|
|
Author
|
Topic: Interstellar locations running in 70MM
|
|
|
|
Brad Miller
Administrator
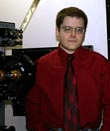
Posts: 17775
From: Plano, TX (36.2 miles NW of Rockwall)
Registered: May 99
|
posted 10-01-2014 02:49 PM
The 3 Dallas locations are ours, using my personal equipment. It was the only way to make it happen because the gear just doesn't exist anymore. Remember any location wanting to run this in 70mm not only has to have a 70mm projector, but a suitable lamphouse, 2-projectors or a platter (hopefully a Christie) WITH conversion kit to run 70mm, a functioning MUT, 70mm splicer, dts70 readers, functioning dts players, the know-how to set it all up properly (so as not to damage the print), a projection staff with 70mm experience (since it is not the same as running 35mm) and any theater worth a flip needs a 70mm gauge film cleaner and FilmGuard as well.
That's a tall order with film being essentially dead at this point in time...particularly 70mm capable equipment. If any one item is missing, then it's a no-go.
| IP: Logged
|
|
|
|
|
|
|
Brad Miller
Administrator
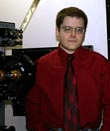
Posts: 17775
From: Plano, TX (36.2 miles NW of Rockwall)
Registered: May 99
|
posted 10-02-2014 12:18 AM
I'll probably bounce around and pull a few shifts at all 3 of them. It just depends on how we end up handling the staffing.
I don't have a lot of time tonight to be too detailed here, but I can type pretty fast so I'll rattle off for a bit. (Don't consider this a comprehensive list though.)
Lots of people think to run 70mm all you have to do is change the rollers out on the platter (assuming a platter is used) and flip the rollers around in the projector and change the gate/trap/shoe/etc in the projector head. Sure you CAN do that and run 70mm, but you aren't doing it right if that is your procedure.
In the mag days, 70mm was more fragile than 35mm. With 35mm twists in the film was nowhere near as big of a deal as with 70mm. The entire projector and everything touching the film had to be carefully degaussed in order to ensure the mag tracks weren't erased (the high frequencies would go first, but thumps and such could easily occur). Loop sizes were also more important due to the 70mm slapping more than 35mm. Also the gate tension in particular was far more critical. Too little tension and the picture will bounce, but too much tension and you will strip out the intermittent. In this day and age, a lost intermittent is not a good thing either.
Today's 70mm prints have dts audio, so there is no degaussing concerns, but they are also polyester, which means they are annoyingly tough and also bring static to those not smart enough to use FilmGuard. This is precisely why Paramount reportedly had to replace at least reel 10 on all of the 70mm prints of Titanic (except the one I played). Of those, many had to replace as much as the last half of the movie due to various print damage that is easier to achieve towards the end of a long movie when running on a platter.
So think about this for a minute. On a Christie platter for example, to get 70mm speed at the center ring you've got to hit about 25RPM for it to barely be able to keep up. That's not a big deal for the machine to achieve, but it's faster than 35mm needs to run so if there is static the payout arm has a better capability of slinging the print towards the end of the movie.
But that's not the fun part. On a longer print, like Titanic or Interstellar that runs 3 hours, you've also got sheer weight running against you, which translates into inertia. As anyone that has ever paid attention to the takeup arm will recall, it is common for there to be a slight bounce in the takeup even if only because of a tiny bulge in the film roll where the leader was secured to the center ring. Normally those bulges don't matter much, but when you have a 200+ pound print and that takeup arm starts bouncing more than just the tiniest amount, suddenly each bounce speeds up the platter, then inertia overspins the takeup, then the next bounce is a little harder with more speed, and then the inertia overspins the platter a little bit more. Suddenly you've got the takeup arm crashing into the motor, flipping the film crooked on the roller, scratching, damaging and stretching sprockets. This can actually go on for quite some time without killing the show on screen when running 70mm polyester prints! With 70mm acetate, it would simply snap the first time it hit, the failsafes would drop and that was that.
This is why very careful timing of the platter is critical. Even pre-testing with a 2 hour movie is no good when you are running a 3 hour movie! (Plus each deck is independent, so the 3 hour test show would have to be run 3 times, one test run per deck.)
Using the Century JJ as an example, a mandatory part of converting the machine is to remove the upper 35mm pad roller. The reason this is so critical is because a normal acetate 70mm print will have a certain amount of slap to it, and if threaded PERFECTLY, then yes you can run it without getting the infamous "JJ scratches", but with a polyester print (anything in dts will be polyester), it's simply impossible to run the print with that pad roller and not scratch it. Sure the scratch is extremely light with one pass and most people would not even notice it, but the more time it is played, the worse it gets. The solution is simple, but not everyone does it. Simply remove the 35mm pad roller from the shaft. (Personally I replace it with another 70mm pad roller, but that isn't necessary.)
