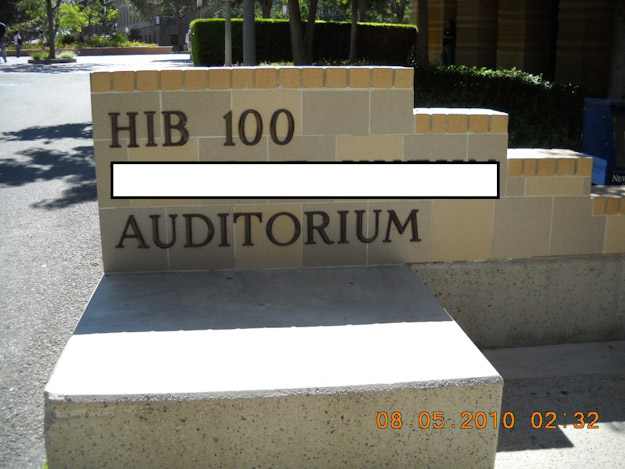 Sign outside the room. The donor’s name has been blacked out as the donor has requested their name removed from the facility. Maybe they can put my name up there now, since I’ve run it since it opened in October 1997.
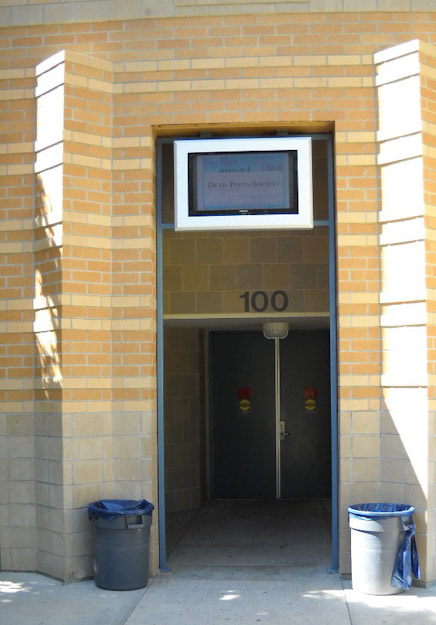 The main entry with electronic video "marquee" above. They post Powerpoint slides of upcoming events there.
 At the top of the auditorium, with the room set up for "lecture" or classroom use. There are 355 seats, stadium style, and note the large podium on the right. It is on wheels and can, with great difficulty, be moved back behind the cinema screen you’ll see later. There are two screens for classroom use, one large which covers all but 4 feet of the chalkboards on each side, and a small screen you can see on the right above the chalkboards. The house P.A. speakers are the triple cluster flown on the ceiling, and the cinema left and right are in the black boxes on each side. This sucks for reasons explained later ... additionally, all the wood panels you see on the walls make the acoustics of the room very live, and that’s a problem until over 100 people fill the seats, then it settles down a bit. The panels were because the director of the Gospel Choir got involved in the design phase and demanded them, even though the Choir’s dedicated room was slated to be opened later that year. University politics at it’s worst.
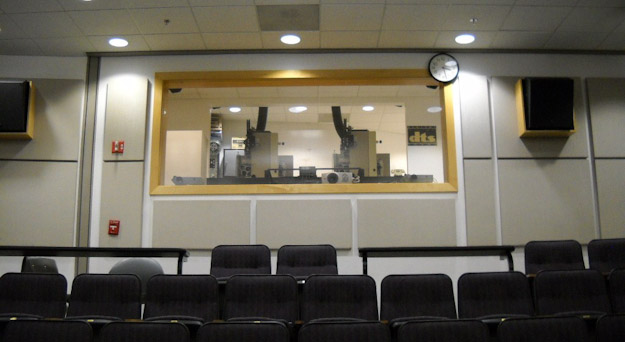 Looking into the projection booth from near the top of house. You can see the Kinoton FP38D’s and the dubber on the left. The booth has two levels and the film equipment is on the upper level. The Sanyo video projector is the grey one on the right below the #1 Kinoton. The huge window is NOT anti-reflection coated but it appears to be at least "water clear" glass ... but starfyre it isn’t.
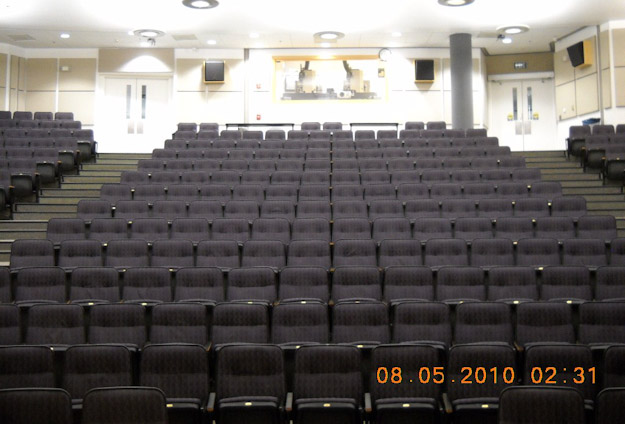 A view from the stage. Surrounds are JBL 8330. Note the fabric acoustic panels ... that’s what the rest of the house was supposed to have.
