly simple task of threading a projector. One guy I was trying to retrain a few months ago said something to the effect of "Everyone has their own way of doing it". He is no longer allowed to touch the projectors because with an attitude like that I felt that he didn't care about a proper method, just as long as the movies played on the screen.
All of my platters are on the non-operator side of the projector. I thread so that the soundtrack faces the platter tree and away from the wall going to the roller on the tippy-top of the projector, bypassing it and back down to the bottom roller of the platter. The emulsion side hits the rollers as often as possible without any crazy twists. I have Strong platters and I do not tuck the leader into the so-called "notch" on the ring. I let tension do my bidding which makes the ring less than effortless to remove (no need to collapse) by lifting straight up as everyone should.
After this I open all of the projector parts if need be and rewind the film cleaning media since my cleaner is mounted on top of the projector. I spin the flywheel so that the the intermittent has JUST STOPPED its spin. Most people think that just as long as it isn't in motion, it is OK to thread. Not true if you value proper loop size. I thread from the bottom up, keeping the leader off of the floor and making sure the framelines of the leader are in specific places on each sprocket. This guarantees consistency in my loops.
That's about it in a nutshell. Sometimes when I am training others, I notice they occasionally go back and adjust their loops after the fact. I say that if you put the frameline where it needs to go as you thread up, you shouldn't need to do this... ever.
It should be noted that I was trained to thread soundtrack facing the platter tree and away from the wall and threading the projector top down, while the leader between the projector and the platter rests on the floor. I learned of a better way and made the effort to change.
So, how do you thread, and why do you do it the way you do?
| IP: Logged
|
|
|
|
|
|
|
Jon Miller
Jedi Master Film Handler
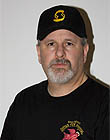
Posts: 973
From: San Diego, CA, USA
Registered: Sep 1999
|
posted 11-08-2008 08:23 AM
At the theatre where I help run film festivals, I work with Christie AW3s on the gear side of Century SA-TA projectors and thread in sort of a convoluted bottom-up/top-down fashion; soundtrack facing wall from platter to projector and facing away on the return trip.
First I thread the payout deck of the platter, run the film through the top projector guidance roller, give the film a half-twist, then take the film back to the platter and thread the takeup deck (yes, the "V" trick).
At the projector, I set the intermittent, then draw off slack from the platter takeup (triggering the motor and keeping the film off the floor), thread the lower guidance roller and failsafe, then clamp the film in place in the holdback sprocket of the R3 soundhead.
Next, I'll draw off enough slack from the payout side to load the film trap and intermittent, feed sprocket, idler sprocket, and soundhead, in that order.
Lastly, I release the holdback sprocket pad and feed off any remaining slack to bring the film into proper tension at the sound drum, then--as Mark recommended in the preceding post--manually advance the film to the proper starting point to ensure the film runs smoothly through the projector.
Whew. Thank goodness for AW3s! I could never pull this off with certain other platters (*cough* Potts *cough* Strong).
As to why I do it that way, the goal is keeping film off the floor. That, and because I never got the hang of threading in a pure bottom-up fashion.
| IP: Logged
|
|
|
|
|
|
Brad Miller
Administrator
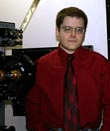
Posts: 17775
From: Plano, TX (36.2 miles NW of Rockwall)
Registered: May 99
|
posted 11-08-2008 01:31 PM
I'm going to pick on Tony for a minute because I see this all the time and it irks me.
quote: Tony Bandiera Jr With my FP-38's I pull the film from the feed reel, start the leader on the takeup reel and wind down until the 10' (Academy) is right in front of the lens.
Bad practice. Pull down just enough to reach the takeup reel, thread the projector and then motor (or POS if your projector has it) down to the starting area. Handling the film on the countdown is precisely why older films that have "never been plattered" look like absolute shit at the reel changes, and lets be honest here, even really bad film handling practices during buildup and breakdown to/from a platter don't make the film THAT crusty at the ends of the reels. Fact of the matter is Tony's procedure is handling the film TOO CLOSE (only a wrap or two away) from the first/last section of picture.
