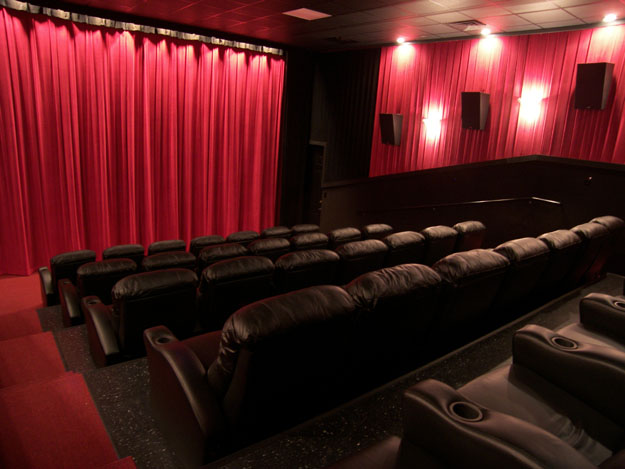 This is the current Film-Tech screening room.
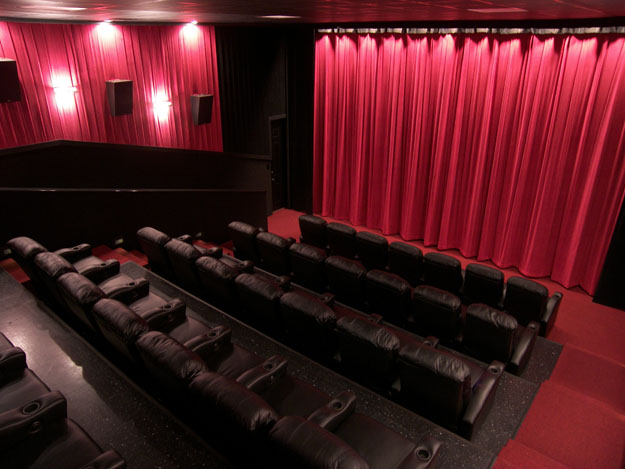 There are two major changes in the design of the auditorium from the previous screening room. As you can see here, curtains were added...
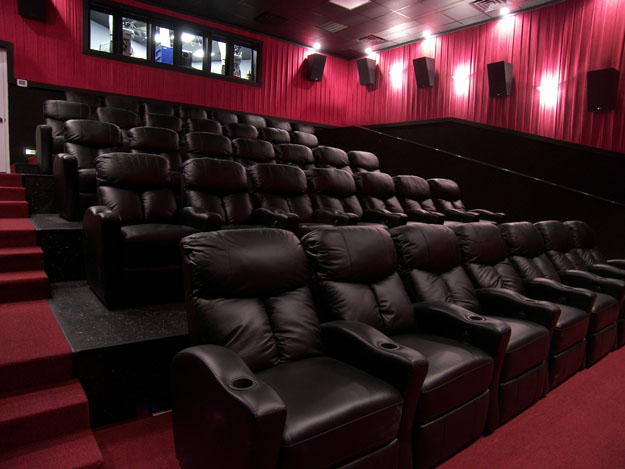 ...as well as a much steeper stadium seating.
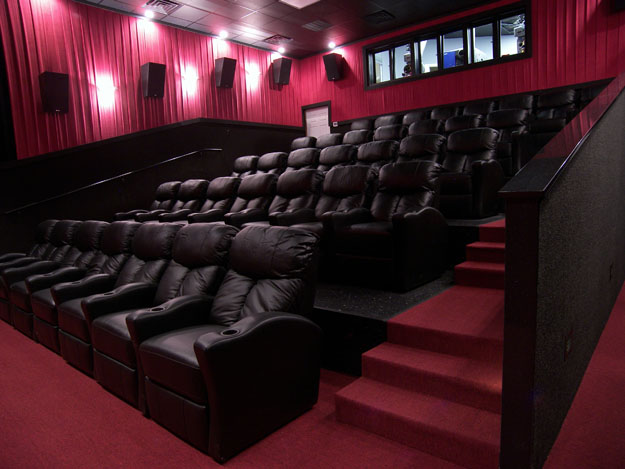 The sound system was also upgraded to QSC speakers, but more about that later in the tour.
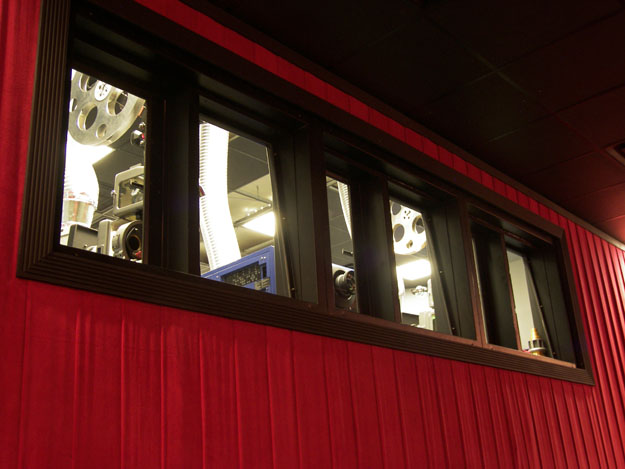 The port windows have expanded to make room for digital cinema as well as the traditional film setup.
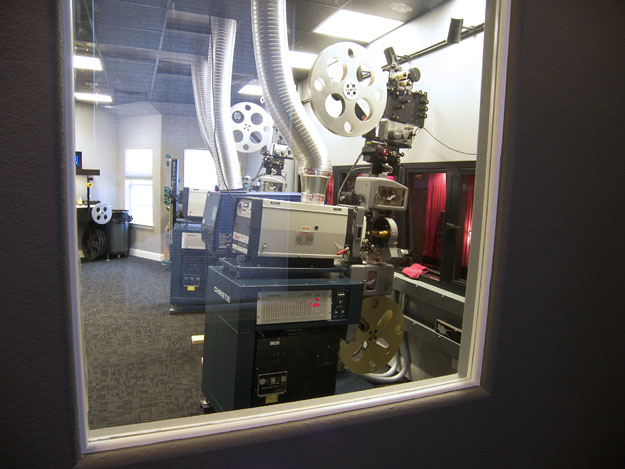 Here is the booth as viewed through the "viewing window" in the hallway leading to the booth.
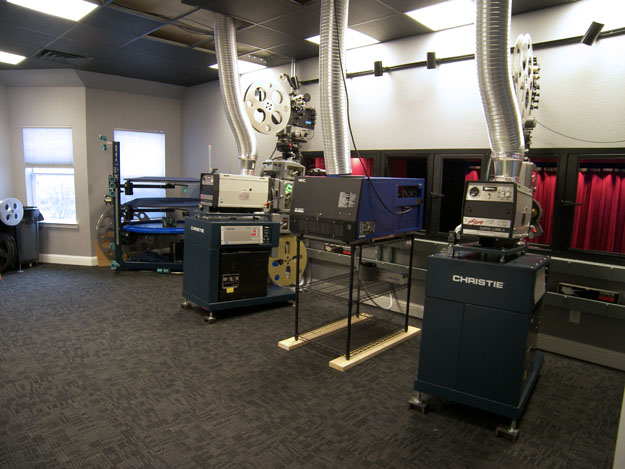 Inside we will see a familiar setup, but with much, much more space. This is the booth as viewed looking right.
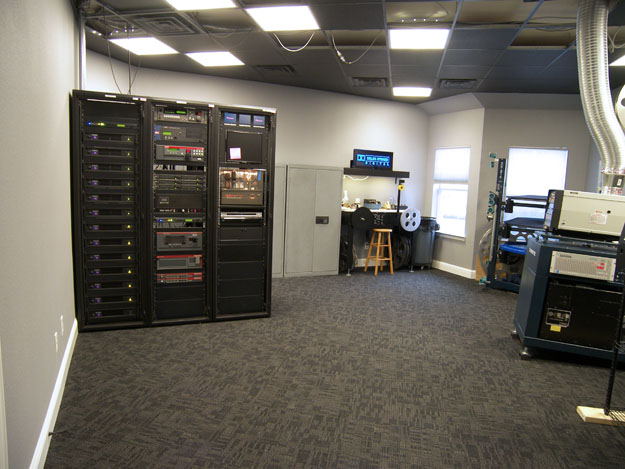 This is the booth as viewed looking toward the left. The sound racks aren't actually up against the wall, they are about 4 feet forward to permit easy access.
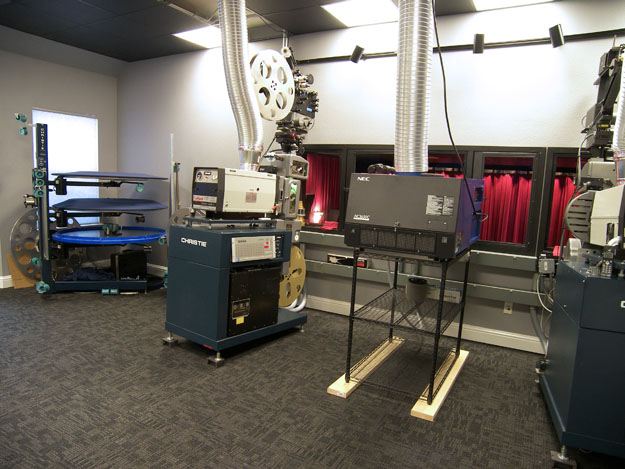 35mm and 70mm film may be ran here via platter or automated changeover. The digital projector pictured here is a temporary install as we are currently evaluating the NEC projector.
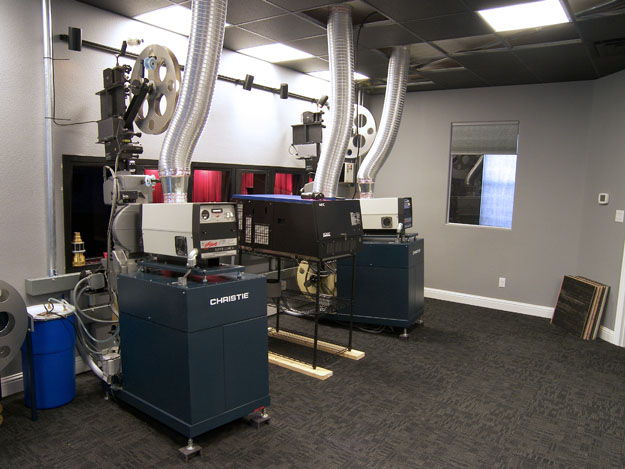 The room is not officially "finished" at this point, as evidenced by the missing ceiling tiles and temporary wiring. (We are waiting for the new Christie lamphouses to arrive.)
