|
|
Author
|
Topic: Screwcutting.
|
Stephen Furley
Film God
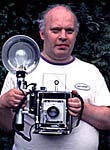
Posts: 3059
From: Coulsdon, Croydon, England
Registered: May 2002
|
posted 01-01-2012 06:11 AM
I've done plenty of screwcutting in my time of just about every type, multi-start threads, left hand threads, imperial threads on metric lathes, module and D.P. worms etc., but there's something that's always puzzled me. A srewcutting lathe needs a leadscrew, which needs a screwcutting lathe to make it. You can guess what the question is, how do you produce a screw in the first place, without a leadscrew?
I can think of a number of ways to generate a screw manually, but most of them would not be very accurate. About the best that I can come up with would be to take a rod, and wrap around it in a helix two narrow strips of material side by side, with the width of each being equal to half the pitch of the screw required. One would be fixed in place on the cylinder, and the other one then removed. Was it done in this way? If not, has anybody got a better idea?
| IP: Logged
|
|
|
|
|
|
Stephen Furley
Film God
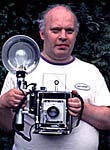
Posts: 3059
From: Coulsdon, Croydon, England
Registered: May 2002
|
posted 01-01-2012 03:20 PM
Generating a screw from a flat die is an interesting idea, but I've only ever seen it done for short threads of smallish diameter. Could it be scaled up to produce something like a lathe leadscrew?
Cutting gear teeth with a simple form cutter on a milling machine is ok for gears which do not run at high speeds or transmit large amounts of power, I've cut clock wheels and pinions myself this way, but the problem is that you need a dividing head, and that needs gears. How do you make those gears in the first place?
For high speed or high power applications the tooth shape really needs to be generated. Traditionally, there have been three main ways of doing this, gear planing with a rack cutter, gear shaping with basically a gear wheel with cutting edges, and hobbing. All of these machines normally use gears in their operation. The teeth on the rack cutter would be straight-sided, and would be the easiest to produce. I cannot think of a way to produce a gear shaping cutter without using pre-existing gears. To make a hob would require both a leadscrew and a relieving shaft on the lathe, both of which would require gears to drive them. Of course, screwcutting also requires gears to drive the leadscrew.
I can think of ways to make the large gears with inserted wooden teeth as were used in things like windmills and watermills with nothing more than simple hand tools to an accuracy which would probably be close enough for the purpose, but that's a long way short of modern gears.
| IP: Logged
|
|
|
Simon Wyss
Film Handler

Posts: 80
From: Basel, BS, Switzerland
Registered: Apr 2011
|
posted 01-02-2012 08:31 AM
It is easier to make a cog wheel than a screw. You need a dividing device that allows you to rotate something by a certain number of degrees. Its hole disk can be made by hand, I mean one makes scribes across a round flat with the help of a centering angle. Twelve equal sections give us 30 degrees for example. Cog wheels can be cast, forged or pro-forged, broached, milled, ground.
Once you have gears you can make a lathe which advances the slide or saddle in a certain ratio relative to the spindle rotation. Later on you add a mainscrew to the gear stock.
First class mainscrews are forged (rolled), then stress-relieved, milled, hardened, and ground.
| IP: Logged
|
|
|
All times are Central (GMT -6:00)
|
|
Powered by Infopop Corporation
UBB.classicTM
6.3.1.2
The Film-Tech Forums are designed for various members related to the cinema industry to express their opinions, viewpoints and testimonials on various products, services and events based upon speculation, personal knowledge and factual information through use, therefore all views represented here allow no liability upon the publishers of this web site and the owners of said views assume no liability for any ill will resulting from these postings. The posts made here are for educational as well as entertainment purposes and as such anyone viewing this portion of the website must accept these views as statements of the author of that opinion
and agrees to release the authors from any and all liability.
|