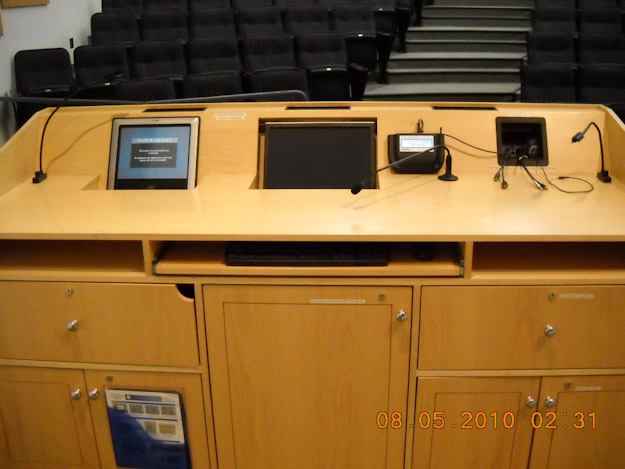 The so-called "Smart" Podium. The touchscreen allows control of all A/V functions for classes and lectures. The company who installed it still hasn’t gotten all the bugs out (and it’s been over six years!) and the tie-in to the audio is full of hum and noise ... perhaps because they didn’t know how to connect the shields on the lines. It weighs about 250+ pounds and is a bitch to move out of the way for film screenings.
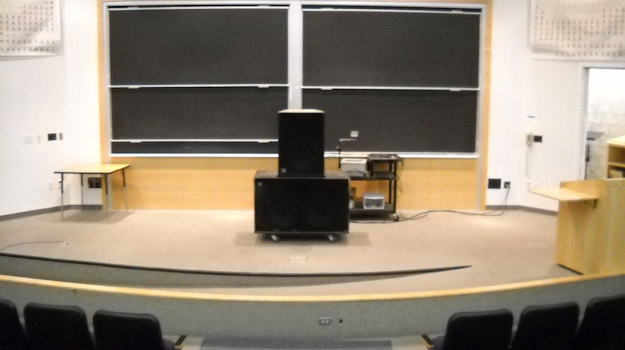 The JBL Center and sub channel speakers on the stage, prior to dropping the cinema screen. The subs are dual 18" and do a good job despite the size of the room. But there are time alignment issues as the center speaker sits about 2-3 feet back from the left and right which are mounted high up on the side walls. The power amps are in the room off to the right.
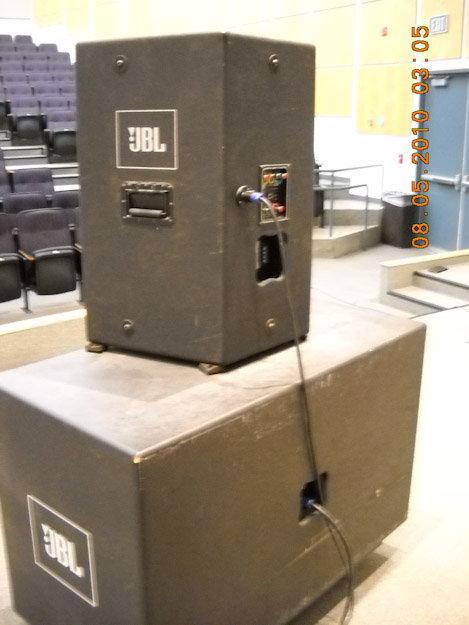 Center/sub rear view showing the crossover and Speakon cables to connect them to the sound system.
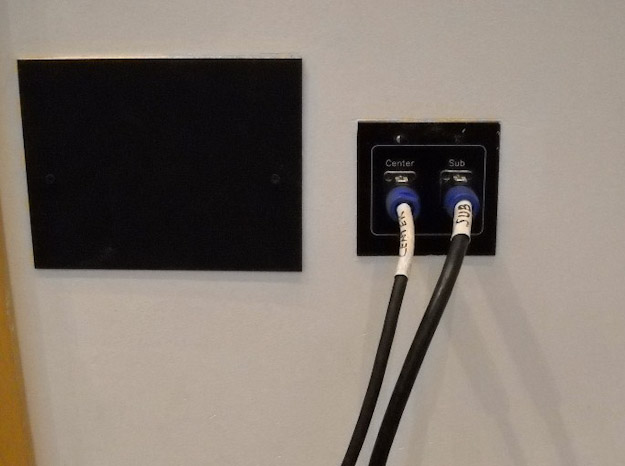 Connector panel on the stage rear wall for the speakers. The large blank panel on the left used to have video and audio connections that were removed when the "Smart" Podium went in.
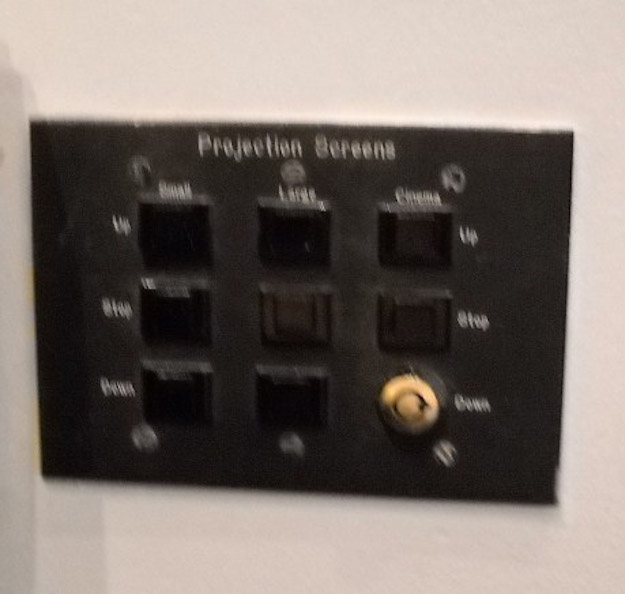 Screen controls on the stage. There is a duplicate set on stage left as well. I added the keyswitch to protect my cinema screen after a professor taped a poster to the large classroom screen ... guess what happened the next time it was unrolled?