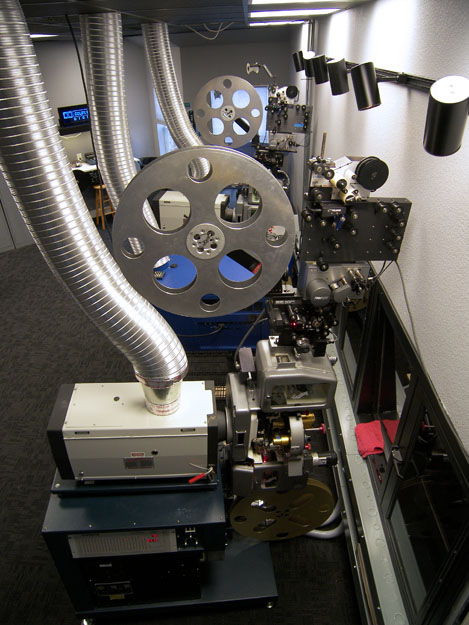 The penthouse stack got a bit taller this time due to the addition of a custom delay bracket. In this setup there is a cue reader just below the film cleaner which reads cues to trigger the opposing projector to initiate a changeover. The actual cue is placed 4 frames after the last frame that is desired to be projected, making for effortless cue'ing of new films without a frame counter. By the time the final frame reaches the aperture, the other projector is up to speed and the system performs a frame-accurate changeover every time. (Similarly, there is a cue point of where the "first frame to be projected" sits on the incoming projector. This eliminates the concern of missing frames in the countdown leader.) Of course, CA21 automations are used. There is no substitute.
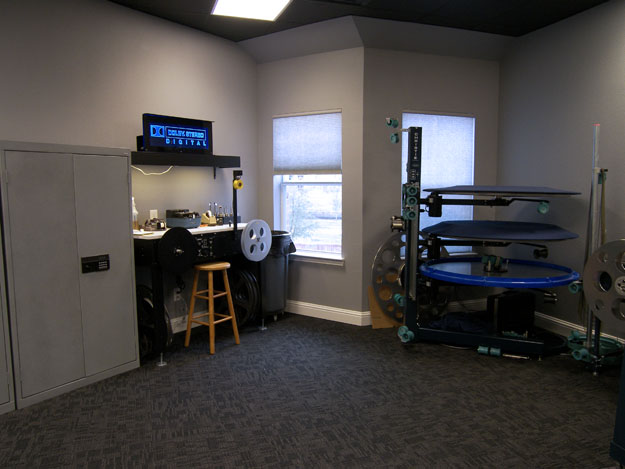 The platter sits out of the way in the corner along with its MUT that can be left connected at all times since the booth was designed in such a way that that MUT's storage location is also its operating location. The rewind bench sits next to the window, which all booths should have.
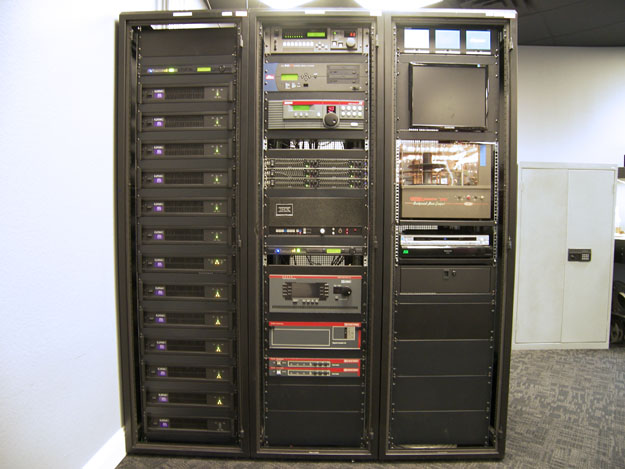 From left to right we have a rack of QSC DCA amplifiers. The stage speakers are 4 way with bass shading, hence the quantity of amplifers. In the middle rack is SDDS via a DFP-3000, DTS via an XD10, Dolby Digital via a CP650, a blank space for a DMA8+ which has not yet arrived, user EQs for poorly mixed content, the THX crossover (which is merely being used as a booth monitor), a QSC Basis system (one for each Dolby processor...the lower one has not yet been installed), a Dolby CP500 for running magnetic content, along with the necessary MPU-1 and PS1B supplies. The right rack is where the DCI server will go, but the most important item in this rack is the Seeburg Background Music System for non-sync content. (Google it to learn of its awesomeness.)
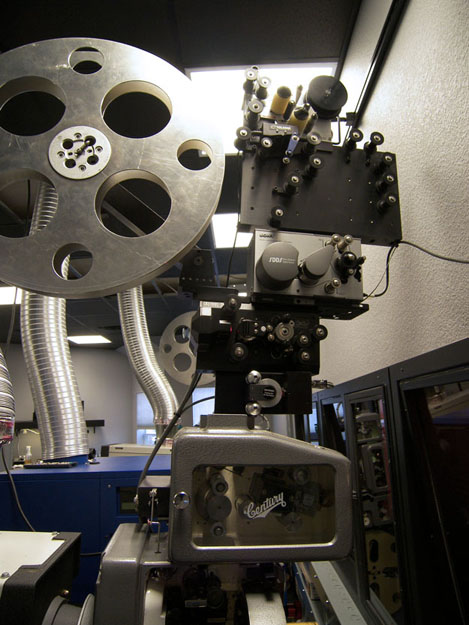 A closer shot of the newly revised penthouse stack.
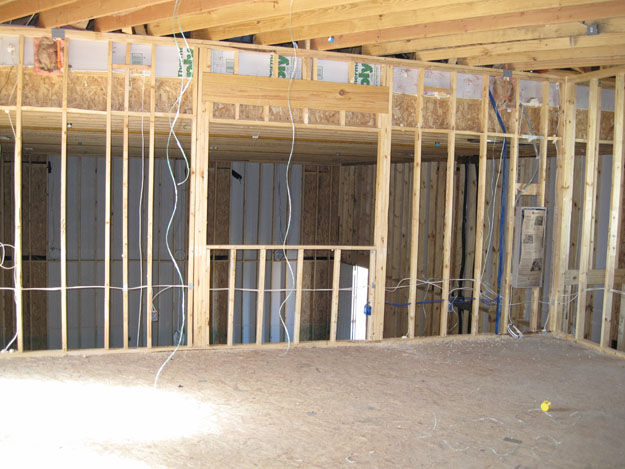 That was now, this is then. Pictured here is how the room started.
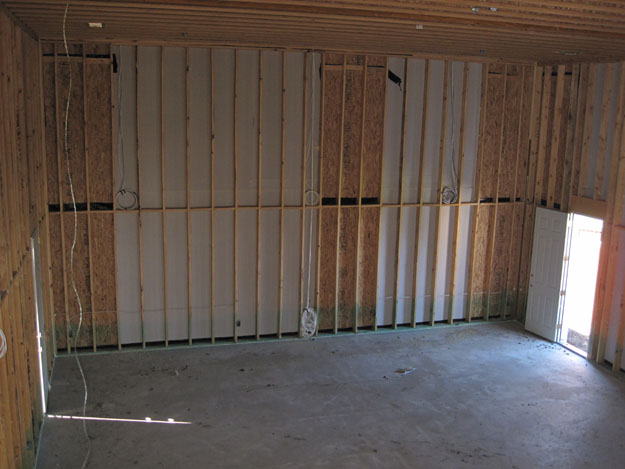 This was the auditorium. At this point the only thing that has been done is speaker, network and control lines have been ran.
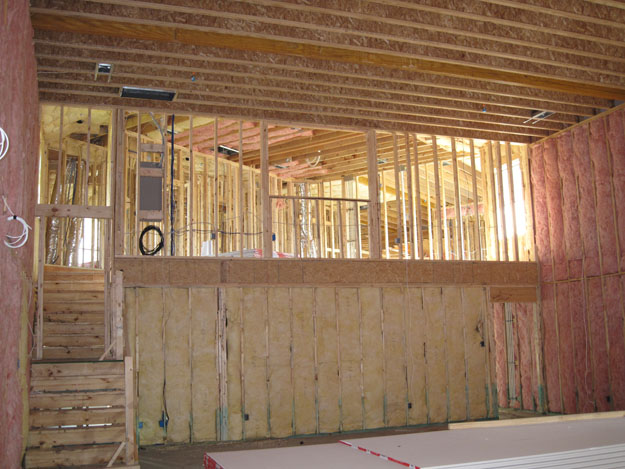 Reverse shot of the room as the first layer of insulation starts to go up.
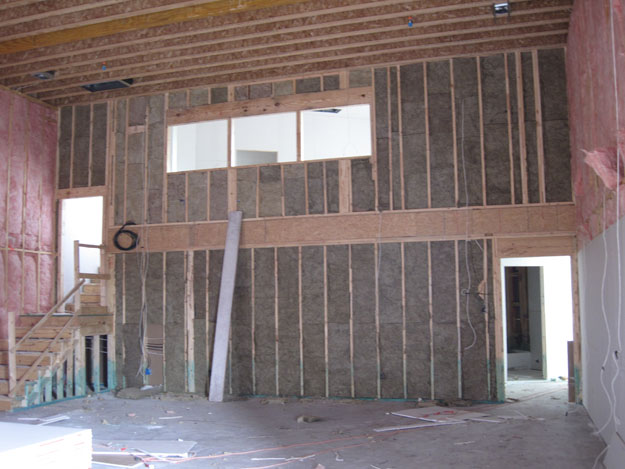 And then a second layer is added.
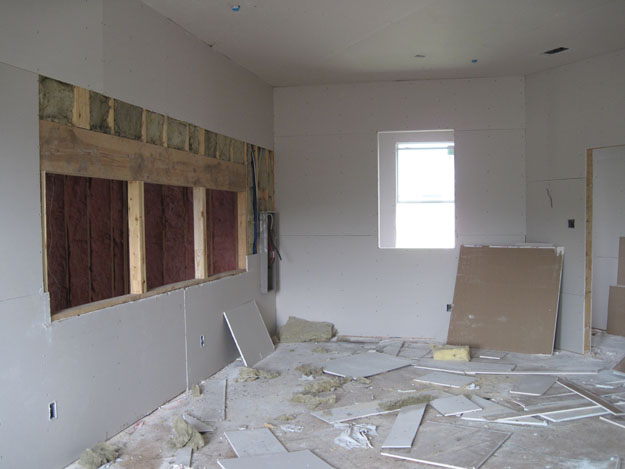 The booth gets it's drywall.
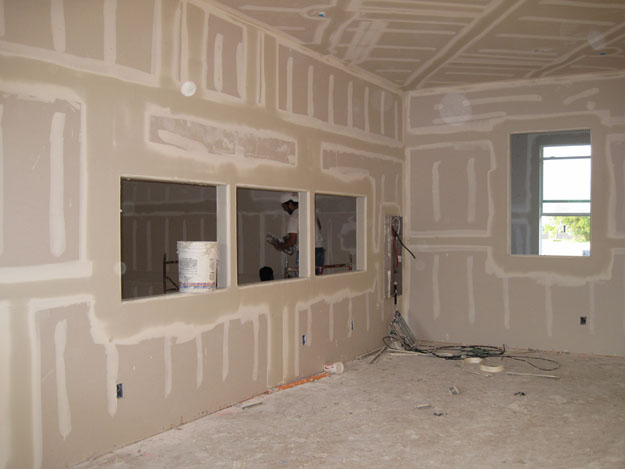 The drywall is now done.