Sadly Dolby is a big part of this film handling nonsense. Ever since 1992 people running SRD have had to deal with NOT using the motor switch to prevent triggering a false changeover, and most techs are not intelligent and/or don't care enough to give their operators a motor switch that isn't connected to the Dolby system for advancing leader. The result is that even a spectacular projectionist running such a booth is forced to use Tony's exact procedure above.
Assuming you have a booth that does not have such traditional silliness in regards to a SRD system and you have one of those leaders with 50 feet of clear before any framelines start and you don't have any time to add some extra leader or put a few frameline marks an arm's stretch from the tip end, just throw the film "good enough" into the projector, motor it down and then adjust the film in the gate and check your loops then. The film is handled much less, and also the entire leader isn't dragged across the side of the reel and/or projector.
With that being said, I thread platters bottom up and reel to reel top down. With platters you have the stretch of film hanging over the top roller of the projector that has just enough weight to keep the film out of your way, and you can pull as needed easily, so bottom up is much faster and easier. With reel to reel the way I do it the film never reaches the floor anyway, and with a heavy reel to pull (often slung backwards over the lamphouse to accommodate a ceiling height restriction) it is faster and easier to thread top down.
The big question Joe didn't ask is...how do you thread your test loops???
| IP: Logged
|
|
|
|
Tony Bandiera Jr
Film God
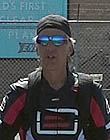
Posts: 3067
From: Moreland Idaho
Registered: Apr 2004
|
posted 11-08-2008 11:24 PM
While on one hand I do agree with Brad, there are several points that need to be considered:
First, most prints do not have sufficient leader(With proper frame lines far enough ahead of the first frame of picture (FFP)) to permit threading up and rolling down into the proper timing for changeover;
Since we don't run first run, we don't have a supply of trailers (a good idea BTW) to act as additional footage to thread up on;
A LOT of the prints I run are archival/last prints around and they take a very dim view of any "added" splices, especially in the leaders;
In most cases, I do wear editor's gloves (and if not, I have a restroom and wash my hands frequently while running) and I ALWAYS clean the machines between reels.
Finally, I have kelmar cleaners for both machines and use Film-guard as needed. And the aux roller on the film cleaner bracket allows me to wind the film down without contacting the projector frame or lens.
In short, while I can see the point Brad has made, I disagree that my threading method causes ANY dirt build-up that can migrate to the image areas.
The REAL problem with dirt/scratches on 80%+ of the prints I get is caused by the bad condition of the shipping cans (flaking cardboard inserts, etc.) AND people who don't properly secure the leaders. (See the "Hey you suck" thread..)
In 11 years of operations at my booth NOT ONE print has left with scratches/dirt caused by my handling or equipment, and this is as confirmed by the feedback from MGM and other archives. In fact the Korean Film Archive sent a very nice letter to my dept. head thanking us for CLEANING AND "RESTORING" their prints.
Having said that, I will state that I DO agree that it would be far better to have an extended leader, with proper frame lines, to thread up on. But until labs start providing them (or I revert back to a first run cinema with platters), I will continue to thread as I do and sleep soundly about it.
Edited to add:
quote: Steve Guttag Speaking of the Kinoton positioning button...for some reason, Kinoton has deemed it isn't needed on "ES" grade and above...we add the functionality back in because it is the right thing to do.
As much as those machines cost, I am dismayed that they took away the POS (Position) button. It is a far better way to advance the film instead of bumping the motor switch. Thankfully Steve is putting that function back.
| IP: Logged
|
|
|
All times are Central (GMT -6:00)
|
This topic comprises 6 pages: 1 2 3 4 5 6
|
Powered by Infopop Corporation
UBB.classicTM
6.3.1.2
The Film-Tech Forums are designed for various members related to the cinema industry to express their opinions, viewpoints and testimonials on various products, services and events based upon speculation, personal knowledge and factual information through use, therefore all views represented here allow no liability upon the publishers of this web site and the owners of said views assume no liability for any ill will resulting from these postings. The posts made here are for educational as well as entertainment purposes and as such anyone viewing this portion of the website must accept these views as statements of the author of that opinion
and agrees to release the authors from any and all liability.
|