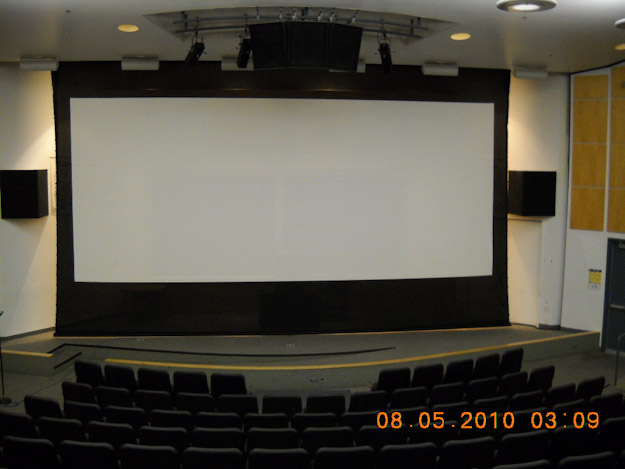 The cinema screen down, with the maskings retracted in the side wall pockets. Left and right channel speakers on the side walls. The screen is about 28’ wide and 12’6" high. Height remains constant for all formats. The screen is a Stewart with standard perfs and is a single sheet with no seams. At the time I installed the keyswitches some years ago a replacement sheet (without the motor and box) was around $40,000.00 !! Original cost of screen according to the Purchase Order I saw was around $65,000.00
 Screen with maskings set for Scope.
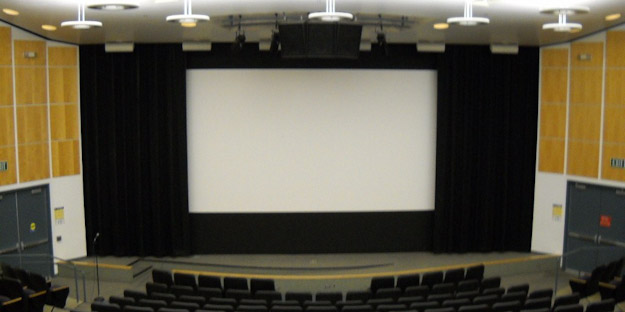 Screen with masking at 1.85 The 1.66 setting is about 2-3 feet wider.
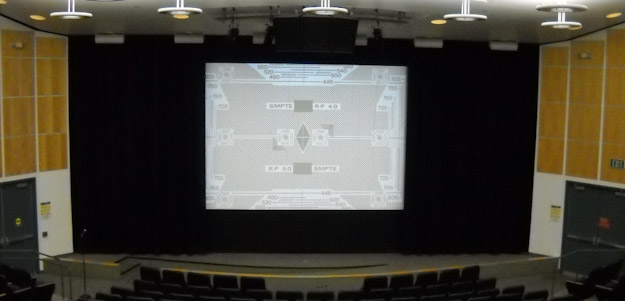 Screen with masking at 1.33/1.37 with RP-40 loop. Yes the plates are a bit off.
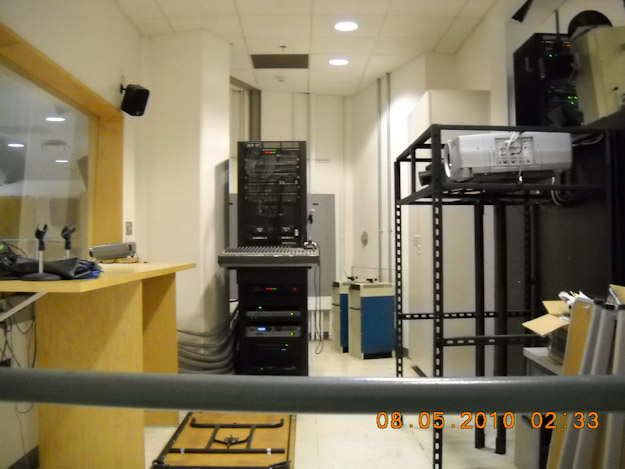 A shot of the lower level of the booth. The counter on the left used to hold the classroom A/V gear and video projector, the rack shown runs all the classroom A/V functions. The Yamaha mixing board is now a huge paperweight as no one uses it anymore (but it is still hooked up and active) and the patchbays give access to ALL of the audio, including the outputs of the Cinema system. On the right you see the racks holding the video projectors (mine and the classroom) and in the back you can see the IREM rectifiers for the 16mm lamps.
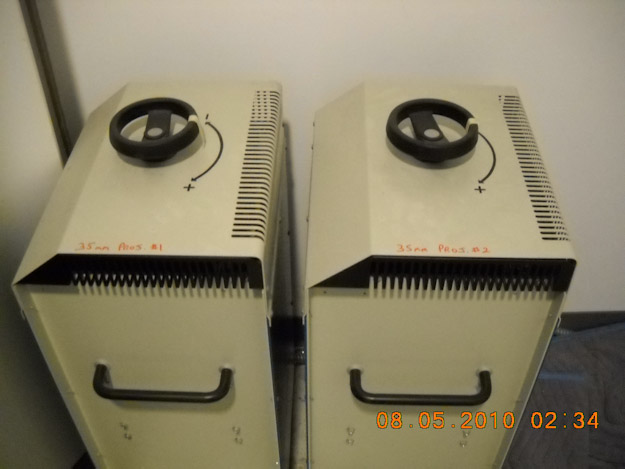 The 35mm Irem Rectifiers. They are behind the A/V rack shown in the previous pic, as are the breaker panels for the booth and room.