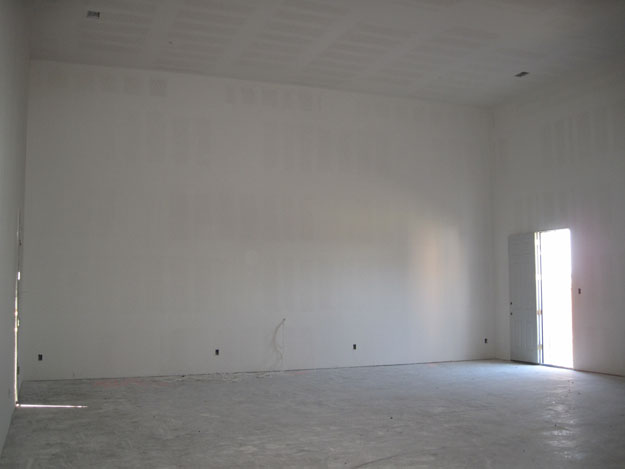 Shot of the screen wall in the auditorium.
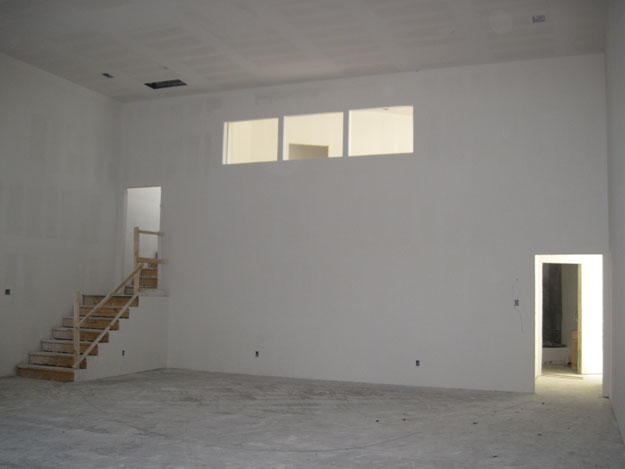 Shot of the booth wall in the auditorium.
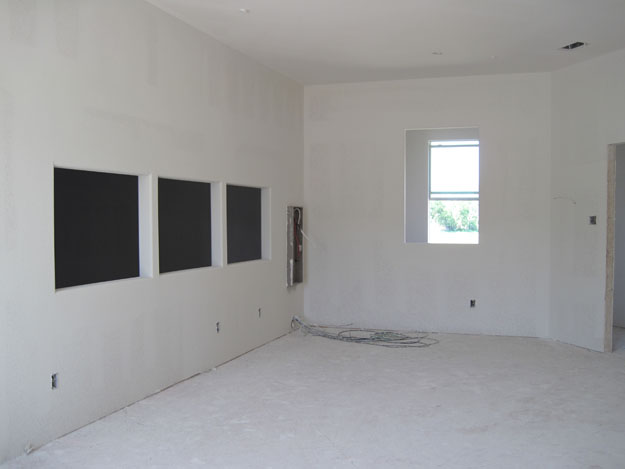 The booth is almost done (as far as the builder is concerned).
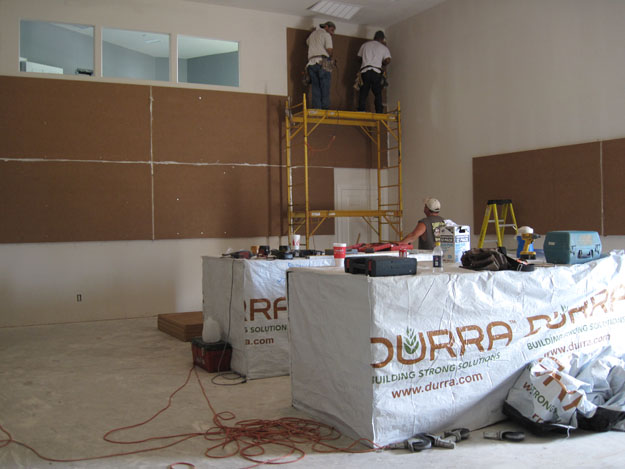 Now comes the good stuff...DURRA!
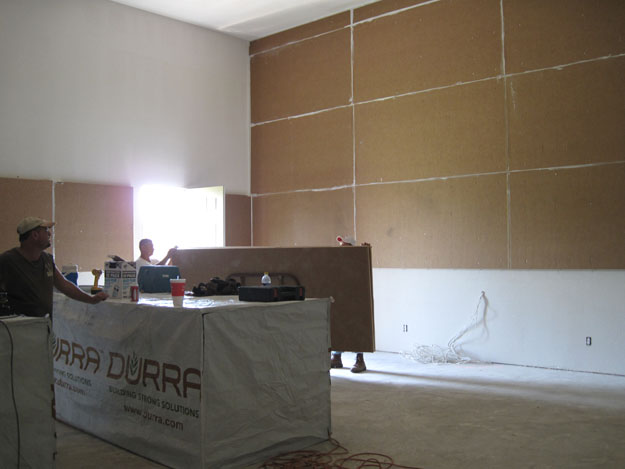 Rock-N-G Drywall was hired to install Durra's Type 8 wall.
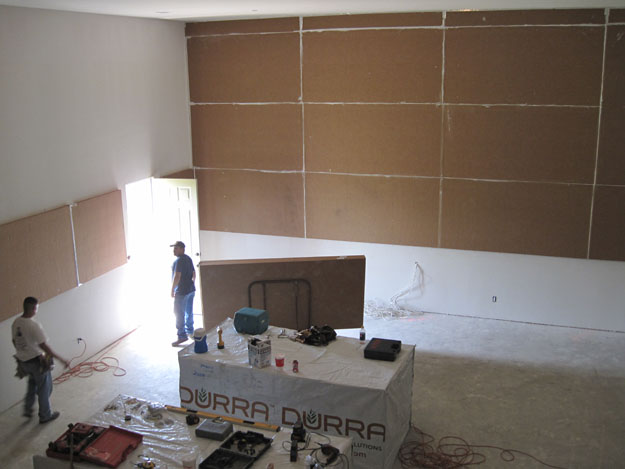 More Durra installation.
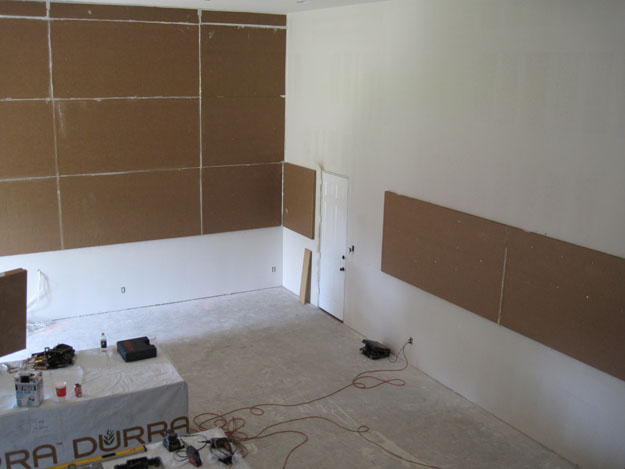 More Durra installation.
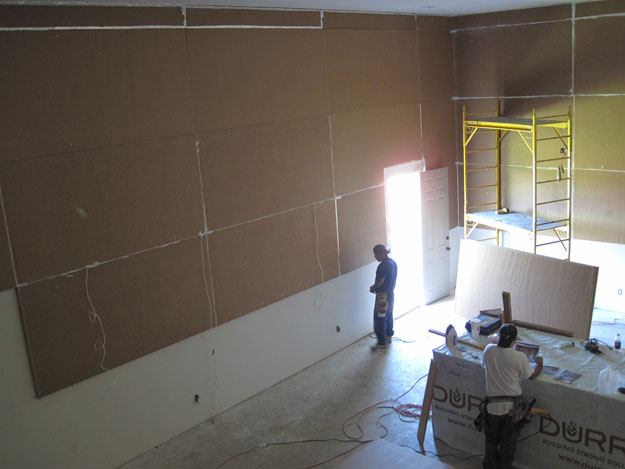 Almost finished with the first layer.
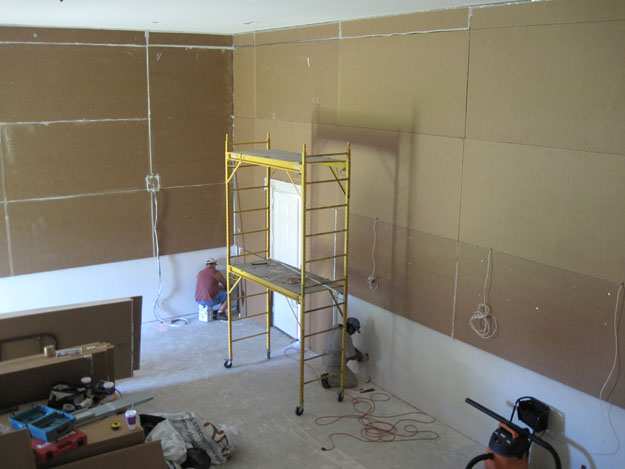 Here the speaker lines have been pulled through the Durra.
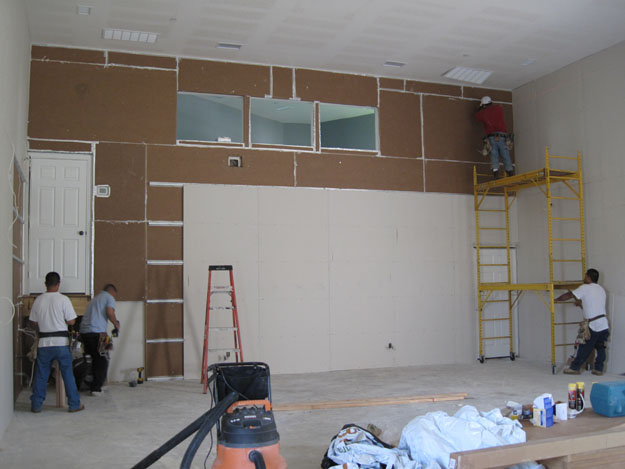 Here you can see where the furring channels have been added on top of the Durra and then another layer of sheetrock is being added.
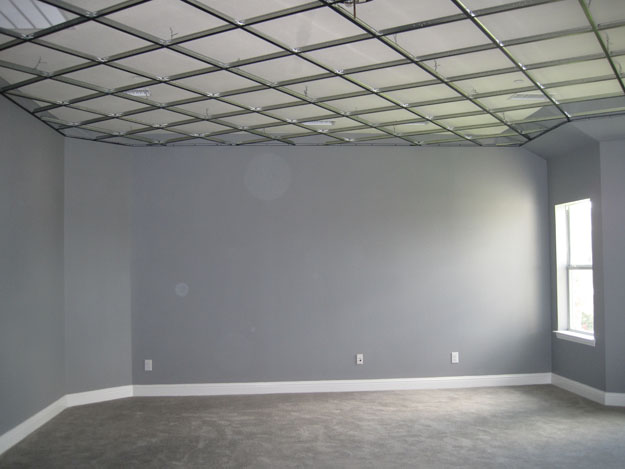 Meanwhile the drop ceiling grid in the booth has been finished.