Now take a look at the lower loop. Again we have the same issue. 70mm slaps more than 35mm, and 70mm polyester slaps WAY more than 35mm. Without some form of slap guard, you WILL scratch the print. On a Century this translates into horizontal lines down the center of the picture where it slaps up against the bottom of the intermittent shoe. (Note it is difficult to even tell that it is hitting the shoe just when looking at it.) Century has studio slap guards that can be attached to the intermittent (if you can find them) which is the ideal solution, but what most JJs have is a little loop stabilizer roller underneath. Many people thread over that roller, but due to the way the 70mm film slaps and curls, it's actually proper to thread under that roller. If you don't have that roller, you will most certainly be inflicting some level of damage. Again it may take a number of shows to truly see it on screen, but it's happening. In this case, the smaller the loop, the better.
I mentioned before that 70mm doesn't handle twists as well as 35mm does. This isn't as big of a deal with polyester prints as the old acetate mag prints, but I've seen many theaters with short lengths between twists actually see tears and film breaks in their acetate shows because of it, and I can't tell you how many prints I've seen where the first couple of minutes have all kinds of nasty stretched sprockets on it. With that being said, it is truly imperative to use LOTS AND LOTS AND LOTS of leader! There is no excuse not to. Thread it up and motor it down. I prefer to put a solid 2 minutes worth of abort leader on the prints to give the projectionist more than adequate time to verify that everything is running absolutely perfect before they possibly damage even one frame of the movie.
So how do you help prevent bad things from happening? Here is a quick list...
*Align the gate/trap for the particular thickness of film you are running. Just because the 70mm film shuttles when you flipped things around does NOT mean that you are not inflicting unnecessary wear on the sprockets and your intermittent.
*Remove that 35mm upper pad roller (again, assuming Century JJ).
*Get studio slap guards or at least the loop stabilizer roller underneath the intermittent.
*Use the oversized center rings and calibrate your platter speeds down for them. Even a long movie like Interstellar will still fit onto the platter with an oversize center ring, and with the platter only being able to max out at around 17RPM is a very good thing as you get towards the end of the movie.
*Don't forget to re-calibrate your platters. You want to just barely be able to achieve minimum startup speed, and you must ensure there is no "bump" in the speed from zero to high.
*Buff your platter decks. You don't want ANY burrs in the surface. The grooves brought about during buffing also helps hold the print where it needs to be and prevent slinging.
*Run FilmGuard on every show. Yes, every single show. With it you won't see a hint of static, nor even any dust on screen for that matter, and it will also prevent most loop size mistakes from translating into a scratch. This should be a law for anyone running expensive 70mm prints...and particularly with acetate magnetic 70mm prints, it's a godsend. (No shedding, no brittleness, no soundtrack wear and no oxide flaking.)
*Find some Film-Tech safety rings. We don't manufacture them anymore, and no we don't have even a single one left in stock, but find one. They fit over the edge of the platter and make it impossible to throw a print if things start to go bad.
*Watch your loops and use tons and tons of leader. Remember this print cost over $20k, so spend that extra time triple checking everything both turning the mechanism over by hand and also running the leader down for a minute or two at full speed to check the entire film path.
*Don't have stupid twists in your film path. Angle the platter a little bit if you need to minimize them. Extend your projector rollers, and ensure at least the upper one is straight up and down and not angled in the event of a payout bounce from a knick on the platter surface or a splice made with cheap splicing tape.
*If running changeovers, go back to that leader rule. ADD MORE! And whatever you do, don't attach the leader to the takeup reel and spin it until you get to the countdown before you thread. That's the absolute incorrect way to do it. Ensure you have some framelines to thread on at the beginning of the newly-extended leader (even if you have to draw a dozen with a Sharpie over clear leader), thread there and then after you are sure you are comfortable with the threading motor it down to the countdown. The reason so many repertory prints look bad around the reel ends is because people are handling the films too damn close to the first and last frame of action on each reel. (This rule even applies to proper 35mm changeover operation.)
There are other tips to follow, but I wouldn't know how to write them out. It's for more of a one-on-one training session. Those are the main points that everyone should be able to follow via text though.
| IP: Logged
|
|
|
|
|
|
|
|
All times are Central (GMT -6:00)
|
This topic comprises 23 pages: 1 2 3 4 ... 21 22 23
|
Powered by Infopop Corporation
UBB.classicTM
6.3.1.2
The Film-Tech Forums are designed for various members related to the cinema industry to express their opinions, viewpoints and testimonials on various products, services and events based upon speculation, personal knowledge and factual information through use, therefore all views represented here allow no liability upon the publishers of this web site and the owners of said views assume no liability for any ill will resulting from these postings. The posts made here are for educational as well as entertainment purposes and as such anyone viewing this portion of the website must accept these views as statements of the author of that opinion
and agrees to release the authors from any and all liability.
|