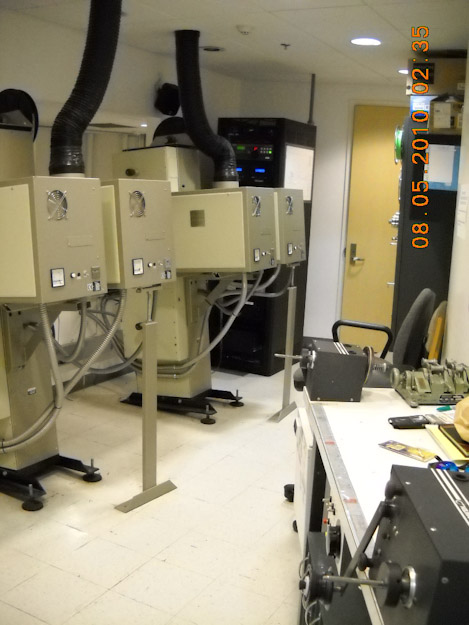 The upper level of the booth, my exclusive domain since 1997. You can see it is a bit tight, and the wall on the right is shaped like a grand piano which wastes even more space. The rewind bench is a Kelmar 8900. Space between the #2 projector and the rack is a sparse 26", so no fat people allowed!! Even I have bumped into the rack while threading.
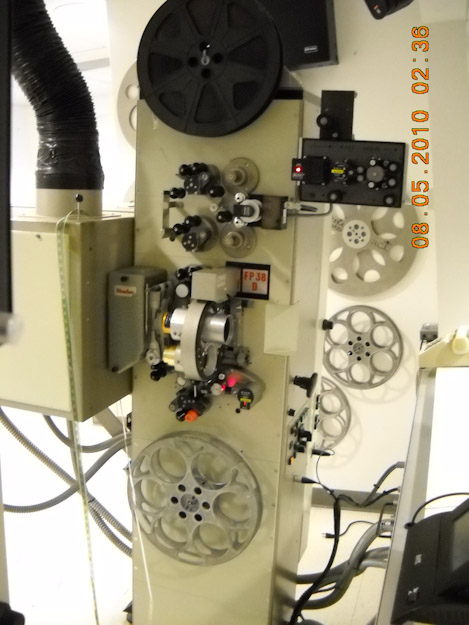 The FP-38D, 35mm film side. BACP Reverse scan readers were donated by me about six years ago. RP-40 loop hangs on lamphouse prior to setting the 1.37 lens. You can see the DTS reader mounted where the old 4-track mag was (It was set up poorly due to the lens turrets, and the sound would have been way out of sync) and the BACP reader with film cleaner bracket mounted to the front. More on the DTS and DD later. The lens turrets are a huge pain in the butt, as they and the apertures never seem to index to the same spot twice. A huge waste of money as we rarely run more than one film in a show and don’t need rapid lens changes. There was even a Kinoton Pin matrix automation!! It was never connected and the University gave it to me. I still have it, brand new and never used. The money wasted on the 4-track, turrets and automation could have been better spent on other things ... like digital sound (I added it later) and perhaps even 70mm capability.
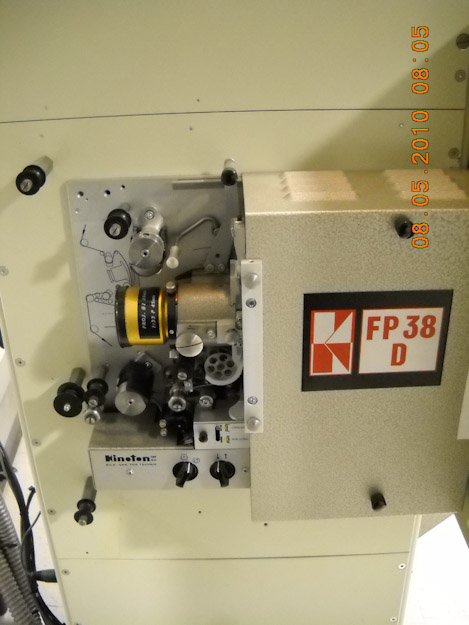 The FP-38D 16mm side. The picture this puts out is bright and steady, but the sound has a major issue ... the whine from the inverter driven motor gets into the sound. After a lot of digging I found it to be a mechanical vibration of the exciter filament (microphonics for you old-school guys) and part of the problem is the solid motor mounts. Even Kinton hasn’t been able to come up with a solution. I run all 16mm films on large reels as it is easier to build them up during inspection than run changeovers IMHO.
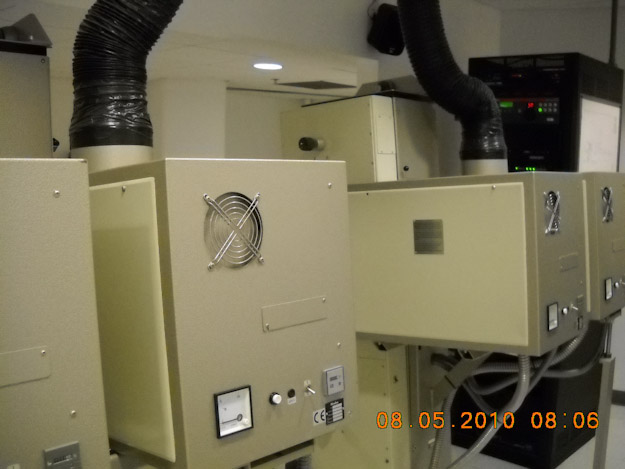 The dual lamphouses on each machine. We run Christie CXL 16 bulbs and after 13 years the 35mm machines have just passed 875 hours. The highest hours on the 16mm is machine #2 with around 105 hours. The 35mm lamps run at 70-75 amps and have the external exhaust and the 16mms run at around 65 amps. The booth exhaust in this room is part of the facility HVAC and it has shut down on me during screenings, and as a result the #2 35mm reflector is badly damaged. The University is still arguing about who’s gonna pay for the replacement.