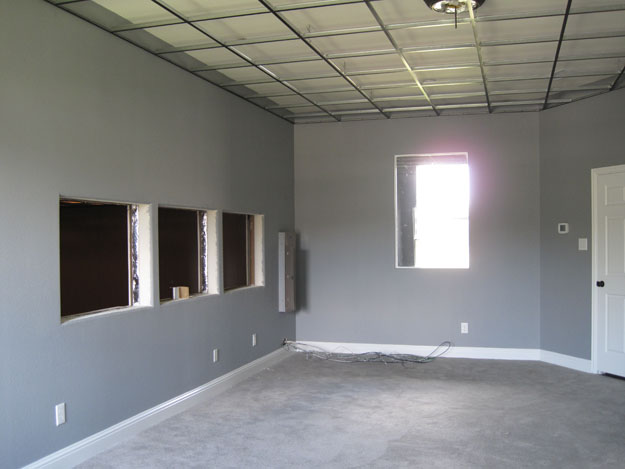 Another shot of the booth after the drop ceiling grid has been installed.
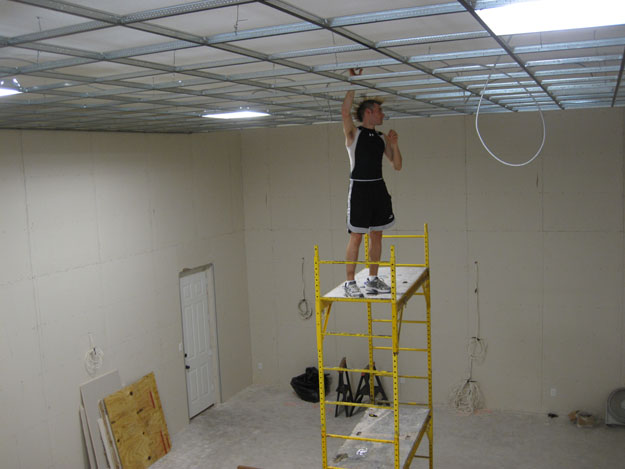 The drop ceiling in the auditorium is also finished at this point and the cleaning lights as well as the can lights are being installed.
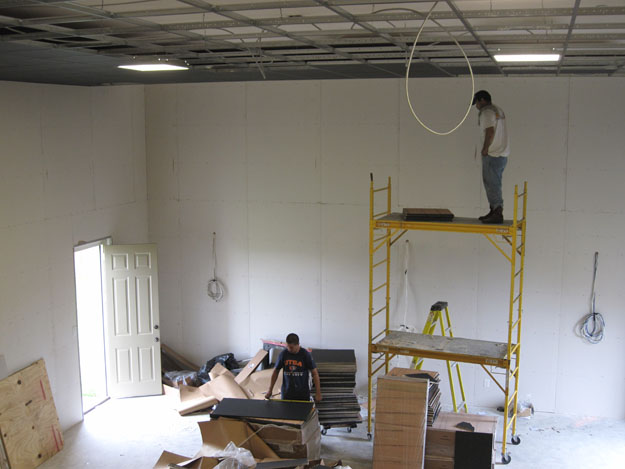 The drop ceiling tiles are now being added.
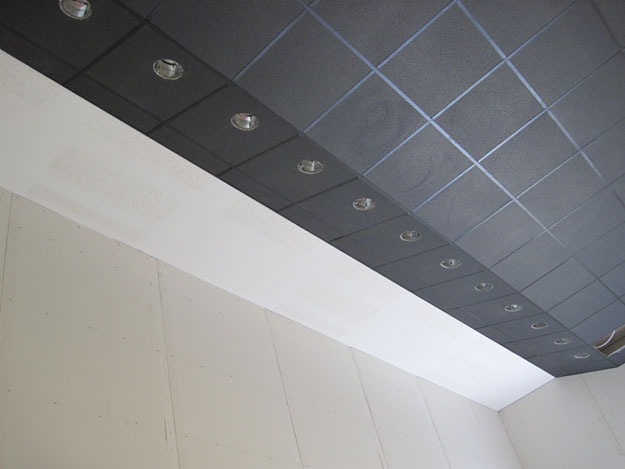 Here is the finished edge of the drop ceiling next to the curtains. The front edge has been tilted so that the lights shine onto the curtains better.
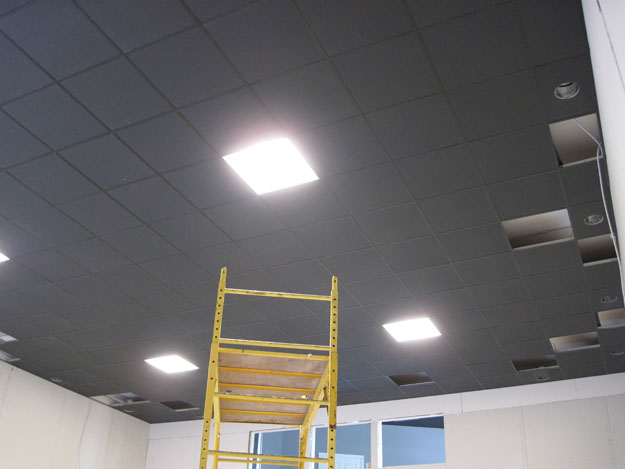 This is the drop ceiling as the HVAC vents are being brought down into the grid.
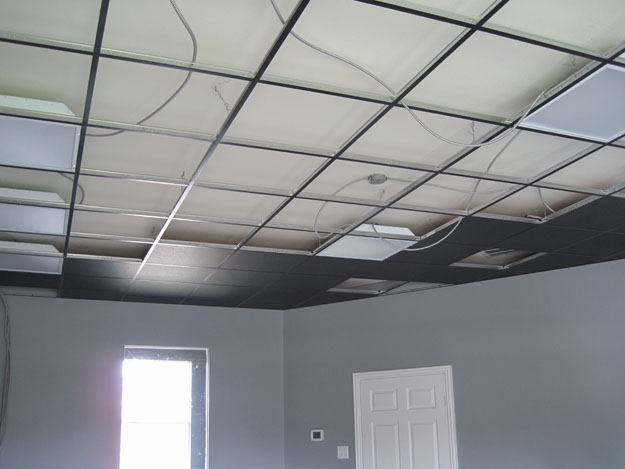 Similarly the same thing is going on in the booth.
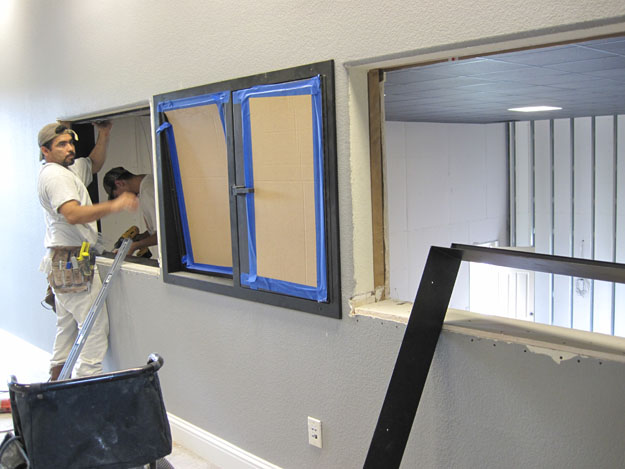 It is now time for port windows.
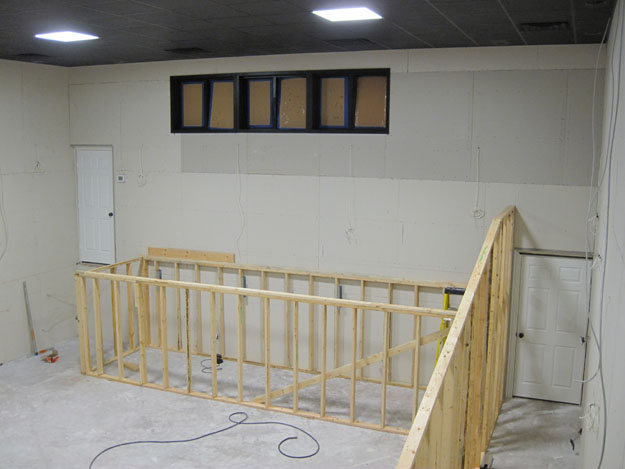 Next comes the stadium risers.
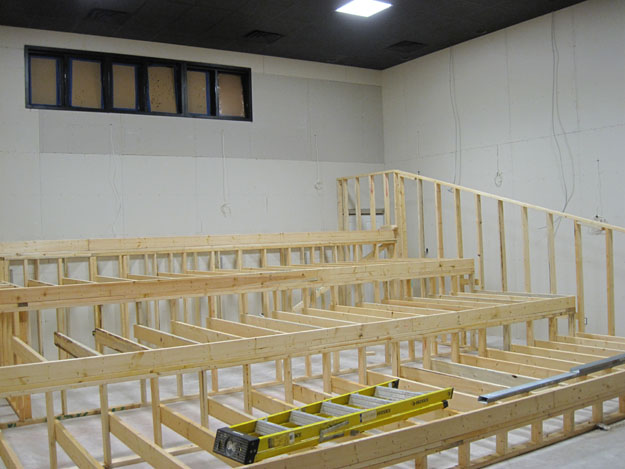 The framework is now complete.
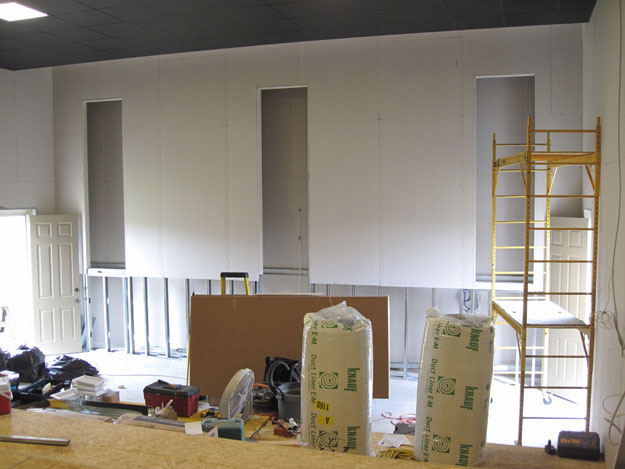 Meanwhile, progress begins on the speaker baffle wall.
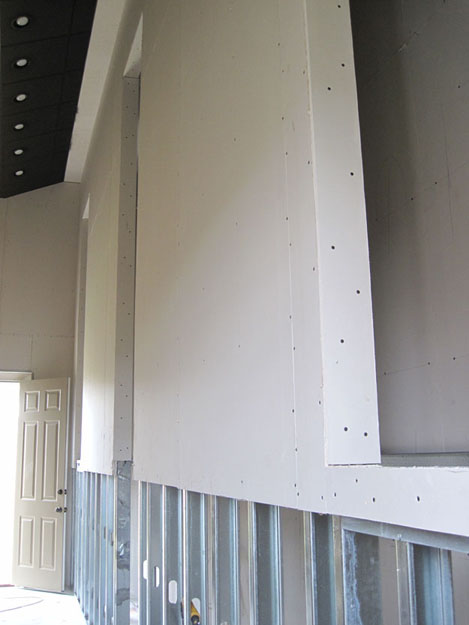 This picture better shows the angled lights that will shine on the curtains.