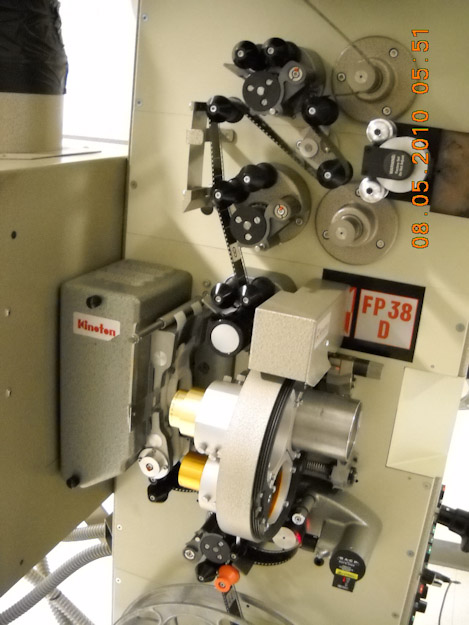 35mm Optical thread-up. Kinoton purists will note that I have taken quite a few liberties with the factory threading pattern. This has proven to work well with NO damage at all to any film. In fact, my simplified threading is easier on the film than all the bends and roller contact Kinoton specifies.
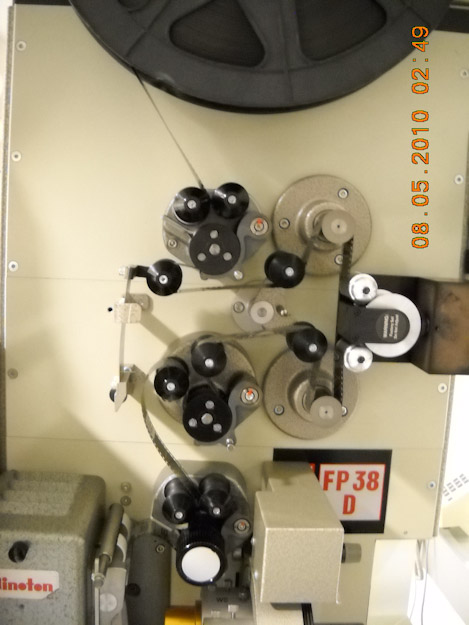 DTS Digital thread-up. The use of the old 4-track mag path provides rock-steady timecode output, verified with a 'scope. It took some thinking to make it easily repeatable to keep loop sizes and sync constant. We don’t see a lot of DTS prints though. The DTS system was very generously donated by DTS circa 1998.
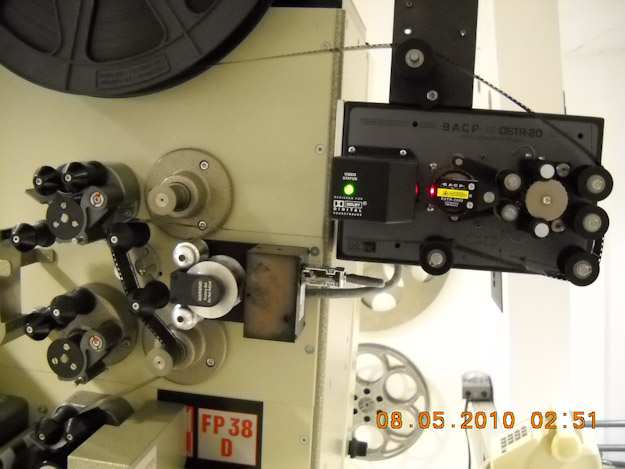 Dolby Digital thread-up. I am extremely unhappy with my effort here as the path forces me to use the "rocker" rollers (to the immediate left of the DTS reader) with the end result being a LOT of "wow" in the film motion over the BACP reader. I will be installing a bracket and a pair of rollers to shoot around all of that and make things a bit steadier. If I get really ambitious I will devise a way to get through that upper feed sprocket first to isolate the reel’s motion from the BACP reader altogether.
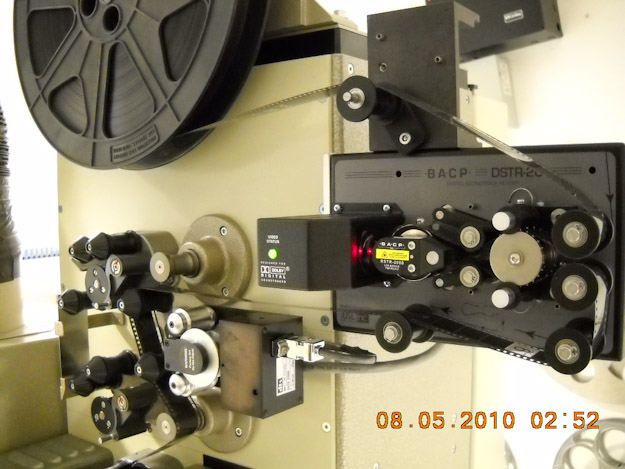 Another angle of the Dolby Digital threading.
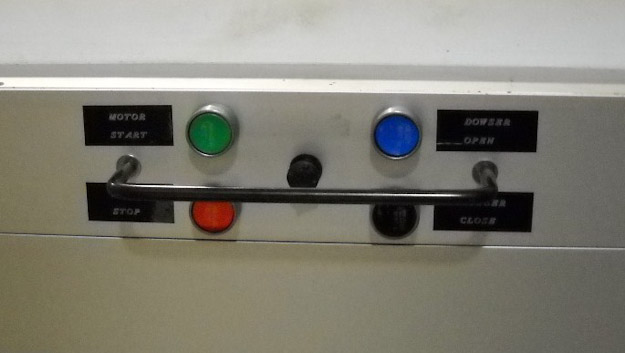 Projector control panel I made some years ago. Before I had to reach around the front of the projector column during changeovers. The buttons originally talked to the projectors directly, but now talk to the AMX control system.
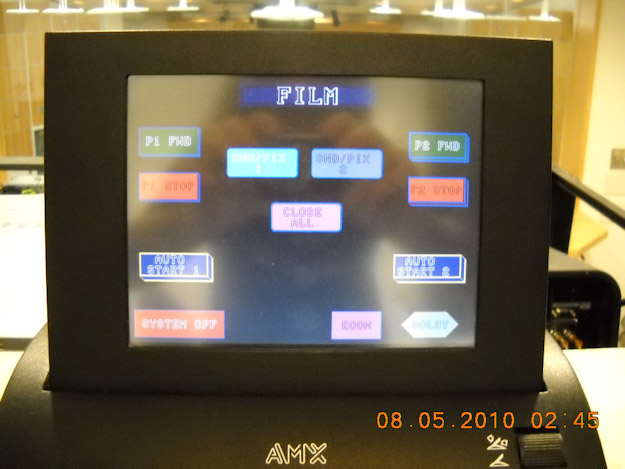 AMX Touchpanel film page. This is an older AXCESS series system, which I donated to the University. I have found some shortcomings in the layout which I need to change. The "AutoStart" buttons will be programmed with a macro to play a short music clip, set lights to "entre act", start the respective projector, then do sound and image changeover and lights out to start the show perfectly every time. In my other room at UCI it will also control the curtains.
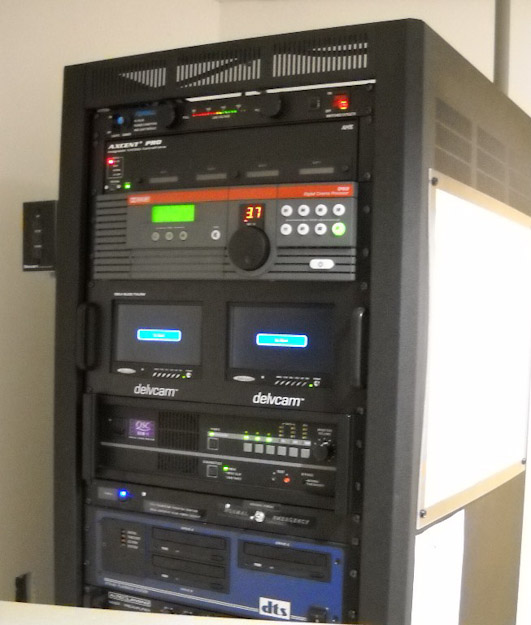 Top part of the film sound rack. From Top: Furman power conditioner, modifed by me to have switched outlets controlled by AMX; AMX AXCENT3 Control server; Dolby CP650 with EX (which we don’t use as the surrounds aren’t wired for it and cannot be changed); DEVLCAM dual video monitors; QSC DCM-1 Monitor (which is simply looking at the processor outputs, it is not feeding the amps or getting speaker returns); Power supply for the BACP Reverse scan readers, built by my company TPA TransCom; and DTS-6D player donated by DTS. The AMX, CP-650, DCM and DEVLCAM monitors were donated by me this past January.
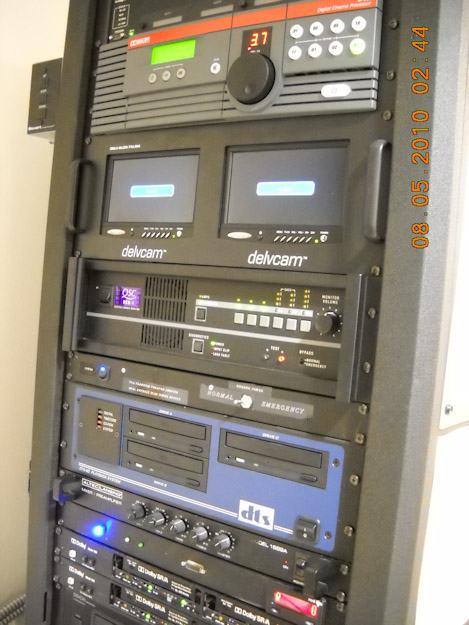 Middle part of film sound rack. Showing the ALTEC mixer for 16mm sound, the custom Dubber interface panel built by TPA including a rate display (far right). Dolby CAT 363’s at the bottom.
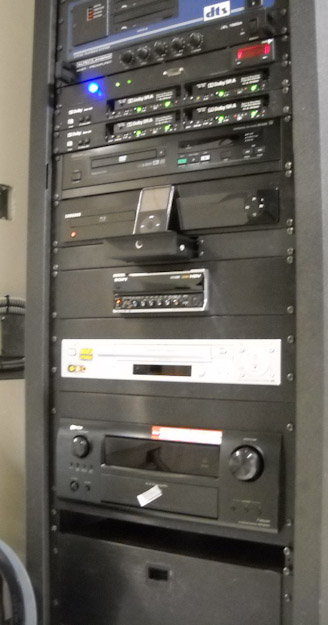 Bottom part of the film sound rack. Dolby CAT 363’s for the dubber (donated by me); Denon DN-V310 region-free DVD player; (following items donated by me) Samsung BDP-1500 BluRay Player; RAXXcess iPod dock; Sony Mini DV/HDV deck; Sony worldwide VHS deck; and Denon AVR-3801Ci AV receiver which controls audio and video switching for the video sources.