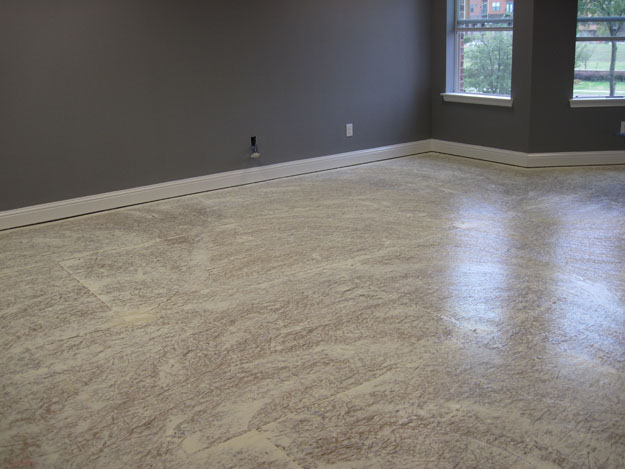 The floor of the booth has been prepped and is ready for carpet.
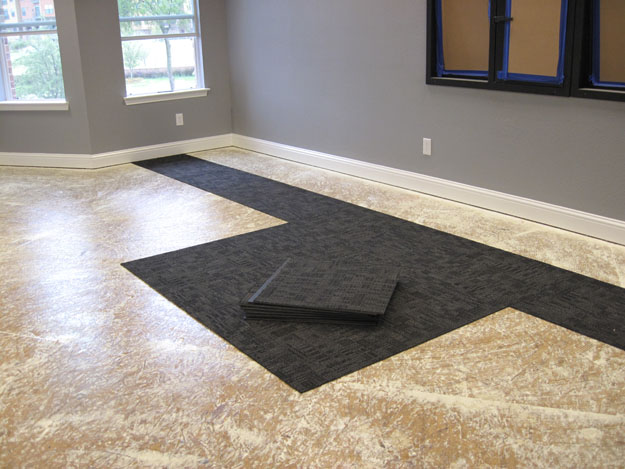 Carpet squares are being used in the event there is damage to a section of carpet. This makes changing out a section near-effortless.
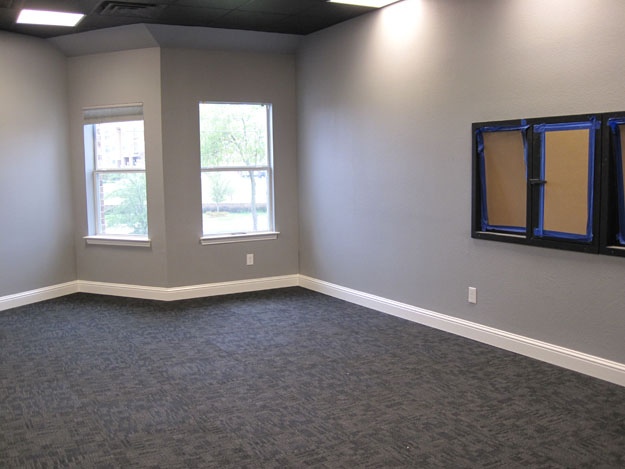 The carpet is now complete.
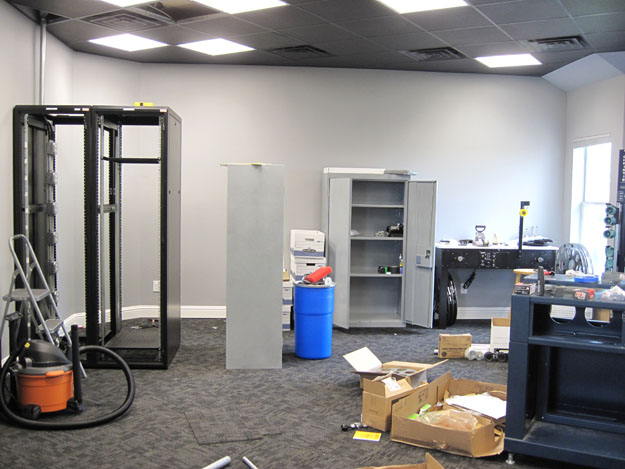 The first items are brought into the booth.
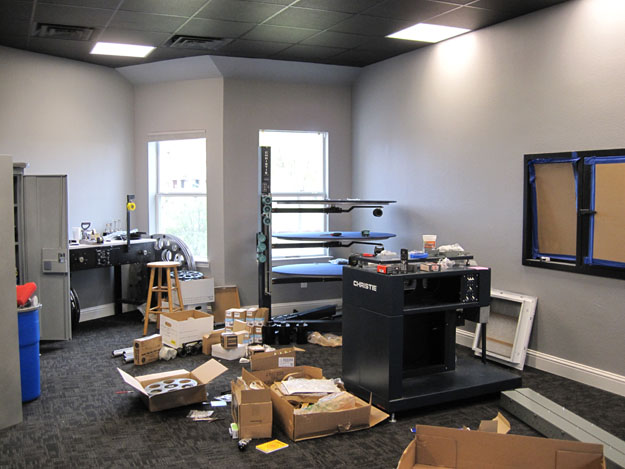 At this point it is mainly electrical work to be performed.
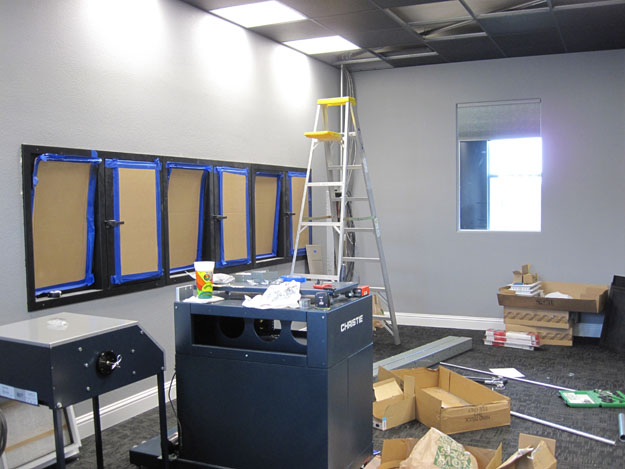 The first piece of conduit has been ran...
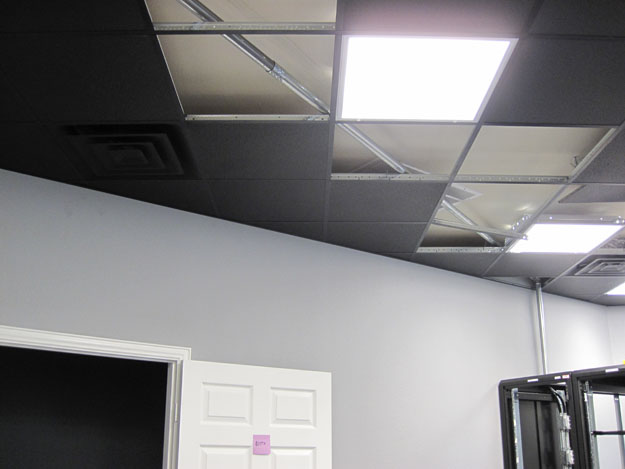 ...up over the drop ceiling and into the sound rack...
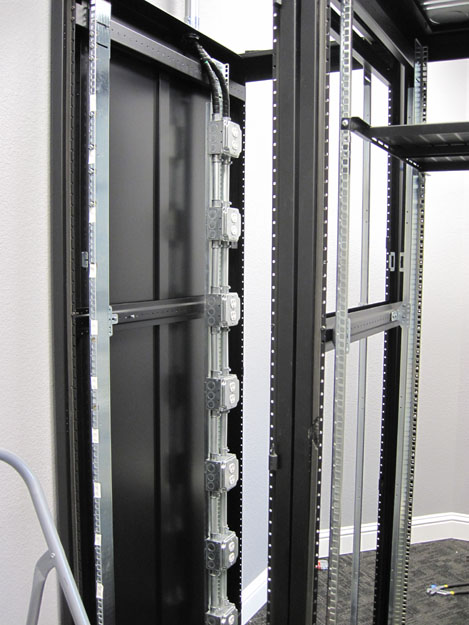 ...to provide all of the circuits to power the sound system.
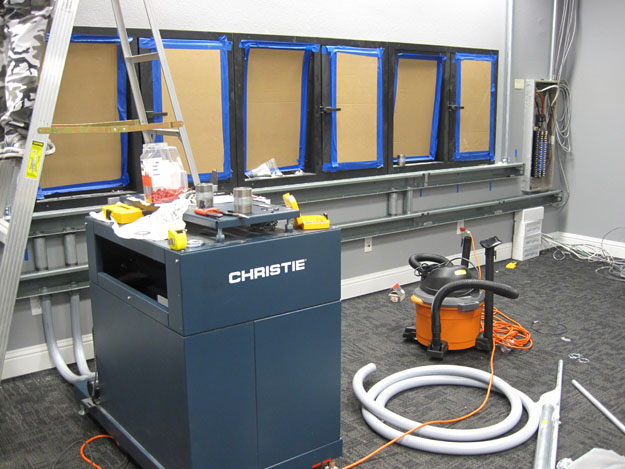 Here the high and low voltage wireways have been installed.
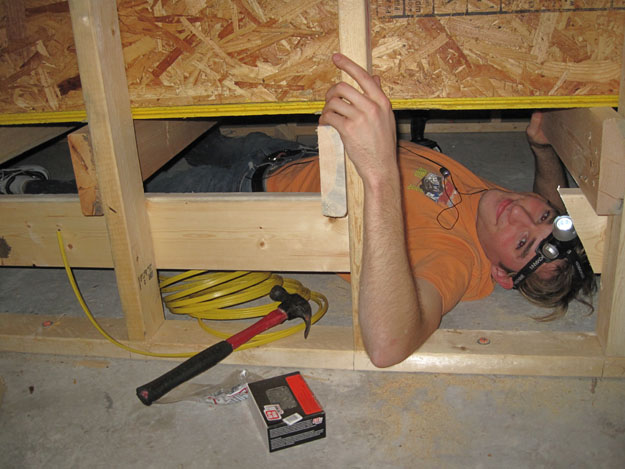 Power is added underneath the stadium risers for the motorized recliners. Just look how happy Josh is!
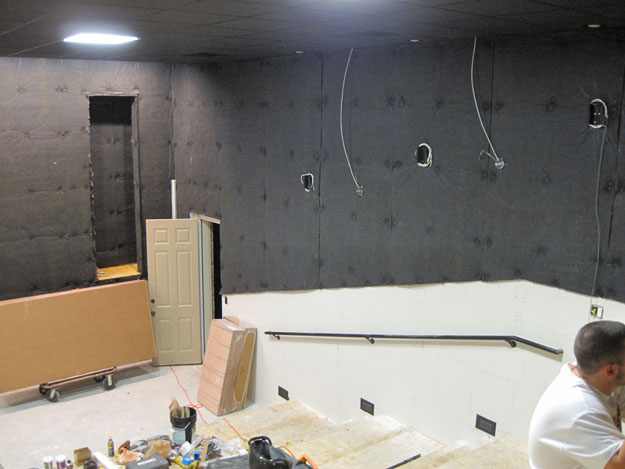 Duct liner has been added to the walls, sconce light conduit has been ran and speaker brackets are mounted.