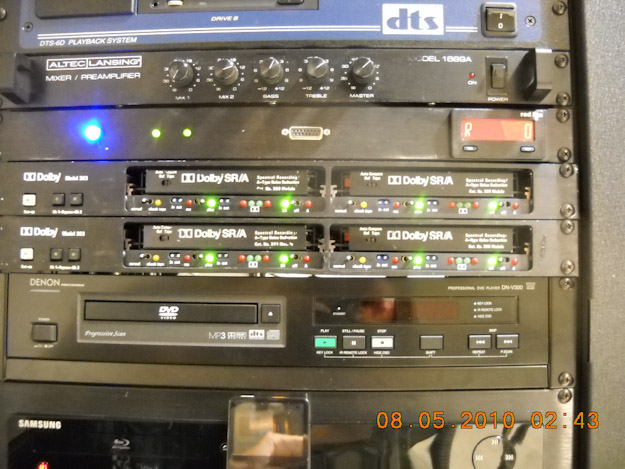 Closer look at the Dubber Interface and Dolby CAT 363 frames. On the interface, the blue LED is power, the next two are red/green LED’s connected to the encoder busses and change state when the projector is running. When idle, they can be red, green, or dark. The DB15 connector allows interface to digital dubbers or hard drives for dailies work, and also carries the changeover signal. The display on the right shows the speed of the active projector. Since I programmed it wrong it reads "240" at 24 fps ... oops. But that allows accurate reading to the tenth of a frame, so maybe I’ll leave it alone.
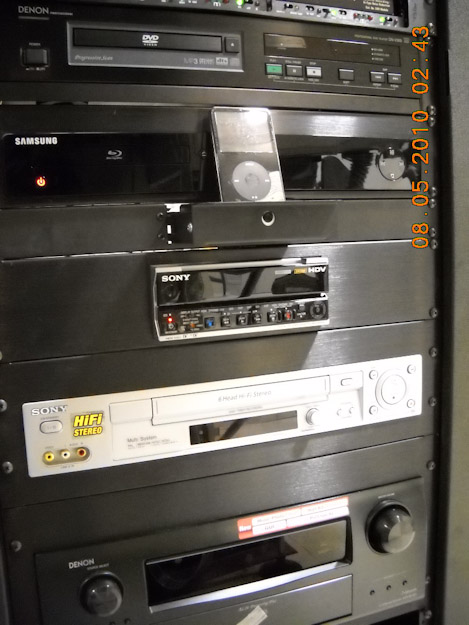 A closer look at the video gear.
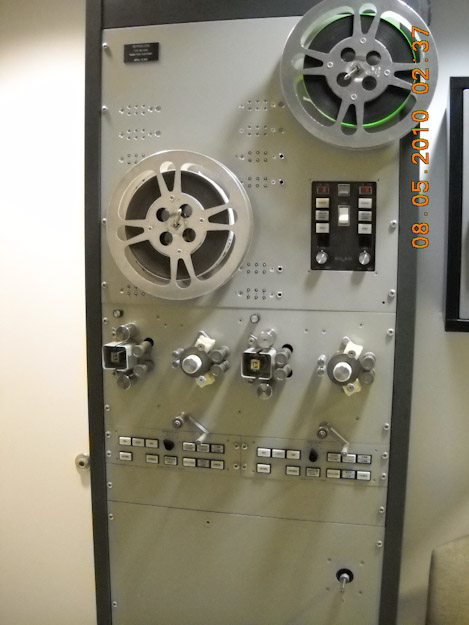 Magna-Tech dual dubber with test reels one picture and one track. I am in the final stages of getting this thing active. Inside the back of the sound rack I have an audio selector switch and patch bay to route the audio from the dubber to the Format 11 external inputs to the CP650. I have the mate to this dubber in my garage.
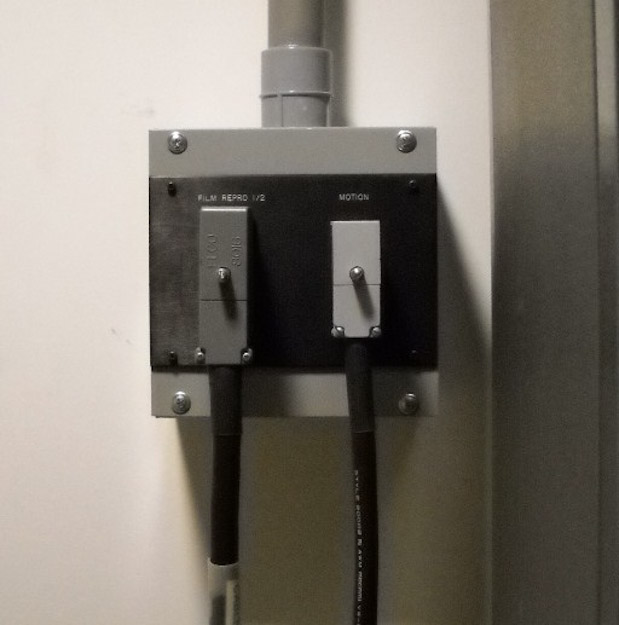 Close up of the dubber Audio and encoder connector panel. I cannot take credit for it, it was made by the studio that gave me the dubbers. A nice clean interface, well done.
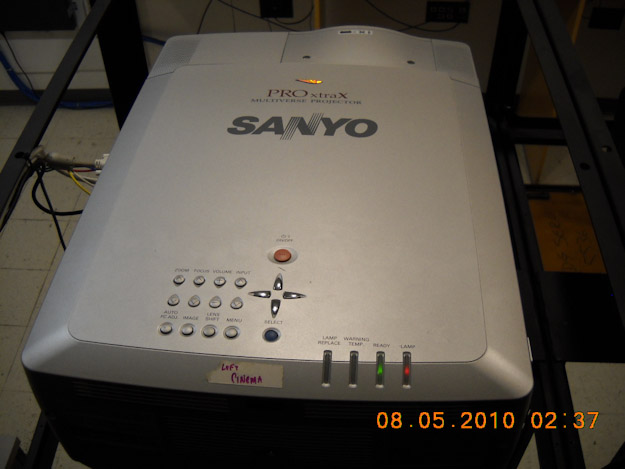 The Sanyo video projector for all of my video. Coolest thing is the lens has the zoom range to let me fill a wide screen when videos are letterboxed. The University provided and services this projector. Images are bright and sharp with good contrast, not DLP quality but so far every director/filmmaker has been very pleased with how their video looks here.
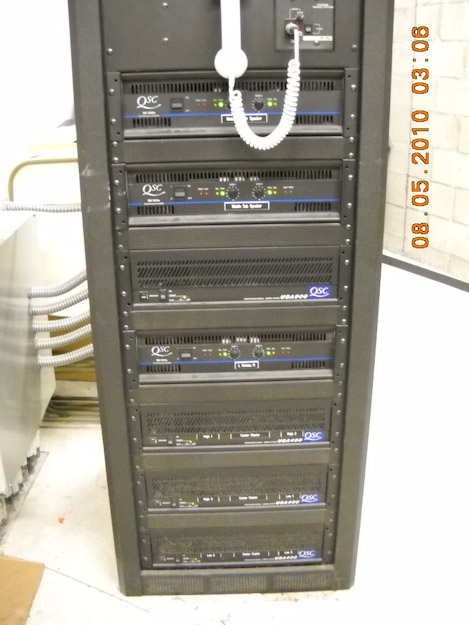 The room’s audio amps are all located in a room behind the chalkboards. All amps are QSC. From top to bottom: Center, Sub,(Both MX3000a) Surrounds (USA900), Cinema Left and Right(MX3000a), P.A. Cluster 1, 2 and 3. (USA 400) All speakers are passive crossovers except P.A. As you can see it’s time to get the dust out of the amps again.
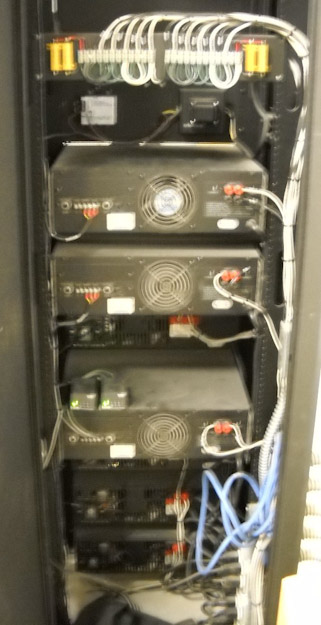 Rear of amp rack showing the surround array wiring with dummy resistors to even out the "speaker count". Surrounds were originally wired from the booth as mono (Previous processor was CP-65, the one now in my screening room) with no digital sound. When I added the DTS I had to trace out an extra 8451 audio line to do the split. There are no more spare audio lines for me to do EX so there it is.
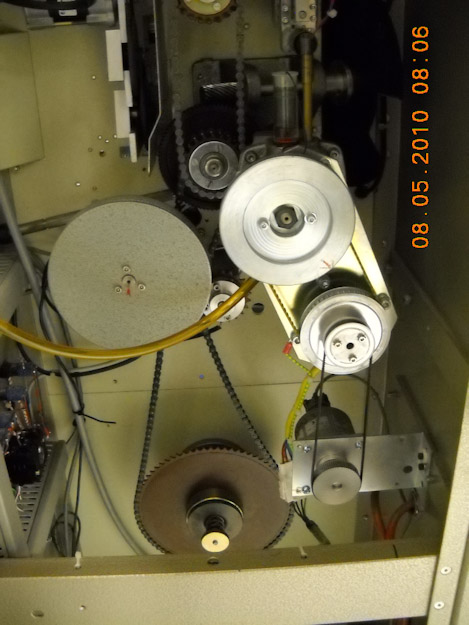 Dubber encoders mounted in the FP-38D’s. I fabricated the bracket and with the help of a local machinist made a jig to get the encoder pulleys mounted to the original motor pulleys. Encoders feed at 10 pulse/frame. Note the gigantic sprocket on the take-ups ... these are "standard" frictions, not the accelerated frictions I really need to get a tight wind on standard reels or cores.
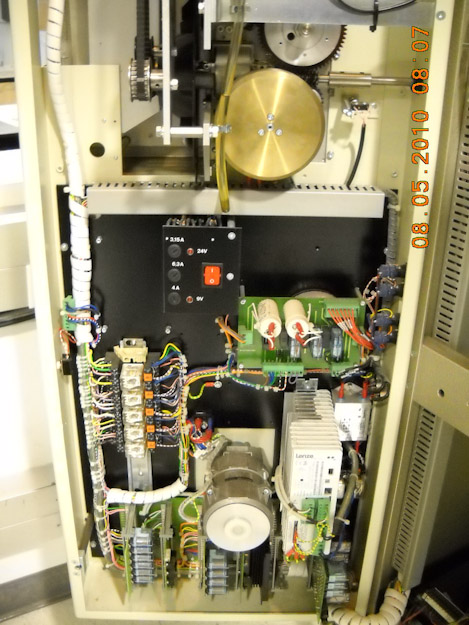 A shot of the FP-38 control electronics mounted on the 16mm mechanism "door". So far only trouble in 13 years has been speed selection relays failing.
|