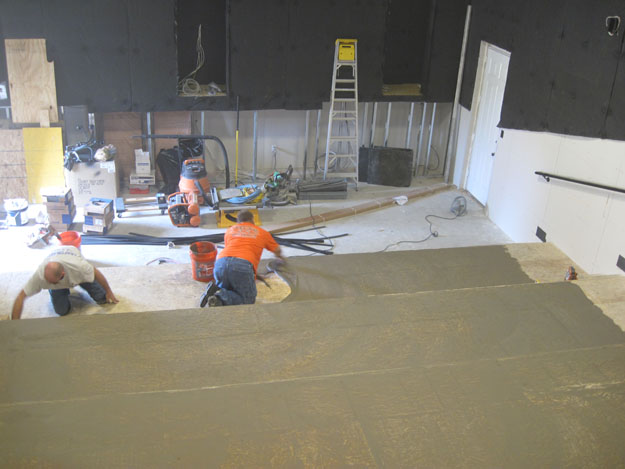 It is now time for the floor.
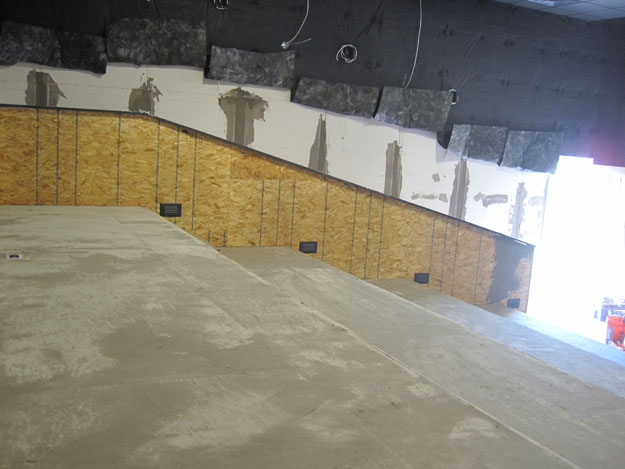 This step was necessary to smooth out any imperfections in the wooden risers.
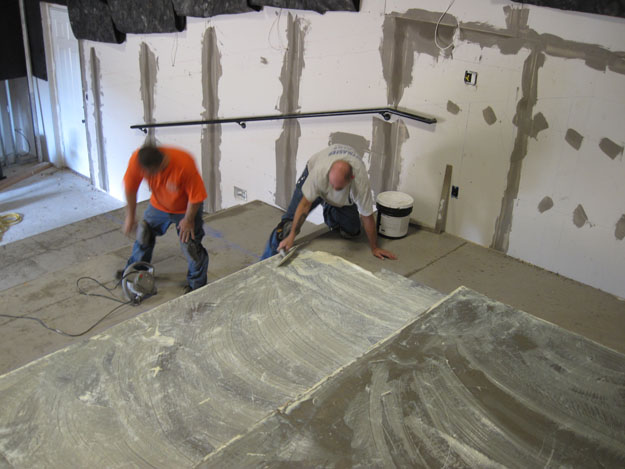 Here the glue is being applied to the floor.
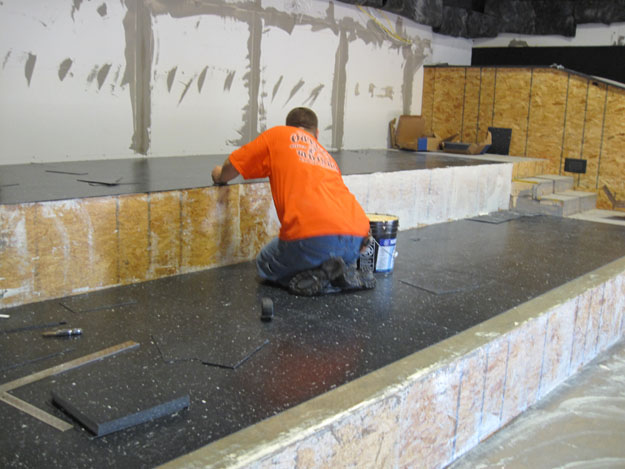 Tiles are then put into place.
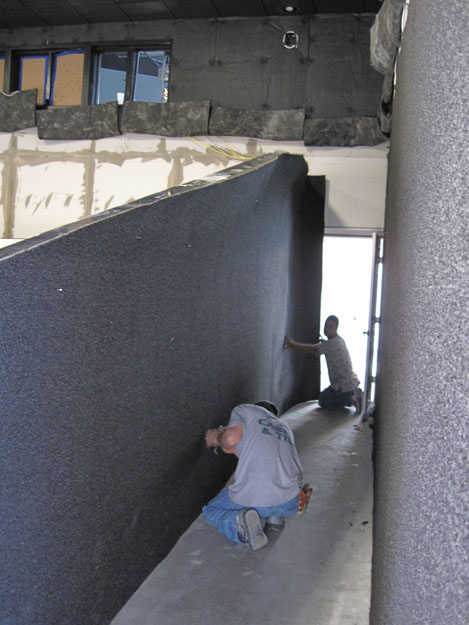 Meanwhile wall carpet goes up.
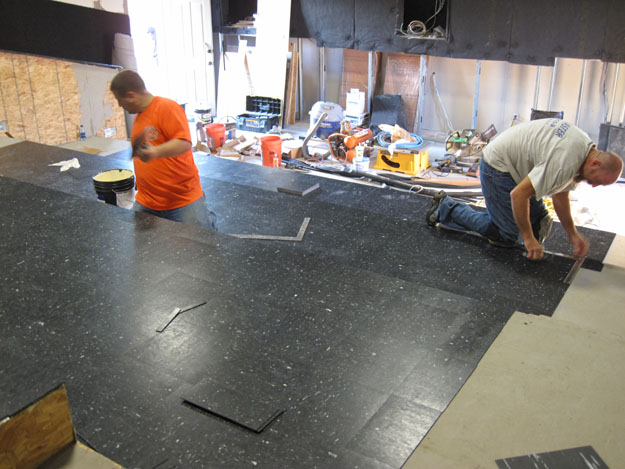 Here the final touches are added to the tile.
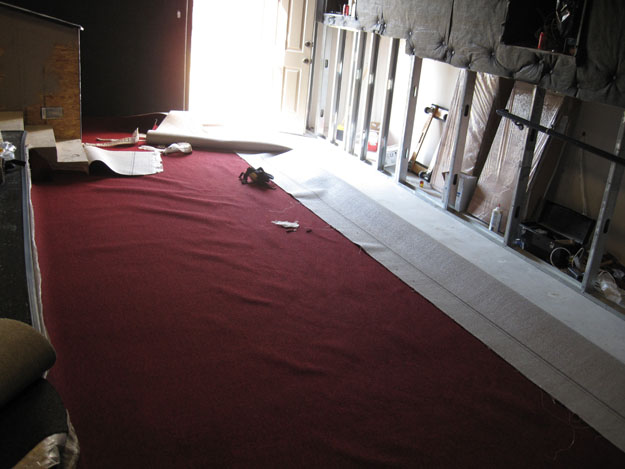 The floor carpet is also laid down.
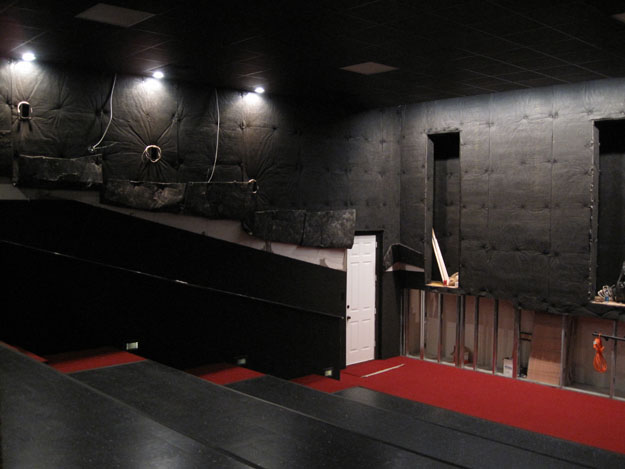 The auditorium is now ready for seats, speakers, curtains and front end.
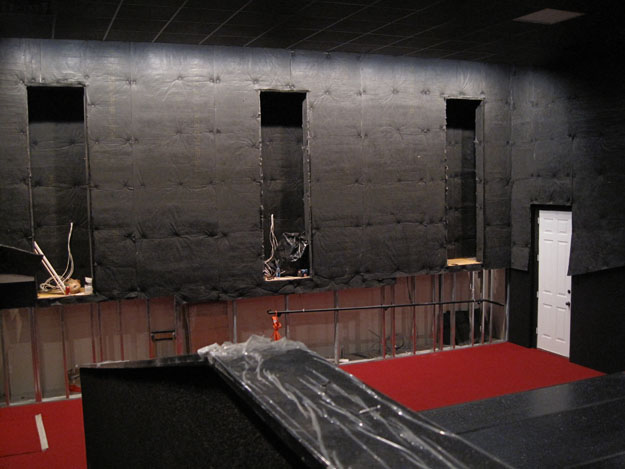 Another shot of the auditorium pre-seats, speakers, curtains and front end.
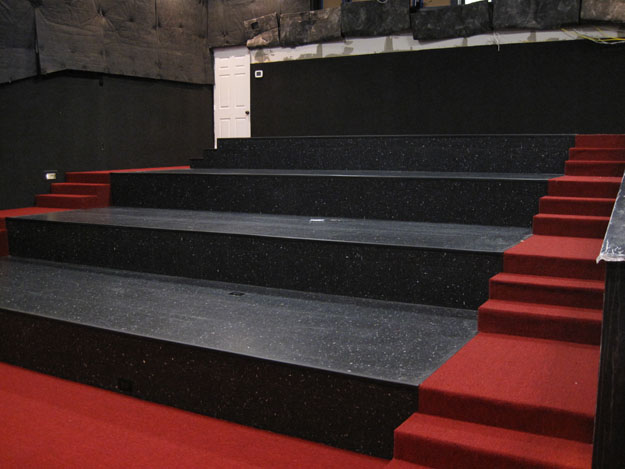 The finished riser floor.
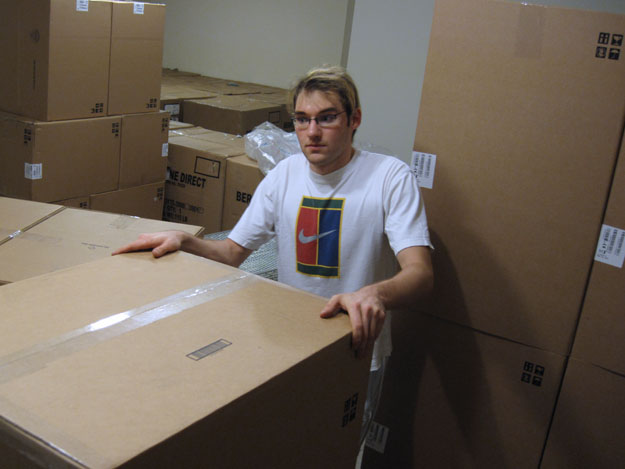 The seats and speakers have arrived. What is Josh thinking?
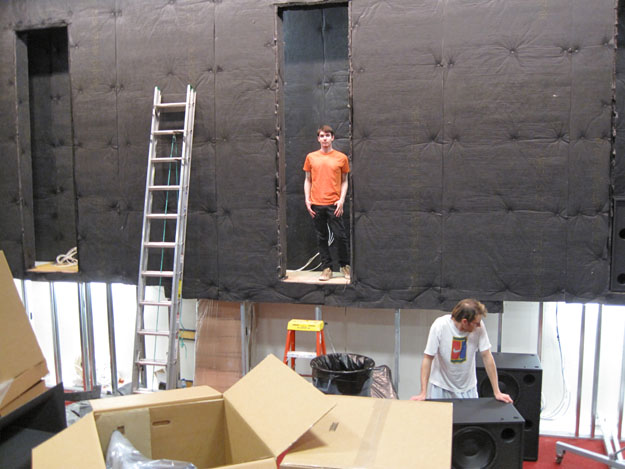 The speaker installation begins.
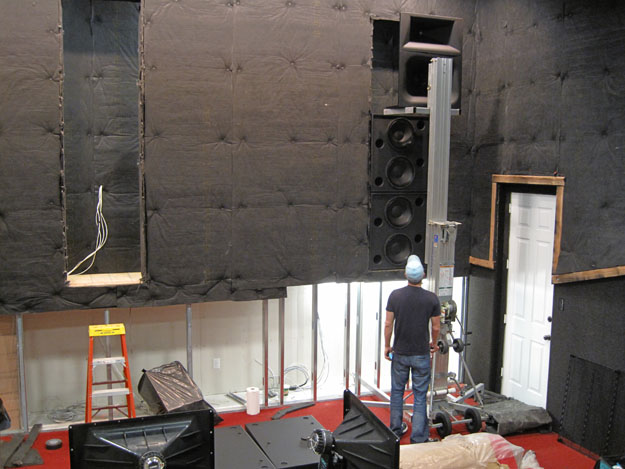 A material lift was needed to get the speakers into place.
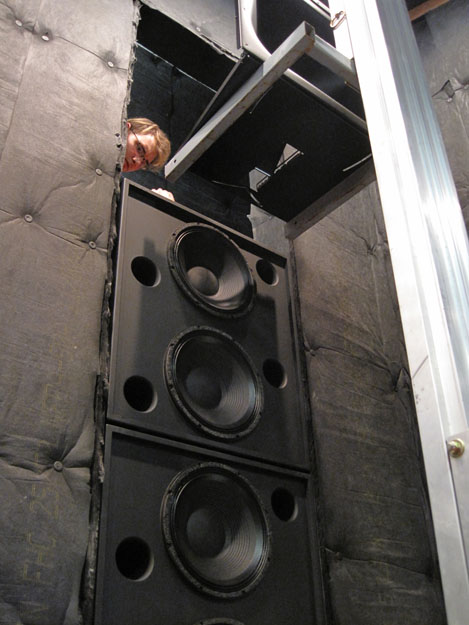 The stage speakers are assembled in place.
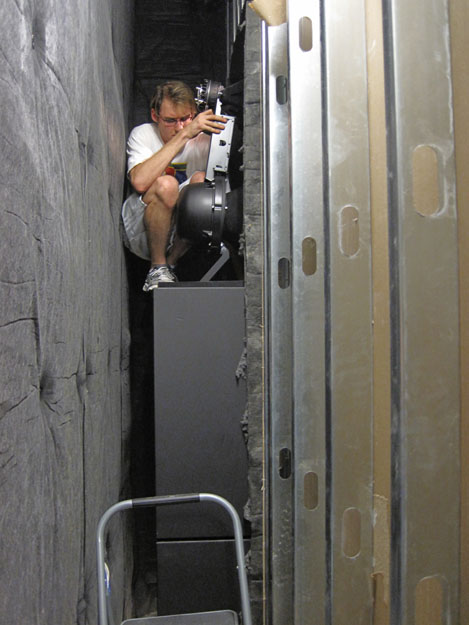 Behind the baffle wall.
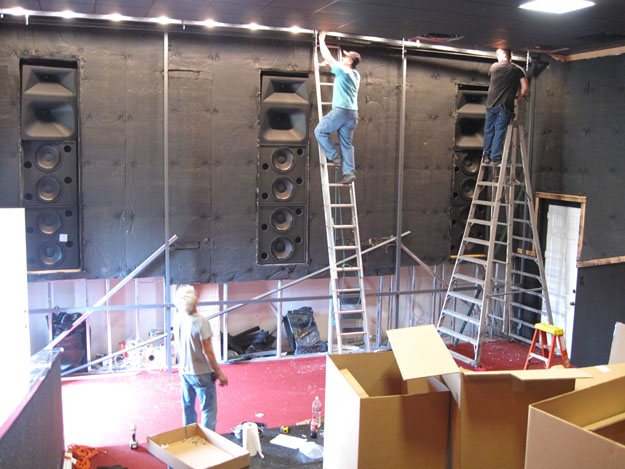 It is now time for Pickett Stage and Screen to do their thing.
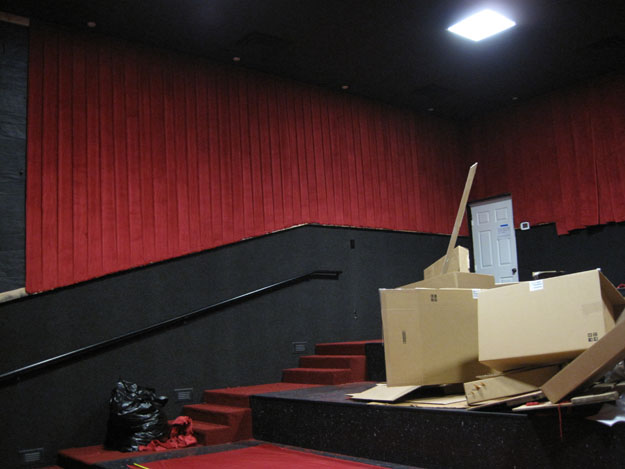 Wall curtains are installed.
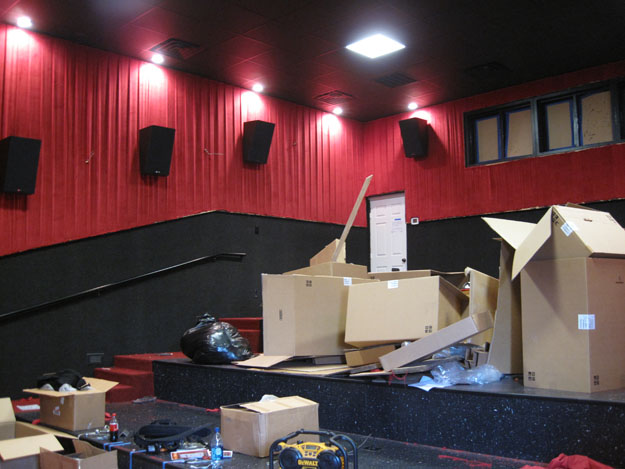 Surround speakers are installed next.
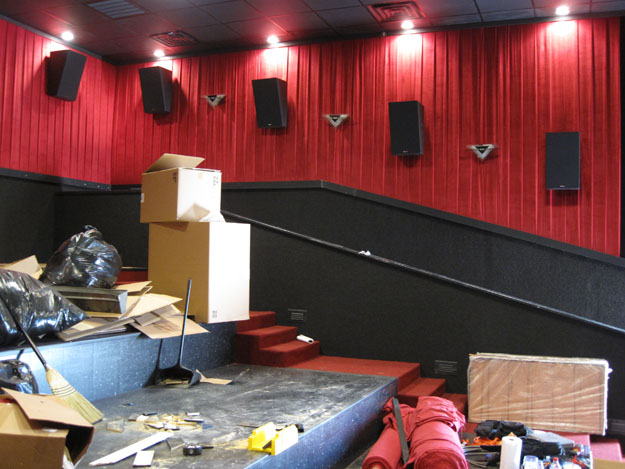 The left wall.
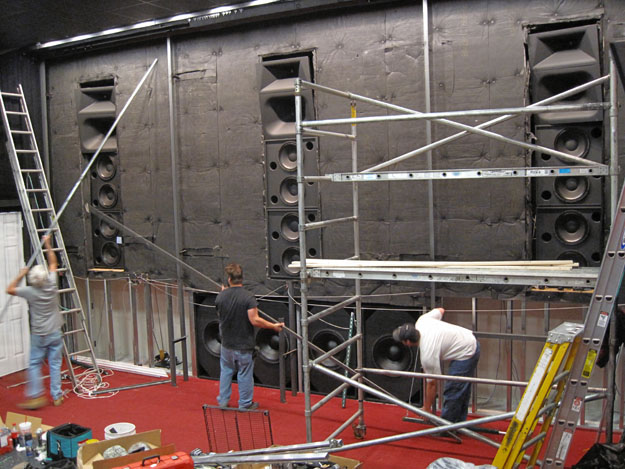 Pops, Kevin and Ed start designing the screen frame and masking system.
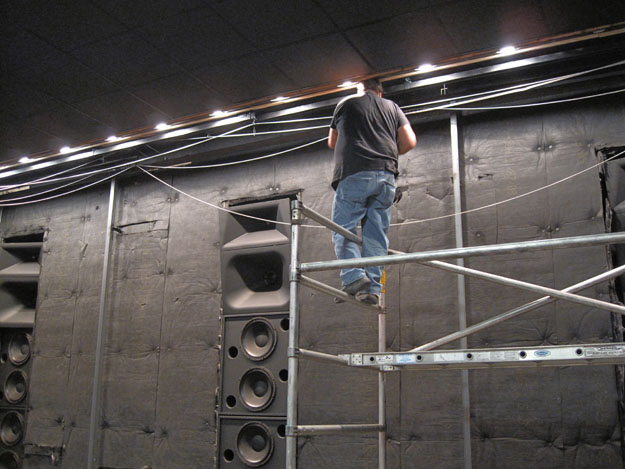 Kevin is busy prepping the curtain track.
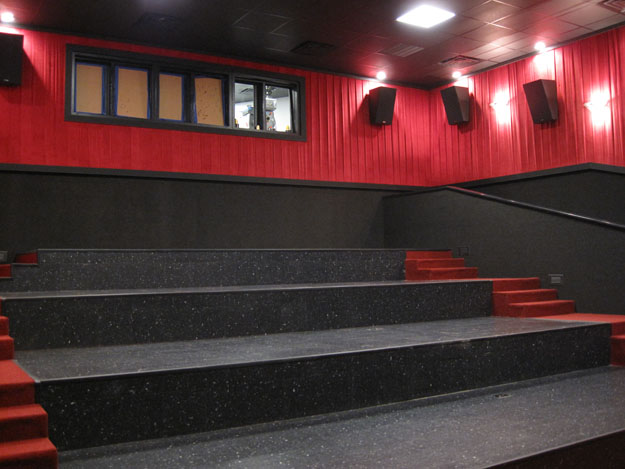 Once Pickett's crew is finished, the room is cleared in preparation for the seating.
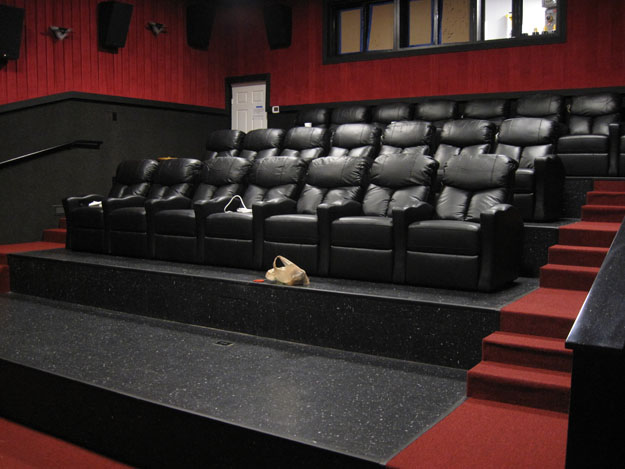 Here half of the seats have been installed.
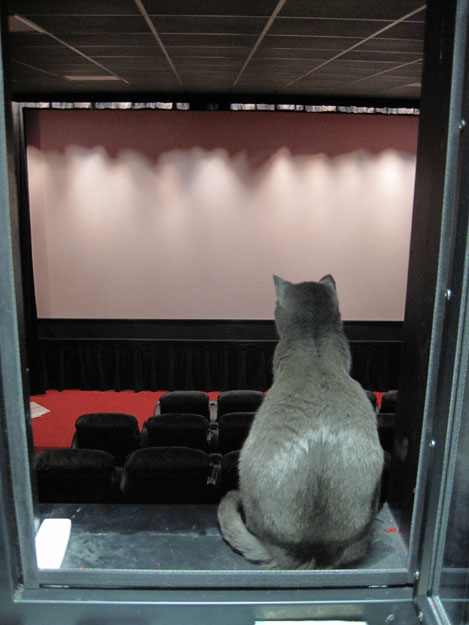 The Dude waites patiently for the last of the chairs to be installed.
 It is now time to start cutting holes in the ceiling for exhaust.
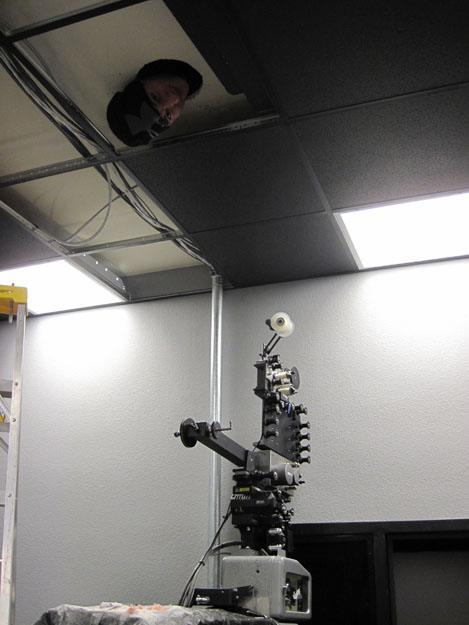 Hi Josh.
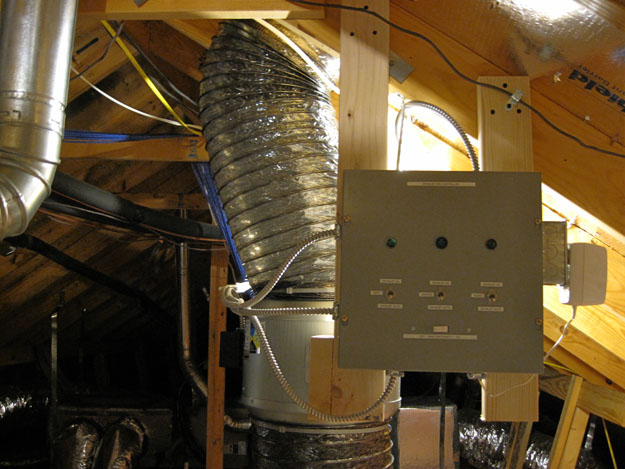 The exhaust system in progress.
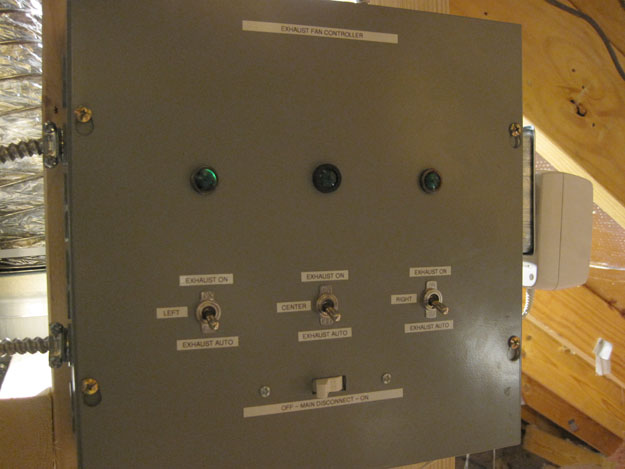 This is the override controller that is interfaced into the CA21 automations. Unlike most exhaust systems, this system turns on with the xenon lamp and turns off once the lamp cools down to a predetermined temperature, meaning they aren't extracting air out of the booth when they don't need to be (such as when the other projector is running). It saves electricity (the fan as well as the effect on the HVAC) and also keeps the booth quiet.
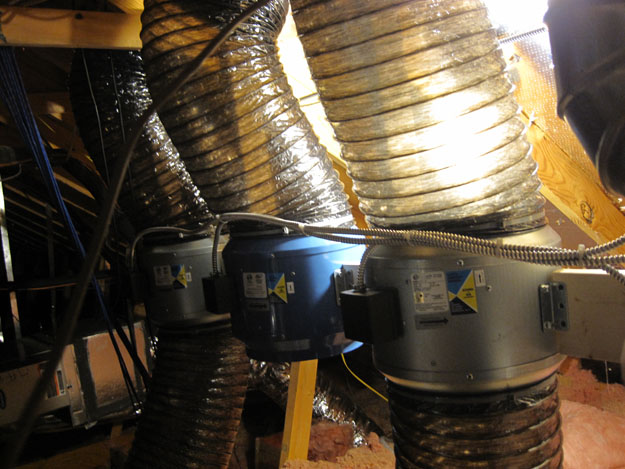 Here are the 3 exhaust fans. (At this point the middle projector has not yet been installed.)
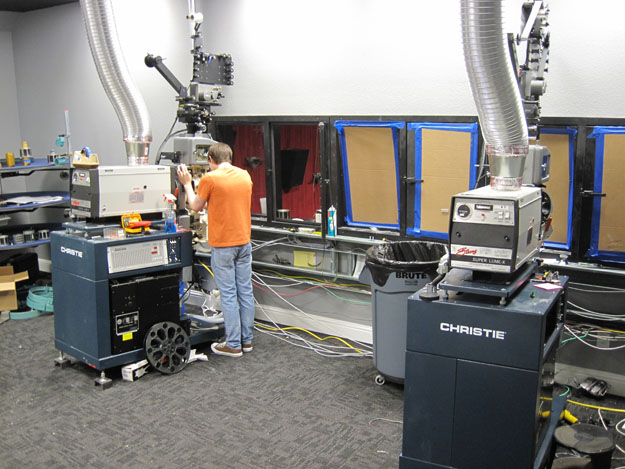 The install is getting closer to completion.
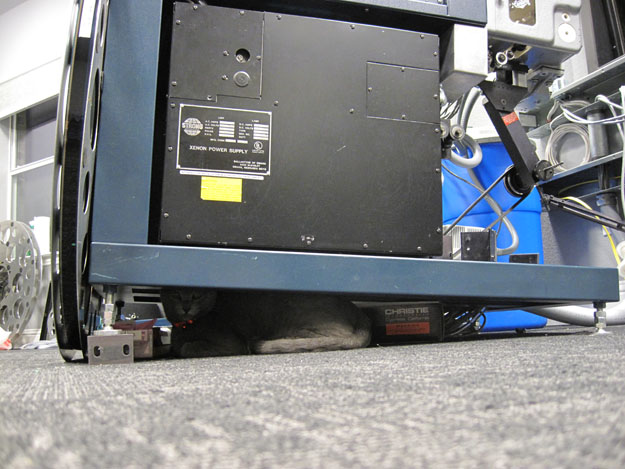 Link supervises from a safe distance.
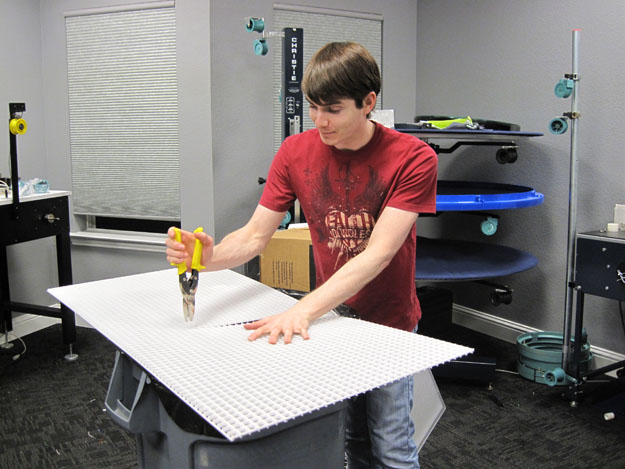 Dan prepping covers for the booth lighting.
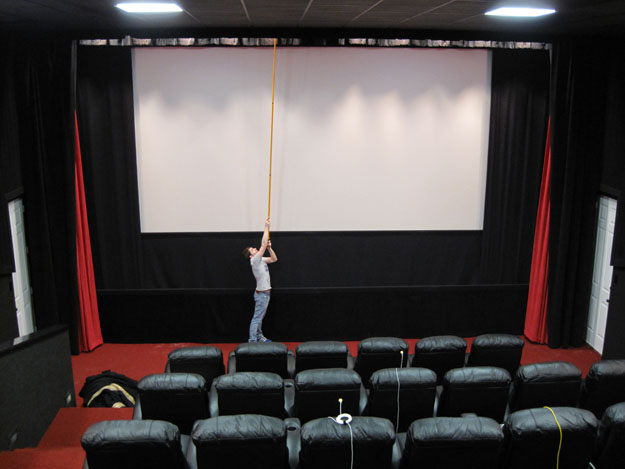 Here the room is being EQ'd while Dan replaces a bulb that has already died. You can see here that when the curtains are open they pull behind the black so the only thing the viewer sees when the curtains are open and the lights are down is the screen surrounded only by black. The masking here is side as well as bottom, to be able to precisely obtain any aspect ratio needed. (The doors will be painted black soon.)
|